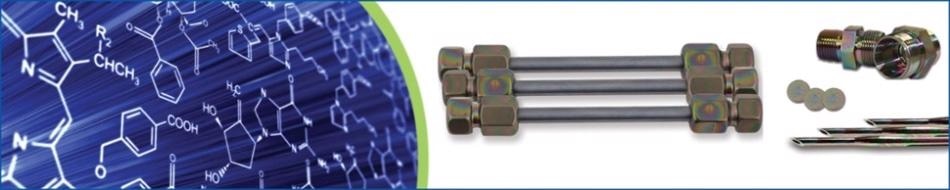
Many organizations and individuals believe that stainless steel and PEEK are ideal for HPLC analysis, but this is not always the case. The use of these materials can lead to flow path components and columns having to be replaced due to corrosion, carryover or cross contamination, adsorption or tube swelling, all of which can have an adverse effect on the process.
This article explores alternatives to these materials, and how these can help reduce system maintenance and test failures whilst improving analytical column performance.
Why an Inert Flow Path Is Critical to HPLC Applications
Non-reactive materials (stainless steel is not non-reactive) should always be the first choice in HPLC sample transfer systems in order to ensure consistency. As well as consistency, there are many other specific benefits of utilizing a non-reactive surface:
- Reduced costs and downtime
- No need to repeat tests again
- Gain an accurate profile of all components, both reactive and non-reactive
- Trustworthy results
- No false negatives
- No additional molecules or ions are introduced
Consistency is the key factor in all these benefits, whether this is in terms of financial consistency, consistency of quality or test consistency. In fact, consistency is the central reason that an inert HPLC flow path is essential.
The Enemy of Consistency, Stainless Steel and PEEK
Stainless steel or PEEK tubing can solve a range of sample transfer problems and while at first glance this may be an ideal solution in terms of availability and cost, it does not guarantee continuing reliability, meaning that in the longer term, these solutions may not be the best choice in terms of investment.
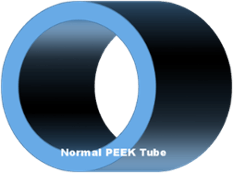
Stainless steel and PEEK will eventually begin to show problems, including the following:
Stainless steel can suffer from corrosion, abrasion and chemical reactivity; all problems which can lead to the introduction of additional molecules and ions to the sample and thus potentially corrupting results. Other issues with stainless steel can include:
- Protein fouling or carryover
- Acid corrosion (especially with halogenated solvents like HCl, HBr)
- Highly reactive towards chelating agents
Additionally, use of PEEK can result in solvent damage and limitations in temperature that can lead to inconsistent pressures, potential delamination, flow issues and even failure. Other PEEK issues could include:
- Halogenated solvent damage
- Temperature limitations (Tg = 148 °C)
- Acetone, THF and other organic solvents can cause swelling
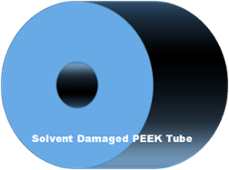
Other options are available however, not least using Dursan® to ensure that tests run smoothly, every time.
Dursan® Material Properties
Stainless steel and PEEK are not perfect, but they remain a reasonably good choice for a range of HPLC applications. Dursan® can help to improve the consistency of tests undertaken in challenging conditions, or when flow paths may be exposed to organic solvents prone to causing swelling.
Dursan® is a silicon, oxygen, carbon coating that can be bonded to stainless steel flow paths using chemical vapor deposition. It can be adhered to any surface that a vapor molecule can reach, including inner bores of needles or sintered metal frits.
In practice, this means that it is possible to maintain all the structural benefits of stainless steel such as high pressure capability, heat resistance, ease of working and low cost; then combine these with the non-reactivity of a plastic free coating. Other material benefits include:
- Usable in wide pH range: 0-14
- High temperature stability of up to 450 °C
- Molecularly bound to the substrate guaranteeing outstanding adhesion
- Inert to most chemicals
- Twice as wear resistant as 316 stainless steel
How Can Dursan® Make a Difference in HPLC Flow Paths and Columns?
