A vital part of production processes across many different industries worldwide is accurate and reliable XRF analysis. From ensuring that solder alloys comply with quality control standards to valuing gold jewelry, selecting the right XRF analyzer will have wide-ranging impacts on production processes as well as profitability.
The Hitachi High-Tech X-Strata920 offers a high-tech solution to a wide range of challenges related to coating thickness and materials analysis. The X-Strata920 offers the best accuracy in its class by integrating a micro-focus X-ray tube and a large-area proportional detector.
When it comes to selecting the right instruments for the operations, accuracy is only one part of the equation. There are many other top reasons to choose the X-Strata920 and these include:
.jpg)
Intuitive Software
Any device designed to increase quality standards, and offer a clear business advantage, must be user-friendly. Bogging down resources in complicated user training is not a meaningful outcome for anyone. An expanded version of the SmartLink platform used by the X-Strata920 is intended to simplify routine analysis and enable less trained operators to obtain the same results as expert technical staff. Moreover, advanced users can gain from the combination of powerful analytical features and intuitive operation that give a boost to both their productivity and capabilities.
From3D mapping to bulk analysis and creating statistics and reports, SmartLink simplifies the task of measuring new and old applications.
Flexibility
Due to its simplicity and flexibility, the X-Strata920 can operate in a broad range of analysis situations with minimal user training needed. The vital part of this is the calibration setup.
The X-Strata920 has been optimized for a countless number of applications such as connector coatings, PCB surface, decorative finishes, corrosion resistance, high-temperature resistance, wear resistance, and more.
Fundamental parameters methods give simple and reliable quantitative results when calibration standards are not available. It is possible to create methods in minutes.
Configuration Options
The X-Strata920 is designed in such a way that it accommodates parts of all shapes and sizes, from the extremely small to the long and skinny ones. Also, a mini-well chamber means that the taller parts can be determined in a fast and non-destructive manner
Base Configuration
The standard base features a slotted chamber that enables the measurement of a broad variety of samples, ranging from minute components to large, flat printed circuit boards (even those that go beyond the width of the instrument). Taller samples are taken care by the mini-well base, and automatic measurements are provided by a programmable base. Even when the operation is unattended, users can make sure that they are achieving a high sample throughput by using the programmable base.
This range of options allows users to make sure that target specifications are met, and at the same time costs and time-consuming over-plating and re-work are reduced. The only thing the operator has to worry about is loading and positioning the samples properly. Once the sample is in position, the results are displayed within a fraction of seconds and the operator is free to move on to his next task.
This choice of configurations added to the optimized calibrations created with traceable standards means that users can trust the results produced by the X-Strata920.
Choice of Detectors
The significance of future-proofing equipment cannot be overstated. Having a device that can evolve and adapt with users’ operations will save them plenty of resources in the long run. The X-Strata920 has a choice of two detectors—a proportional counter and a more sophisticated Silicon Drift Detector (SDD).
The proportional counter is ideal for operations that have to reliably and accurately identify single elements. For users who need to detect multiple elements, or those who have the possibility that the coatings they use may possibly change in the future, the SDD enables them to better future-proof their operations. By using lower noise, the SDD is able to detect thinner coating and provide a clearer view of the gold peak.
.jpg)
Language Options
The X-Strata920 can be used without having to be proficient in English, because the software is available in 11 languages. Hitachi’s customers are spread worldwide and they themselves are often part of the global supply chains. As a result, making its solutions user-friendly is an important part of Hitachi’s business.
In-house Expertise
Hitachi’s in-house experts across five applications centers have created more than 1000 coatings applications. In addition to having a team of experienced manufacturers continuously working with customers to improve its products, Hitachi has a global network of service hubs that provide a complete range of technical support.
Whether customers need a fast response to their issue or require a comprehensive online diagnostics, training or preventive maintenance, Hitachi’s team can guarantee that customers’ analyzers continue to generate the right results for years.
Hitachi has been a pioneer in the XRF coatings industry for four decades, and its portfolio includes models such as the CMI series, SFT series, Eco series, X-Strata series, FT series, and MAXXI series. The company’s success has come from knowing that for its clients, reliability and accuracy should go hand in hand with the most recent developments in technology. The X-Strata920 takes this insight, with its series of calibrations and configurations, and uses it to enable manufacturers to quickly and easily ensure the quality of their productions.
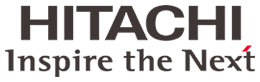
This information has been sourced, reviewed and adapted from materials provided by Hitachi High-Tech Analytical Science.
For more information on this source, please visit Hitachi High-Tech Analytical Science.