.jpg)
SilcoTek® provides a wide range of coatings including SilcoNert®, Dursan®, Silcolly® and Notak™. To stop things from becoming too confusing, this article is going to look at the different uses of each coating.
.jpg)
Coatings can be considered as tools which are used to enhance the ability of processes and products. They can be thought of in a similar manner to doing up the bathroom – a lot of different jobs need to be done and you have the knowledge and materials required, but you also need the tools.
Just a screwdriver isn’t enough – you’ll also need a drill, a hammer, a trowel and more. Each tool is designed to help achieve a specific task. The same is true for coatings.
This article would explore:
- The different applications for the different coatings provided by SilcoTek
- The materials present in each of these coatings
- How to assess the suitability of a coating to give the required performance for a specific application
Choosing the right coating can be difficult as each one has its own specific characteristics and there are so many different potential applications.
As experts in coatings, SilcoTek has produced a simple-to-use guide to help with appropriate coating selection. As the guide is not fully comprehensive and there are so many different factors to consider, it is still recommended to speak to an expert at SilcoTek after using the guide. For some circumstances a custom coating from SilcoTek may give optimum performance.
Comparing Coating Performance
The performance guide in the table below rates coating performance for different environments and applications.
For example, the table shows that if a coating resistant to acids and bases is required, then Dursan® is most appropriate, whereas if an inert coating for use at temperatures below 200 oC is needed then SilcoNert® 2000 is the most appropriate. However, if the customer is looking for an ‘all-rounder’, then Sawzall® is a good choice.
.jpg)
Best Practice for Using the Guide
When using the guide the following questions should be asked, related to what is required for your specific application:
- What is the maximum temperature the coating will be exposed to?
- What is the pH range of the application?
- What coating surface properties are needed?
These questions should be answered and the values given for each property should be added together to find the most appropriate coating. for example:
- The application involves acids so the coating must be acid resistant up to pH 14
- The following surface properties are needed:
- Acid corrosion resistance
- Inertness
- Hydrophobicity
Taking this information and applying it to the table gives the following ratings:
Using this information, each coating would receive the following scores.
SilcoNert 1000: (Chemical Inertness, 2) (Hydrophobicity, 2) (Acid Corrosion Resistance, 2) = 6
SilcoNert 2000: (Chemical Inertness, 4) (Hydrophobicity, 3) (Acid Corrosion Resistance, 2) = 9
SilcoGuard: (Chemical Inertness, 2) (Hydrophobicity, 2) (Acid Corrosion Resistance, 3) = 7
SilcoKlean: (Chemical Inertness, 2) (Hydrophobicity, 3) (Acid Corrosion Resistance, 2) = 7
Silcolloy: (Chemical Inertness, 2) (Hydrophobicity, 2) (Acid Corrosion Resistance, 4) = 8
Dursan: (Chemical Inertness, 3) (Hydrophobicity, 3) (Acid Corrosion Resistance, 4) = 10
Dursox: Chemical Inertness, 2) (Hydrophobicity, 1) (Acid Corrosion Resistance, 4) = 7
Following this method, Dursan® is the most appropriate coating with SilcoNert® 2000 in second place. As the application requires high corrosion resistance over a wide pH range, Dursan is the best coating.
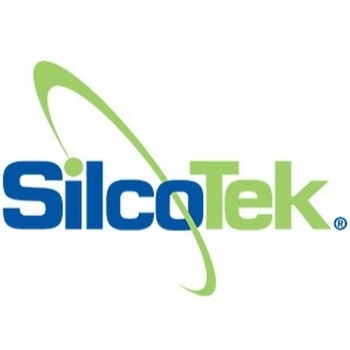
This information has been sourced, reviewed and adapted from materials provided by SilcoTek.
For more information on this source, please visit SilcoTek.