Located 20 miles from Charleston, South Carolina is the Isle of Palms which is a small barrier island. There is a small oceanfront lodge called Seaside Inn on the island, with excellent access to the beach.
.jpg)
Challenges
Located on the first floor is the lodge’s main lobby area, which is 12 ft. above ground level. The access stairs to the lobby were metal and concrete for years, which constantly rusted. The management company stated that it spent more than $2,500 a year to get the stairs sandblasted, rust treated and repainted. Rust started to reappear within 60 days of treatment.
The complete annual process would create no significant improvement to aesthetics and cause inaccessibility for nearly two weeks. The front staircase measured 54" wide and shared the same corrosion cycle as the 8' wide access stairs to the service elevators adjacent to the front of the facility, which further complicated accessibility. In the end, the stairs deteriorated beyond repair.
The costs associated with the ongoing corrosion repairs were concerning to the lodge’s HOA board and they started looking into ownership costs across a 15 year period. They found that a huge part of the $20,000 maintenance expenses ($7,500 for three years of sand blasting treatment/repaint and $12,100 for 11 years of painting) had been used on the stairs.
Under the advice of several general contractors and a structural engineer the board was given three practical choices for replacement. A summary of those three options is below.
.jpg)
.jpg)
Solution
The HOA realized that maintaining aesthetics was crucial to the facility after reviewing option three. EXTREN® ’s potential to give 75 years or more of life expectancy was a surprise. This option also provided the cheapest 10 year overall ownership costs in comparison to cast-in-place concrete (57% less) and steel (32% less).
Furthermore, the inn is positioned next to a busy two-lane street which is the only access point for tourists and deliveries. Option 3 also gave a significant downtime reduction compared to cast-in-place concrete (98%) and steel (88%) all without the need for traffic rerouting or special permits, as the stairs remain one of two access points for check-ins. Engineers and guests still have to be convinced that the steps are pultruded fiberglass after 11 years of continuous use. The HOA voted to replace the property’s 8' wide elevator access stairs with EXTREN® as well, based on the success of this project.
Technical Data
Product |
Oceanfront Lodge Entry Stair System |
Process |
Pultrusion |
Materials & Sizes |
EXTREN® Series 525 Structural Shapes |
For |
SRH Corporation |
User |
Seaside Inn |
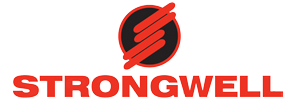
This information has been sourced, reviewed and adapted from materials provided by Strongwell Corporation.
For more information on this source, please visit Strongwell Corporation.