.jpeg)
Almost 50% of all sample transfer systems in industry are either failing, or they have already failed – this is not good news for process control. This article explores how to keep sample transfer systems in operation, the money that can be saved by looking after your systems, and how to avoid regulatory fines associated with failure.
Most process control systems directly interact with the fluids or samples being processed. This means it is very important that these systems are durable, have low reactivity towards the materials they are handling and that they are responsive to external systems.
This article will explore:
- Ways to make process sampling and control systems more reliable and durable
- Improving the responsiveness of process monitoring systems
- Using CVD to coat existing designs with inert and durable coatings
- The important things to consider when selecting materials of process sampling and control systems
- The unique challenges for instrument probes and other forms of samplers
Systems used for process monitoring undergo a lot of environmental stresses. These can include phase changes within the system (vapor condensing, or liquids freezing), extreme temperatures, corrosion and chemical reactions with the surface, tube fouling, liquid pooling and moisture contaminations and more.
It is because of all of these challenges that so many process systems are in a critical state and need to be repaired or replaced.
Efficient process control with a reduced chance of failure can be achieved by building a system with a hardy design that is regularly maintained. Additionally, the materials used should be chosen to improve the efficiency and compliance of the system. Sample transfers and heating problems should be discussed with heat specialists to ensure that heating is not problematic.
When selecting the most appropriate materials the plant’s engineers should be consulted as they have the most knowledge about the process conditions. Once the key problems to solve are known, the requirements of the material can be determined.
Selecting the Correct Material
Whenever a sample is transported from one point to another it must come into contact with another material – this could be the internal surface of a sample container in the lab, or the inside of tubing or a pipe in a factory. The behavior of this material that the sample is in contact with is very important.
The most common choices for piping and container materials are stainless steel and PTFE. However, they might not always be the most appropriate. Before selecting a material the chemical behavior of the sample, the environment it will be in and the economics of the plant must be considered.
An example of where the environment must be considered is a chemical plant which uses monitoring probes to test corrosive solutions. The table below shows the huge variation in how common CVD coatings on steel perform when exposed to corrosive materials. This variation is highly important as it can have a significant impact on the performance and economics of a process.
.jpg)
Considering the Process Environment
Processing conditions vary depending on what is being processed, with many presenting their own challenges. This can include high temperatures, corrosive exposure, abrasive feeds or rapidly oscillating temperatures.
Other processing systems must keep the temperature constant. If this temperature is close to the melting temperature of PTFE, which is 250 °C, the system can deform and tubing can collapse (this has even been known to occur at constant temperatures of 120 °C).
Using extremely inert, temperature resistant coatings such as Dursan® and SilcoNert® is beneficial as they can handle temperatures reaching 450 °C whereas coatings containing silicon such as Silcolloy® can withstand more extreme temperatures greater than 1000 °C.
.jpg)
Considering Corrosion Resistance
Many samples contain strong acids, such as hydrochloric or sulfuric acid and even low exposure, when occurring over a long time span, can pit into sample containers and tubing. Pitting is problematic as it provides somewhere for analyte and moisture to collect, which can result in sample degradation and unwanted chemistry from occurring.
Using an inert coating can bring corrosion resistivity to materials such as stainless steel, providing inertness at a low cost. When comparing the performance of stainless steel (and alloys) with stainless steel coated with SilcoTek® in 6M HCl, the Dursan-coated surface saw less corrosion by a factor of 10.
.jpg)
Considering Abrasion and Wear Resistance
Highly abrasive materials can damage tubing made of (relatively) soft materials such as PTFE. Filtering the sample before processing can reduce the effects of this but damage is still possible from abrasion or by handlers interacting with the system.
Studies, using a pin-on-disk method, which compared uncoated steel with Dursan coated steel showed that Dursan coating reduces wear by 50% and friction is also reduced, meaning Dursan significantly improves durability.
It is possible to apply Dursan (and all other CVD coatings) to both internal and external coatings. The process is used in non line-of-sight so even systems with complex internal structures, such as fritted filters, can be coated effectively.
