Sep 13 2002
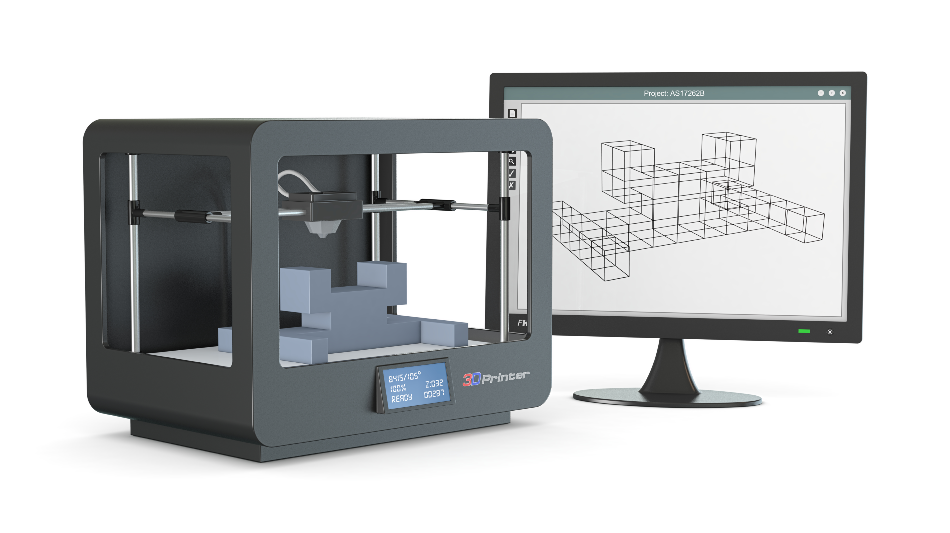
lucado / Shutterstock
Time to market is becoming an increasingly significant factor in the success of a product, apart from cost and quality. A major contributor to product development cycles is the time required to make prototypes.
Additionally, in markets where customers are demanding individually customized components, the time and cost required to produce the molds or tools can be significant.
Rapid Prototyping (RP), also called Solid Freeform Fabrication (SFF) processes helps to resolve these problems. Normally, additive processes are used to build complex shapes, resulting in components without the use of any tools.
Ink Jet Methods
There are two techniques for utilizing inkjet for SFF. The first method is three-dimensional printing (3DP); this is a more advanced technology that uses inkjet to apply a binder to ceramic powder. The other method is Direct Ceramic Jet Printing (DCJP) that deposits ceramic suspensions directly through an inkjet printing nozzle.
Three Dimensional Printing (3DP)
3D printing builds parts in layers. Initially, a layer of loose powder is distributed over the machine bed. Then, the component slice is created by inkjets which form a green part, by selectively injecting a binder into the material. The binder can be a refractory material such as a temporary polymer binder or colloidal silica.
The part is first lowered by a piston, then the next layer of powder is distributed, and the binder is printed once again. The process is repeated until the part is completed. However, when the part is removed from the bed of unbound powder, it has a comparatively low density. This density is usually 50% theoretical, and is either densified by isostatic pressing and sintered, or infiltrated to give a dense part.
A 3D Printer (Z-Corp)
A 3DP can produce parts with intricate geometric features like overhangs, undercuts, and internal voids.
3DP has been utilized to produce a number of items:
- Ceramic cores and molds for metal casting in ZrO2, SiO2, Al2O3, and SiC printed with a refractory colloidal silica binder
- Sintered Si3N4 parts
- Monolithic Al2O3 components with densities of more than 99.3% theoretical, and normal flexural strength of 360 MPa
- Filters for power plants with intricate geometries
- Materials with graded or controlled microstructures; for instance, Zirconia Toughened Alumina (ZTA) can be produced by depositing a ZrO2 slurry onto an Al2O3 bed
Disadvantages of 3DP
The disadvantages of the 3DP method are anisotropic mechanical properties. These are caused by the weak bonding between the layers and poor control of the dimensions of the grown part due to the wetting of the binder, processing parameters, and particle size distribution. Anisotropic properties can be reduced by sintering and isostatic pressing.
Direct Ceramic Jet Printing
Direct Ceramic Jet Printing utilizes the ceramic powder included in ink which passes via a printer nozzle. As the diameter of a typical nozzle is around 60 µm, the diameter of a normal droplet is 100 µm.
Successful DCJP relies on producing an appropriate ceramic ink which is basically a well-dispersed suspension of fine powder. The dispersion should be stable and free from agglomerates.