Laboratory tests possess the potential to offer significant insight into different factors that influence a material's performance. One key benefit is that a laboratory test provides extremely controlled conditions, which allows one to isolate individual features and overlook distracting variables.
Prior to conducting any physical property test:
- Users must understand the reason for performing the test and what they want to do with the data
- Verify if the end point is understood and clear. For subjective end points, it is advised to have an agreed upon rating chart between the concerned parties to reduce interpretation variances of what is acceptable.
- Train laboratory personnel to minimize operator error
- Clarify any ambiguity in the test technique
It is important to know that physical property testing may be impacted by conditions to which the entire system is exposed. For instance, resistance to abrasion is influenced by conditions of the tests such as the nature of abradant; tension of the specimen; the pressure between the specimen and abradant; variable action of the abradant across the area of specimen being abraded; and the dimensional changes in the specimen. For a laboratory test, one should acknowledge the fact that a person may not be able to accurately identify all of the impacts that create conditions that one is attempting to replicate. A majority of standardized test approaches will define the parameters that must be compiled with when conducting tests. If users are not following a proven abrasion test, they must pay attention to the following influences:
- Contact geometry
- Normal force
- Sliding speed
- Length of exposure
- Interacting material surfaces
- Material composition and hardness
- Environmental conditions
Do not become distracted when trying to isolate and replicate the impact of each parameter.
Example
To show the complexity of recreating wear, reflect upon the following example illustrated by Adam Varley of Vartest Laboratories. When a person sits on an upholstered chair, his or her body weight presses down on the fabric. The cushioning materials push up against the upholstery fabric, compressing it, and the user’s body provides a force that drives the fabric he or she is wearing across the surface of the upholstery fabric causing abrasion to take place. Simultaneously, tension or shear forces are placed on the fabric as it pulls against its support.
Visualize the huge variation with body shapes and sizes that should be taken into account. Furthermore, different clothing materials must be considered. A majority of textile technologists agree that wear on textiles includes all interacting factors that may make a fabric to fail; flexing, twisting, snagging, rubbing, stretching, and exposure to sunlight, chemicals, heating, etc. The resistance to abrasion is also affected by factors that are specific to the fibers (fiber content, fiber shape and dimension, fiber mechanical properties, yarn twist, yarn ply, yarn structure, yarn size, and the type, kind, and amount of finishing materials incorporated to the fibers or yarns); fabric construction; thread count; thickness; and weave type.
Helpful Hints
1) Whether or not a specific type of abrasion test relates with end-use performance relies on a similarity of abrading mechanisms as well as on the extent to which that mechanism is maintained during the course of the abrasion test.
2) Abrasion resistance is a combination of the specimen’s basic properties such as hardness, elasticity, strength (tensile, cohesive, and shear strength), toughness and thickness, particularly in the case of wear resistance.
3) The mechanism of wear relies upon the topography of the counterface abradant. It is desirable in most cases to use an abrasive just once, unless it can be refreshed.
4) Different types of wear can take place in combination or on various areas of the same component.
5) Particles responsible for abrasion or erosion are characteristically between 1 µm and 500 µm in size.
6) Materials may not display the same relative order of resistance to abrasion when tested by different techniques.
7) Test approaches that lack crucial procedural information could add problems with reproducibility.
8) When assessing multilayered systems, the substrate plays a significant role. Therefore, care must be taken when assessing the results of tests on various substrate materials.
9) Humidity and loading systems have an impact on test system dynamics.
10) Do not simply accept that the wear rate is always a linear function of time or number of contact cycles—it relies a lot on the materials, type of wear, and the contact conditions.
11) Ensure steady-state conditions are realized. Some materials may need a run-in period.
12) Extrapolate results only with considerable caution.
13) Do not use loads that surpass the maximum strength of a material or speeds that can cause a thermal condition on the test specimen.
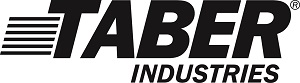
This information has been sourced, reviewed and adapted from materials provided by Taber Industries.
For more information on this source, please visit Taber Industries.