.jpg)
Abrasion Resistance Demonstration - Dursan® from SilcoTek®
The Importance of Sample Properties and Behavior
Whilst obvious, knowledge about the sample being processed is key to making sure the processing equipment is up to scratch. The following information is important:
- The moisture content of the sample
- If the sample contains corrosive chemicals or components
- Potential reactions of the sample with all materials in the processing system, i.e. sealants, piping, probes etc.
- The pressure and temperature of the sample
- The phase of the sample and if this remains constant throughout the process
- The concentration (or concentration range) of the sample:
- Surface reactivity has a bigger impact (relatively) on a 200 ppb H2S sample than a 20% concentrated sample as a loss of 10 ppb throughout the samples path is a 50% loss of total sample
- Whereas for a 20% concentrated H2S solution the flow path must be more resistant to corrosion than a 20 ppb concentration
.jpg)
Getting the Best Results
The needs and functions of a particular sample analysis system determines which materials should be selected to give the best performance. For example, does the system need to calibrated for low level detection, is the sample (e.g. sulfur) speciate during the process, or is quick grabbing required for a maximum allowable value.
For example, a system designed to sample 20% concentrated H2S will not be able to accurately sample H2S at 20 ppb concentration. Many materials, including stainless steel and other alloys, elastomers, glasses and ceramics, will adsorb reactive samples; meaning trace samples in untreated containers can be completely lost as a result of adsorption.
.jpg)
Improving the Response of a System
The adsorption of sample as a result of surface interaction can be problematic – it introduces inaccurate results and means the entire system can spiral out of control, as reactive surfaces and adsorption slow the samples journey to an analyzer.
For example, using the case of H2S, as the sample travels through the system it is absorbed by the surrounding material to the effect for no H2S (initially) makes it to the detector.
It is only once all of the surrounding material has been saturated that it can flow through the entire system and be detected at the end. Depending on the length of the system and the concentration of H2S this can take anywhere between minutes to hours.
Using a coated line, which prevents sample adsorption, prevents this from occurring and the sample can travel undeterred through the entire system proving a journey time of seconds or minutes rather than hours. This is an important thing to achieve when processes must have good yields and comply with process control regulations.
.jpg)
This case study does not only relate to H2S as almost all processing of reactive samples is improved by coating the sample with SilcoNert or Dursan. Using a SilcoNert coated system results in a response in seconds, whereas PTFE or stainless steel lines require longer.
Response delays can have big consequences such as false alarms, the damage of systems which use catalysts for processing or incorrect measurements by auto feed systems.
.jpg)
Cost
As (unfortunately) budget constraints exist, cost needs to be taken into consideration. The total cost should always be considered, i.e. not just the cost of setting up the system but also the total cost of operating the system over its lifetime.
Even the quickest of calculations will demonstrate that having to regularly repair a system invalidates any short-term savings when setting a system up. For this reason it makes sense to always use a coated system, rather than naked stainless steel or PTFE where possible.
.jpg)
Choosing the Right Material
If you’re unsure on which material you should choose for your analytical flow path please see the below table. This comparison chart visualizes the different limitations and advantages of different materials for use in process control and sample transfer.
Material |
Advantages |
Limitations |
Stainless Steel |
Low cost, durable, high/low temperature capable |
Reactive, lower corrosion resistance |
PTFE |
Corrosion resistant, inert, low cost |
Permeable, easily damaged, low melting point |
Super Alloys |
Corrosion resistant |
Expensive, limited availability, reactive surface |
Inert Coating, Dursan, SilcoNert |
Corrosion resistant, inert, durable, temperature capable |
Can be damaged by base exposure. Abrasives can damage over time. |
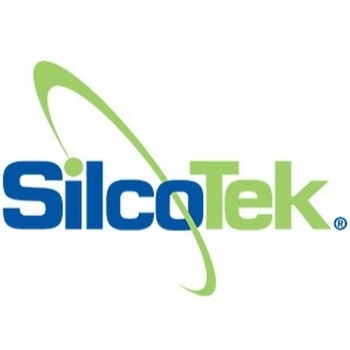
This information has been sourced, reviewed and adapted from materials provided by SilcoTek.
For more information on this source, please visit SilcoTek.