
Ensuper / Shutterstock
Lubricants are used throughout various mechanical systems, from engines and motors to industrial machinery. They have many beneficial properties that prevent wear and damage to mechanical components in a system, often by lubricating the surfaces between moving metal components (and lowering the friction). However, no lubricant is the same, and this can be because of the type of lubricant or in the additives that a specific lubricant contains - and many are designed to work in particular environments/applications. In this article, we look at the types of lubricant available and what factors go into choosing whether a lubricant is suitable for your intended application.
The Types of Lubricant to Choose From
There are two classes of lubricants that people usually choose from depending on the intended application, lubrication environment, and other determining factors. These two classes of lubricants are general purpose and synthetic.
Regardless of the type of lubricant used, there are requirements that all lubricants must meet as standard. These include reducing the friction and wear of the system they are used in, protecting the surrounding environment from corrosion, dissipating heat and the ability to provide a sealant effect. While these are the fundamental properties that each lubricant must have, they can also possess a wide range of other beneficial features, which vary depending on the lubricant formulation and the intended application for each lubricant.
General purpose lubricants are usually those which are hydrocarbon based and are often mineral oil distillates of crude oil. They are typically composed of 95% base mineral oil, while the other 5% is made up of various additives. These types of lubricants are often used in engine and motor-based applications.
Synthetic lubricants, on the other hand, are synthetically derived specialty lubricants, with the most common compositions being made up of polyalphaolefins (PAOs) or synthetic esters. Synthetic lubricants generally offer much better properties than general purpose oils and are typically used to provide better mechanical and chemical properties to the system; however, their cost is much higher (often between 50 and 500% more expensive). So, general purpose oils are generally used when an enhanced lubricant is not required for the task, as the difference in lubricant quality may not be worth the extra cost.
There is also a third type of lubricant known as semi-synthetic oils. These are a blend of mineral and synthetic lubricants, where the properties are usually enhanced against general purpose lubricants but are much cheaper than fully synthetic lubricants.
What Factors Should Be Considered?
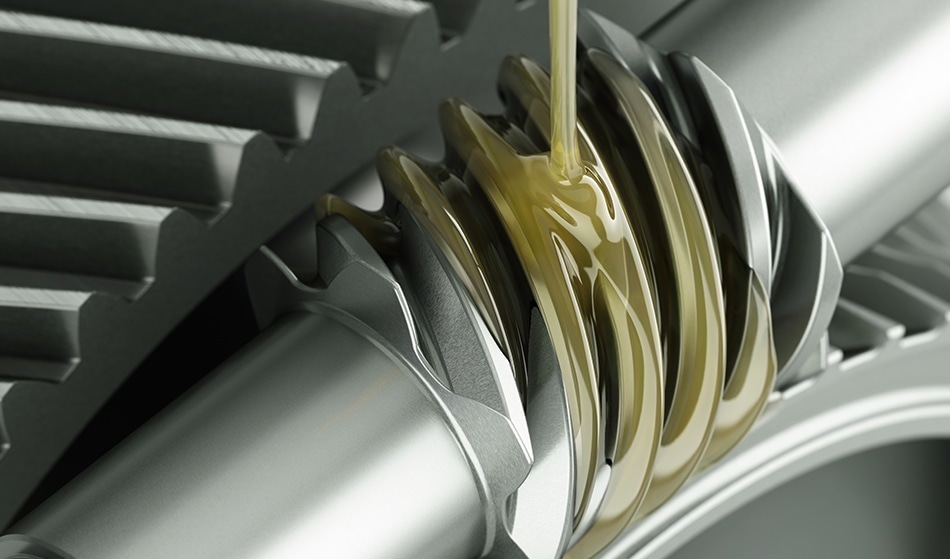
maxuser / Shutterstock
The first significant factor to consider is whether the equipment using the lubricant will need to be maintained at regular intervals, or whether the apparatus can be lubricated “for life.” If the lubricant is maintained regularly, then the better option is to use a lower-quality general purpose lubricant that can meet the necessary performance requirements and replace it when it becomes contaminated or degraded. Many of the specialty synthetic lubricants have been designed to last for extended periods of time without maintenance.
Once the general type of lubricant is known, many other factors can affect the choice made. The other key factor to consider is the base oil viscosity, which is determined by a series of sub-factors that are relevant to the type of lubricant specific to your needs. These sub-factors include: axis operating speed (and whether it is fixed or variable), whether the friction forces are sliding or rolling, temperature, load and environmental conditions, required viscosity, amount of moisture in the system (water can damage lubricants), and whether the lubricant needs to adhere to any industry-specific standards.
Once all these are known by the manufacturer (or vendor), then they should be able to point you in the right direction as to which lubricant is best suited for your application. In cases where there is not a suitable lubricant available to meet your specific needs, you will have to purchase a customized/tailored lubricant based on your requirements. Luckily, many manufacturers offer this service.
Overall, If you are looking for a lubricant with:
- Both low and high temperature viscosity performance
- Low evaporative loss
- Lesser degrees of friction and wear
- Higher efficiencies,
- Higher chemical stability
- Greater viscosity index
- Extended drain intervals,
- Longer-life expectancy
Then the best option is one of the many synthetic lubricants available (with the specific type being based around the desired individual properties), especially if cost is not an issue.
If you’re looking more towards the lower-end and lower performance side of lubricants, then a standard general-purpose lubricant will be sufficient. However, if cost is a factor (but it should never be the only factor), you will need to work out the cost of buying more significant amounts of cheaper general-purpose lubricant (depending how often maintenance will be required– which will depend on how intensive the lubrication environment is), against the more substantial upfront cost of a synthetic lubricant.
Sources:
Disclaimer: The views expressed here are those of the author expressed in their private capacity and do not necessarily represent the views of AZoM.com Limited T/A AZoNetwork the owner and operator of this website. This disclaimer forms part of the Terms and conditions of use of this website.