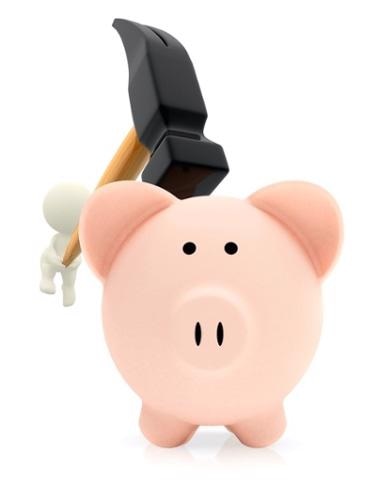
SilcoTek® provides a range of wear and impact resistant coatings. To demonstrate the benefits that this coating technology can provide, the SilcoTek R&D team recently conducted testing to evaluate the strength and bend resistance of their CVD based coating Dursan®.
The tensile strengths of an uncoated and Dursan coated 316 stainless steel rod (of 1” diameter) were tested. The samples were pulled until they reached a point of failure (at their ultimate strength). The below video shows an example of the type of test ran:
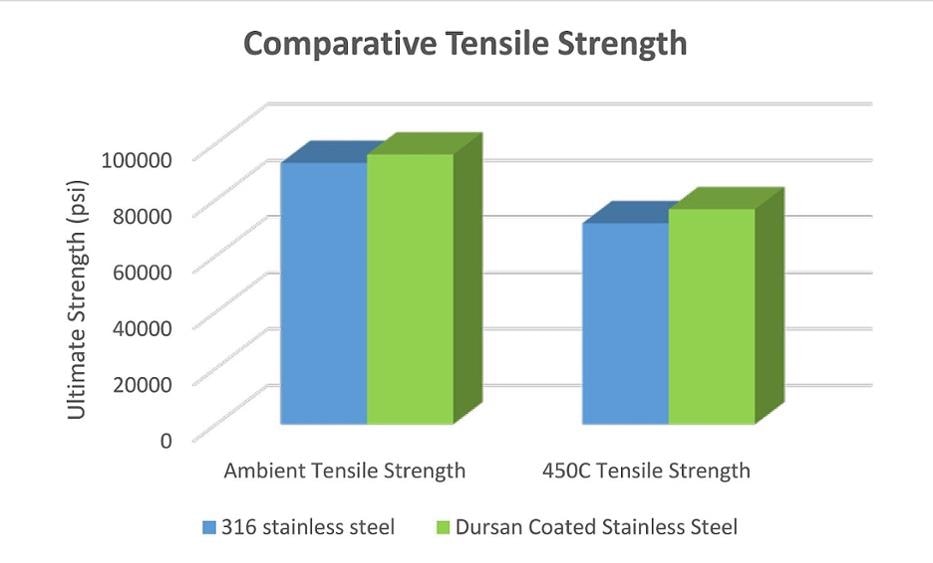
The results demonstrated that the Dursan coated rod outperformed the uncoated rod in terms of ultimate performance, with a failure at 96,000 psi at room temperature.
The test was repeated at 450 oC which showed a reduction in the ultimate tensile strength of both the coated and uncoated rod. For both rods the ultimate strength is reduced, though the coated rod has a lower reduction (by 20%) than the uncoated rod (23%).
Comparative tensile strength |
|
|
Material |
Ambient Tensile Strength |
450C Tensile Strength |
316 stainless steel |
93000 |
71500 |
Dursan® Coated Stainless Steel |
96000 |
76500 |
Testing Impact Resistance and Crushing
Crushing tests on coated samples (foil and a steel ball) were carried out to see if the coating remained adhered to the surface.
Firstly a coated foil of stainless steel and a painted foil sheet were crushed. Following crushing, the coating had remained surface bound and not flaked.
Bend it, Smash it, Ball it up - SilcoTek® Coatings Won't Flake like Paint
A press was then used to crush a coated steel ball to see if this would remove the coating, which following crushing remained intact. A coated tube then underwent a bending test, which also demonstrated that the coating remains intact following the application of force.
The Flexibility of SilcoTek® Coating Solutions
Wear Resistance
Testing surfaces coated with Dursan showed that they had greater lubricity and more wear resistance than stainless steel. This makes Dursan an ideal coating for valve components and other surfaces prone to wear.
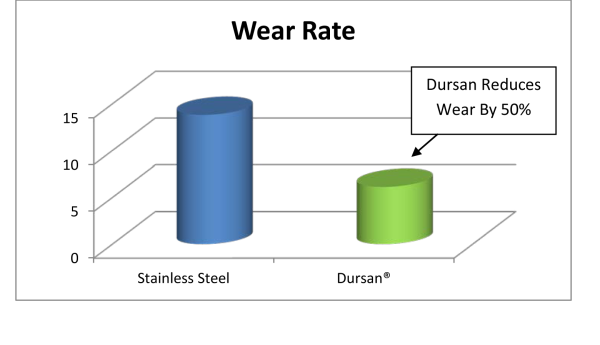
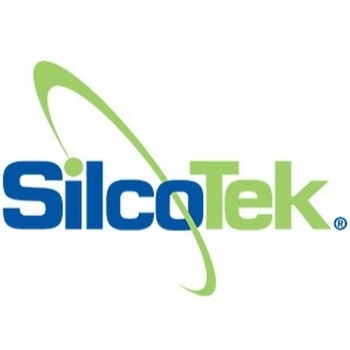
This information has been sourced, reviewed and adapted from materials provided by SilcoTek.
For more information on this source, please visit SilcoTek.