When comparative tests of the corrosion-resistant HPLC coating Dursan® were run alongside uncoated stainless steel, corrosion rates were reduced by a considerable amount. More specifically, ASTM G31 hydrochloric acid immersion of test coupons illustrated that the stainless steel surface corroded 170 times faster than a surface coated with Dursan®. Overall, this gives a much lower chance of contamination alongside improved flow path life. In summary this test showed:
- ASTM G31 guidelines
- Over 170x improvement with coating
- 20% (6M) HCl room temperature immersion 24 hours
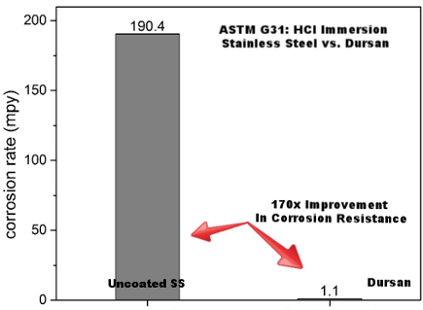
HPLC Inert Surface
The comparative chromatograph below highlights the following:
- Tetracycline has a range of potential chelating groups
- Dursan® coated column shows improvement in peak shape
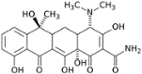
The resolution quality of tetracycline on a stainless steel column was compared to a column coated with Dursan®. The Dursan® coated column improved the peak shape considerably.
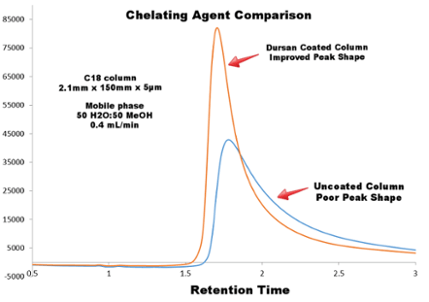
Prevent False Positive Tests and Carryover Contamination
As well as the benefits discussed above, studies by Abbott Laboratories on non-specific protein binding have shown a reduced risk of protein sticking and carryover when using Dursan®.
As can be seen in the image below, a QCM-D (Quartz Crystal Microbalance with Dissipation monitoring) study was undertaken. A thin layer of 316L SS was coated with Dursan® before protein solutions were flowed over the sensor. The frequency was monitored over time, exploring mouse immunoglobulins and normal human plasma adsorption.
The study showed large amounts of protein adhesion to stainless steel surfaces, while, following a rinse with a non-ionic surfactant, the surface coated with Dursan® showed hardly any protein retention.
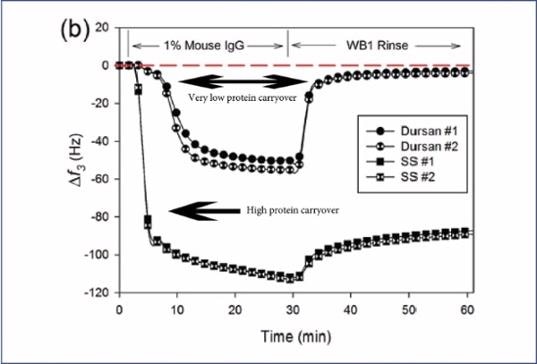
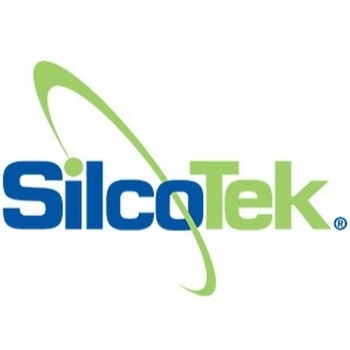
This information has been sourced, reviewed and adapted from materials provided by SilcoTek.
For more information on this source, please visit SilcoTek.