International Syalons have investigated the mechanical properties of silicon nitride (Si3N4) in depth. An advanced engineering ceramic, silicon nitride circumvents several of the conventional disadvantages of many oxide ceramics.
Exceptional fracture toughness and high moduli of rupture and elasticity impart outstanding resistance to multiple wearing phenomena. This presents the ability of silicon nitride-based ceramics to cope with severe operating conditions that have been known to cause comparatively brittle ceramics to propagate flaws, deform, or even fail.
These properties govern the mechanical integrity of material when responding to loading or bending forces, and are mainly functions of either strength or toughness. In addition, hardness is a key factor in the mechanical behavior of technical ceramics.
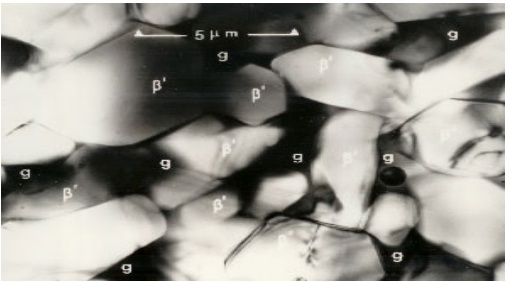
Image Credit: International Syalons
What is Hardness of a Material?
The hardness of a material refers to the measure of how well its crystalline structure continues to hold together in response to forces of friction or impact. Typically, hardness displays the strength of the intermolecular atomic structure of the material in a linear relationship. Nevertheless, it is a property that comes with its complexities, which are dependent on many factors such as toughness, strength, and ductility.
Three specific measurement types are attributed to finding out the hardness of materials when they are exposed to specific forms of stress. Indentation hardness is the most prevalent form of testing utilized in engineering sectors. This is, in reference, the ability of a material to resist deformation by an indenter such as a sharp point. Different testing methodologies can be used to further break down indentation hardness into multiple scales.
Hardness characteristics related to silicon nitride are usually tested using the Vickers or Rockwell scales, also referred to as the microhardness method. It involves a diamond pyramid indenter being pushed into the surface area of the test material at a specific load force. Then, the amount of indentation is measured and converted into a unit of hardness. This is expressed as the load over the indentation’s surface area (Kg/mm2 or GPa).
Why is Hardness Important?
Extreme hardness values allow ceramics to tolerate significant wearing phenomena. This ranges from mechanical agitation to small-particle abrasion. This allows silicon nitride-based ceramics to be engineered into complex, long-lasting shapes. It enables rugged applications in some of the most challenging industrial sectors. Parts routinely produced using silicon nitride-based ceramics are nozzles, milling media, plates, welding jigs, and fixtures.
Under the Syalon product family, International Syalons offers a wide-ranging selection of silicon nitride and sialon. These display specific hardness characteristics appropriate for a variety of applications.
- Syalon 050 displays a hardness value of 19.81 GPa.
- Syalon 101 displays a hardness value of 14.71 GPa
- Syalon 110 displays a hardness value of 11.77 GPa
- Syalon 501 displays a hardness value of 13.24 GPa
Silicon Nitride Ceramics from International Syalons
International Syalons specializes in producing high-performance ceramics with specifically tailored thermomechanical properties that are appropriate for demanding applications. The range of Syalon products cover the three crystalline phases of silicon nitride and is offered with hardness properties comparable with that of high purity alumina.
Sialons are modern technical ceramics based on silicon nitride (Si3N4) and offer equal or improved mechanical properties compared to silicon nitride thanks to their isostructural composition and high strength covalently bonded semi-crystalline microstructure.
This exceptional atomic scale density allows excellent resistance to extreme mechanical degradation and corrosion, which are very usual in industrial manufacturing environments. Hence, Sialons are continuously employed for the fabrication of wear components and thermally stable barriers for heat-sensitive elements. Commonly, the materials of the sialon group are used for producing grinding media, cutting tools, and thermocouple protection sheaths.
Syalon 050 is distinct from other sialons due to its enhanced hardness and high temperature properties. Although all sialons exhibit excellent mechanical stability when common industrial corrosive elements such as alkalis and acids are present, Syalon 050 was particularly intended to withstand the most difficult wear conditions. It is stable in the presence of molten aluminium for prolonged periods of exposure and is completely non-reactive to most industrial acids and alkalis at boiling temperatures.
In this article, the capacities and applications of Syalon 050 are explored in more detail.
Specialized Corrosion-Resistant Sialons
Syalon 050 is an α/β-sialon composite. Its fully dense microstructure contains both interlocking needle-like β-SiAlON grains and a fine equiaxed α-SiAlON grains. The material’s hardness rating of 94 HRA comes from this structural matrix, forming a 0% porosity bulk material with a very low glassy-phase content that is intrinsically resistant to a range of industrial corrosives and refractory temperatures. It has the ability to maintain this mechanical stability at continuous operating temperatures up to 1450 °C (2552 °F), demonstrating total non-reactivity with molten non-ferrous metals including aluminium, tin, and zinc for metallurgical applications.
Sialons for Chemical Processing
Sialons are continuously used for enhancing transport processes and chemical handling in industrial chemical manufacturing and production facilities. Tubes produced from Syalon 050 do not react with common acids and alkalis such as hydrofluoric acid, potassium chloride, and acetic acid. These have been examined at 100% concentration and boiling temperatures for nearly 100 hours of continuous exposure.
Sialons for Metering Valves
A metering valve is an important component in the oil and gas sector and is used for controlling the flow rates of corrosive materials over transport components. Syalon 101 is the preferred sialon ceramic for fabricating exceptionally tough metering valves for marine and chemical applications, offering reliability and security, and surpassing traditional metering valve materials by factors of up to 14 to 1.
Sialons for Shot-Blast Nozzles
Shot-blast nozzles are the outlet component for industrial sand or grit blasting surface preparation. They have the ability to withstand extremely abrasive media and velocities throughout their service application in automotive manufacturing, construction, and wear industries. These sectors employ different abrasive methodologies, from wet abrasive blasting to hydro-blasting. Sandblasting is the most conventional technique, which involves projecting a continuous, pressurized stream of abrasive grit over a surface to modify its composition.
The challenging specifications of hot-blasting equipment need high-performance materials with the ability to resist sustained temperatures and pressures. It is common to use traditional metals with excellent hardness values for preparing tough shot-blast nozzle linings; however, they lack the ability to compete with the distinctive mechanical stability of advanced silicon nitride ceramics.
Syalon 050 was customized for wear applications, where components are required to continually withstand various abrasive and corrosive elements. Shot-blast nozzles are subject to normal abrasion from heavily pressurized and high-temperature media. Silicon nitride shot-blast nozzles were intended to surpass standard industry materials like tungsten carbide (WC) and alumina (Al2O3), by offering advanced temperature resistances of up to 1450 °C (2642 °F) at pressures of up to 100 psi for tough continuous operating hours.
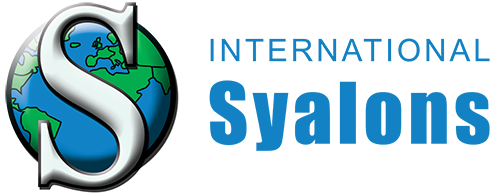
This information has been sourced, reviewed and adapted from materials provided by International Syalons.
For more information on this source, please visit International Syalons.