When Tualatin, Oregon-based company Plasti-Fab, Inc., signed a contract to cut hundreds of circles out of 8,000 pound fiberglass plates, it decided that abrasive waterjet would best complete the job. The company had to identify two things: a waterjet manufacturer that can build a 14’x28’ waterjet table and a system that can be installed outdoors — Plasti-Fab’s building already had two CNC routers and no space was available.
Jet Edge’s iP60-50 Intensifier Pump
Wade Oxford, CNC Supervisor at Plasti-Fab, informed that after researching a number of waterjet systems, only Jet Edge of St.Michael, Minnesota, was able to deliver the large system they required. The company chose Jet Edge’s Mid Rail Gantry that features a pinion drive-rail motion system and a rugged floor-mounted rack. The waterjet system — the largest in the Northwest — is powered by Jet Edge’s 50-hp iP60-50 intensifier pump, rated for 60,000 psi.
Plasti-Fab set up the system under a steel awning fitted with a hoist and then added a retractable solar blanket and a swimming pool heater to the waterjet tank to maintain the temperature of the water between 68 and 74 degrees throughout the year.
.jpg)
To keep the water between 68 and 74 degrees year round, Plasti-fab added a swimming pool heater and retractable solar blanket to the waterjet tank.
Jet Edge Waterjet System
According to Oxford, the Jet Edge waterjet system cuts the parts much faster when compared to cutting the parts with a hand router, which produced poor results following a week of tests. It took them around a week to make 28 holes, but now with the Jet Edge waterjet system they can make 212 holes in just four hours. Oxford also remarked that he can easily prevent delamination of his layered fiberglass parts by simply running a pre-piercing operation before cutting the circles.
This huge project has helped Plasti-Fab grow from 45 employees to 105 employees in just a span of two years. In addition, Plasti-Fab uses its waterjet system to cut neoprene parts for its gates department and steel parts for its metal shop. The company also produces many wastewater treatment products such as shelters, flumes, manholes, gauges, stop logs, gates, and skimmers.
.jpg)
Plasti-Fab runs its waterjet system five days a week, 10 hours a day. This project has to maintain a tolerance of 1/16 inch over 24 feet, which can be easily achieved with an automated waterjet system.
According to Oxford, the Mid Rail Gantry is very accessible and easy to load. He along with Plasti-Fab Waterjet Operator Don Logan can load or unload the table within an hour by using a hoist and two forklifts to maneuver the parts into position.
It was easy to learn and operate. I’ve been very satisfied with the system and follow-up service since it was installed. I’ve been able to pick it up in four months. I am extremely happy with the service from Jet Edge. In fact, I am floored with their response.
Wade Oxford, CNC Supervisor, Plasti-Fab
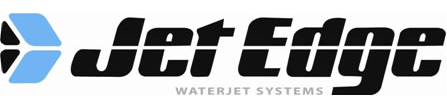
This information has been sourced, reviewed and adapted from materials provided by Jet Edge.
For more information on this source, please visit Jet Edge.