When it comes to plating and surface finishing, businesses are looking to ensure that they don’t have any waste. Although too thick and mechanically fit products may suffer, money is wasted on surplus material. Similarly, too thin products may not be able to meet performance targets, causing businesses to face downtime and costs from correcting errors.
In the worst situations, product failure will tarnish the reputation of businesses. By routinely checking their output, businesses can ensure to reduce their waste and the downtime caused by having to rework or scrap products.
Hence, it is very essential to choose the right equipment to analyze coatings for the business. Several companies analyzing coatings choose XRF as it is fast, simple, and non-destructive. XRF instruments are available in a wide range of forms with features that determine how suitable they are for a specific application. There are two important things that should be considered when choosing the equipment—the type of detector and the size of the sample being measured
The Type of Detector
The selection of the right detector enables shorter measurement times to enhance testing throughput and provides better flexibility to make the analyzer as productive as possible.
PC vs SDD Detectors
In order to measure coatings on small features, XRF coatings instruments employ either a silicon drift detector (SDD) or a proportional counter (PC).
While proportional counters are good for numerous coatings applications, they are ideal when few elements are present in the sample and when thin coatings are being measured on small areas.
Thanks to their superior resolution, SDDs can handle complex coatings structures more easily; they can also be better for very thin coatings (<0.05 µm). Something to consider is the amount of flexibility required in the business. SDDs provide better flexibility for future requirements and can better deal with variations such as adding a new intermediate layer, alloy coatings, or altering the base metal. Cost should also be taken into account – although SDDs cost more up-front, they may be more future proof and save cost in the long run.
.png)
Image Credit: F.M. Callahan
The Samples Measured
The samples that are measured and the way they are measured will decide the type of analyzer that is suitable for a certain application.
Sample size is an apparent thing to consider when selecting the analyzer. Rather than simply assuming whether the samples will fit the analyzer or not, users must consider whether the analyzer they purchase will be future proof or not. Selection coatings analyzers with the right features can enhance productivity for measuring samples today and also adapt to changes in the parts plated by users and the markets served by them. This prolongs the life of the XRF instrument and offers users more opportunities to win new business.
The shape of the sample has a great influence on the type of analyzer purchased. Samples that are long and skinny are better suited to slotted chambers as they can slide through the gap between the door and the stage. With a slotted chamber, one can move the sample along without having to open and close the instrument again and again. However, a closed chamber mitigates the risk of the sample being bumped at the time of measurement, which will provide inaccurate results. Large samples with complicated geometries work well in a closed chamber.
XRF analyzers with larger chamber may have extra features that save time. For instance, larger chambers can be equipped with dual camera views for easier movement around a sample or will have the ability to rapidly adjust the distance from the sample for parts of varying heights. For certain businesses, automatic positioning of samples is very important to the operation as it frees the operator to carry out other tasks while the XRF is taking measurements. For others, manually positioning the sample is adequate.
Regardless of the needs for an XRF analyzer, Hitachi High-Tech Analytical Science has the right analyzer for a specific business. Customers can select from the benchtop FT Series, X-Strata920, MAXXI 6, and handheld X-MET8000 to measure coating thickness.
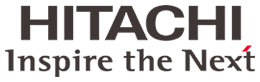
This information has been sourced, reviewed and adapted from materials provided by Hitachi High-Tech Analytical Science.
For more information on this source, please visit Hitachi High-Tech Analytical Science.