.jpg)
SilcoTek® provides a wide range of inert coatings which go beyond their primary use in process sampling. This article will explore the different uses for coatings from SilcoTek.
This article will cover:
- The different applications that silicon-based CVD coatings can be used in
- The advantages of using CVD coatings in industry
- The materials which can be used with CVD coatings
One of the main applications for SlicoTek’s coatings, which are designed to be extremely inert, is the transportation of analytical samples. SilcoTek coatings can be found in many different analytical systems and components for sample transport and sample testing. Examples of these applications include:
- Gas Chromatography (GC)
- The monitoring of flares and stacks
- The monitoring of whole air
- Analytical processing
- Transporting samples
- EPA 325 Fenceline monitoring
Provided that the material used is compatible, the entire flow path of a system can be coated. This means it is possible to coat fittings, valves, probes, fritted filters, tubing, sample containers and glass liners to improve the inertness of the system path.
.jpg)
What are the Benefits?
Coatings from SilcoTek have many advantages. Research into their effectiveness has shown that the coatings prevent cross-contamination, improve sensitivity and improve responses – meaning systems can rapidly provide accurate data.
Testing conducted outside of SilcoTek has demonstrated that flow paths coated with SilcoNert® provide the lowest adsorption rate when compared to other available coatings. This means a faster response time and less cross contamination.
.jpg)
Coating to Improve Corrosion Resistance
Whilst inert coatings for sample transportation is a large application area for SilcoTek coatings, the largest application is the provision of corrosion resistance, which is in high demand. Applications in which corrosion resistance is required include:
- Upstream and downstream oil and gas transport
- Processing systems in chemical plants
- Furnaces and other fabrication units for semiconductor manufacturing
- Medical diagnostic equipment
- Offshore and marine systems
.jpg)
Corrosion resistant coatings are mostly applied to fittings and tubings; however, coating of valves, regulators, canisters and the interior and exterior surfaces of needles are also coated.
The Advantages of SilcoTek Coatings for Corrosion Resistance
Products coated to be corrosion resistant don’t cause process contamination due to rust and have a longer lifetime.
.png)
Avoiding process contamination is especially important in research, chemical processing and semiconductor manufacturing. For example, the image below shows uncoated stainless steel exposed to 6M hydrochloric acid for 72 hours – the liquid is green because the metal is leaching into the acid, making it turn green, as the steel corrodes.
Below the same test has been run but with a Dursan coated sample. It can be seen that the sample looks brand new and the solution remains clear, indicating that no corrosion or liquid contamination has occurred.
.jpg)
.png)
The corrosion rates of different coatings, including Dursan, and naked stainless steel are shown below.
.jpg)
Other Common Coating Applications
Other common uses for SilcoTek coatings include:
- Preventing protein carry over in medicine
- Modifying the surface energy of filters and sensors
- Corrosion resistance, low contamination and inertness in HPLC needles and flow paths
- Non-stick and anti-fouling surfaces for chemical processing, refining, aerospace and automotive
- Non-stick for mold release in plastic manufacturing
.jpg)
Coatings from SilcoTek can also be used to modify the energy of a surface to make it hydrophilic (wetting), hydrophobic (non-wetting) or oleophobic (oil repelling). This is very useful for specific filtration, sensing and probes.
What can be Coated?
Coatings from SilcoTek can be used to coat a variety of different components, from intricate shapes to objects with a high surface area. As the novel CVD process used is non-line of sight it possible to coat internal surfaces too. Examples of things that can be coated include:
- Probes and sensors
- Tubing, valves and fittings
- Filters – metal or ceramic
- Reactors and heat exchangers
- HPLC and GC systems
- Needles and fuel injectors
- Precision components
- Intricate components
- Sample containers and gas containers
- Regulators
What Materials can be Coated?
Coatings from SilcoTek can be applied to a wide variety of materials allowing their surface properties to be modified.
Some of the more unusual materials we can coat include:
Aluminum
Not all aluminum systems can be coated. For example, components, which undergo high stress, such as sample cylinders, should not be coated and there are some grades that should be avoided too. More information can be found on the SilcoTek website.
Glass
Coatings can be made to make glass even more inert than it already is. Whilst glass does not break down too easily it can contain contaminants, which can interfere with chemical and analytical processes, impacting research quality.
Alloys
SilcoTek coatings can be used on most alloys. For alloys which are expensive to produce, such as Hastelloy®, the alloy lifetime can be significantly increased by improving the durability, corrosion resistance and chemical inertness, saving money in the long term.
.jpg)
Ceramics and Quartz
SilcoTek coatings can be used to further increase the inertness of quartz and ceramics for high temperature applications. The coatings also adhere to the porous surface of ceramics regardless of how high the surface area is.
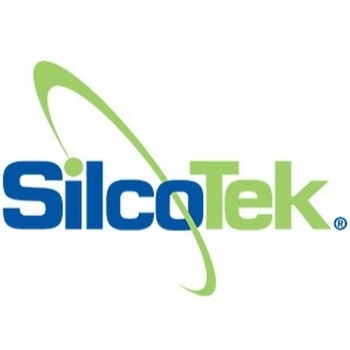
This information has been sourced, reviewed and adapted from materials provided by SilcoTek.
For more information on this source, please visit SilcoTek.