JACQUET Midwest has set up a dual head 5-axis Jet Edge EDGE X-5® waterjet cutting system at its metal processing facility in Racine, Wisconsin. The EDGE X-5 is the third Jet Edge system of JACQUET Midwest and is the 13th Jet Edge waterjet nationally.
JACQUET supplies and processes nickel alloys and stainless steel for fabricators, OEMS, and machine shops that mainly support the oil and gas, pollution control systems, power generation, and water purification industries. The company’s North American service centers offer waterjet as well as plasma part cutting. JACQUET stocks 19 different grades of nickel and stainless steel alloy plates in a wide range of sizes and thicknesses.
JACQUET intends to employ the new system to offer near-net shaped stainless steel parts with compressed lead times to its Midwest and nationwide customers. The chamfering and beveling capabilities of the system’s 5-axis cutting head will enable them to bring new opportunities to JACQUET’s four domestic regional service centers. The “lights-out” cutting package maintains value-added production even when the machine is unattended.
.jpg)
The 5-axis Jet Edge Edge X-5 has a proprietary plate mapping feature that allows precise nozzle-to-plate sandoff.
The waterjet system includes a 21’x13’ work envelope, which allows the metal service center to process full 10’x20’ or 8’x20’ plates. Its dual 5-axis cutting heads boost their production by two-fold and can cut precise 3D parts from almost any material, including bevels up to 50°.
Jet Edge iP60-100 Intensifier Pump
The ball-screw driven waterjet system is powered by a 60,000 psi, 100 hp Jet Edge iP60-100 intensifier pump and it has the best repeatability in the industry at +/- 0.001”. The system has submerged or above-water cutting capabilities, and also a proprietary plate mapping feature that enables precise nozzle-to-plate standoff.
We’re really excited to bring the Jet Edge dual head 5-axis waterjet into our facility. With the precision that we’ll be able to achieve, we can provide a tighter tolerance part from the top edge to the bottom edge, eliminating a lot of the machining. It allows us to do much more for our customers…we can bevel cut, taper control, and chamfer holes on both the top and bottom edges of the material.
Dan Chatterton, CEO, JACQUET Midwest
.jpg)
A Workhouse Waterjet System
Chatterton added that JACQUET has always equipped its service centers with large gantries in order to serve its customers better. JACQUET distinguished itself even further when it decided to add a 5-axis system to its collection.
All of the machines in the JACQUET system are large table machines because of the large plate sizes that we buy mill-direct. This allows us to be more efficient with our cuts, have longer run cuts, and have better nesting. Our dual 5-axis system is going to provide an even higher level of service to our customers, allowing them to look to JACQUET for all their cutting needs.
Dan Chatterton, CEO, JACQUET Midwest
The 5-axis Jet Edge EDGE X-5® is a workhouse waterjet system designed to offer years of reliable service. Its robust design separates the motion system from the catcher tank, eliminating vibration and guaranteeing maximum part quality. This system will help JACQUET Midwest to maintain its reputation of knowing what works, when it works.
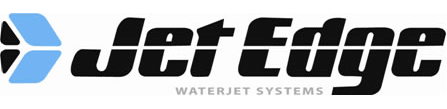
This information has been sourced, reviewed and adapted from materials provided by Jet Edge.
For more information on this source, please visit Jet Edge.