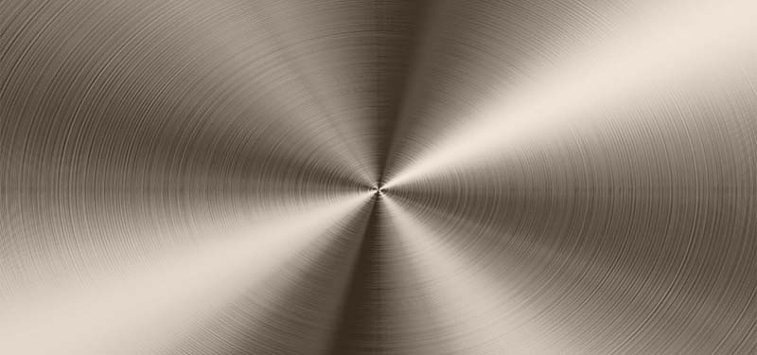
The number of electrons in the element's outer shell hugely influences reactivity. If the outer electron shell is full then an additional chemical bond cannot be formed because there is no room.
Inert elements, such as silver, gold, or platinum are less reactive because they have a full shell. These elements would make excellent materials for inert surfaces used in processes, but they are also expensive.
Cost forces us to switch to less optimal but generally stable materials, with few available open electron spaces in their outer shell. Thankfully there are a number of methods and processes available to make a less reactive surface.
Other factors to consider such as cost, toxicity, work-ability, durability, and overall fitness for use that play a major part in the inert surface selection evaluation and process of an inert surface.
Options to Make the Surface Inert
Siloxanes
Types of siloxanes, such as PDMS (polydimethylsiloxane), can be employed to coat surfaces to essentially cover up any reactive sites on a surface. This technique is popular and inexpensive, but there are durability issues and temperature limitations.
Passivation
Passivation is a term which applies to processes that eliminate select reactive elements from the surface. Acid passivation techniques are used on materials like stainless steel, to remove iron from the surface and enrich the chromium, nickel content which enhances reactivity and corrosion resistance.
Passivation can improve corrosion resistance somewhat but does not show much improvement in other reactivity issues like chemical adsorption.
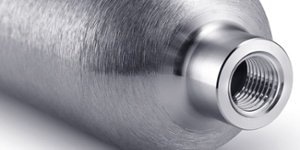
Some other passivation methods include saturation methods such as priming which is employed when analyzing and handling "percent level" applications. The technique of priming is to flow lots of an analyte through a flow path and letting the analyte be absorbed onto the surface.
Hopefully all active sites will be taken up by the analyte. This method is largely ineffective when sampling lower levels or part-per-million of a sample and there can be extreme desorption issues. Corrosion resistance is typically not enhanced using this technique and test results are unreliable.
Coatings
Coatings of all types have been utilized with different degrees of success. Whilst they are effective in corrosion resistant applications, they are ineffective in precision inert sampling applications.
About Silicon and Silicon Coatings
Silicon is a relatively non-reactive element but can react at high temperature (molten state). Silicon acts like a non-metal and metal which means it can be utilized in electronics and exceptionally precise applications such as semiconductors.
Silicon is not easily compromised because it does not readily oxidize or react with acids (but can be etched and damaged by some acids like hydrofluoric acid and can be damaged by bases). Silicon based coatings are becoming increasingly popular as a solution to surface reactivity problems.
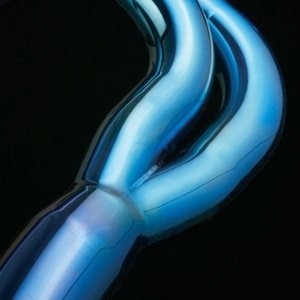
Why Use Silicon?
Silicon is relatively durable, plentiful and inexpensive. Elemental silicon cannot be readily found in nature but the oxide versions like SiO (sand) are found in abundance. The main reason silicon is a good prospect for an inert, non-reactive surface is its capability to be "doped" with other non-reactive agents, such as carbon, that can make a highly inert and durable material, when combined with silicon.
The data
Silicon surfaces allow part per billion and part per trillion analysis. Carbon enhanced silicon surfaces have been tested routinely to single digit part-per-million stability for reactive materials like sulfur or mercury in gas chromatography. Whilst silicon can produce exceptional sensitivity in moisture analysis down to part-per-trillion sensitivity.
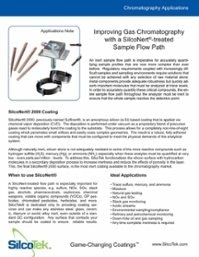
The inertness and non-reactivity of a silicon surface (in this case SilcoNert® 2000) is shown by extreme, low level mercury analysis. Trace mercury analysis demonstrates that the sample is completely lost in minutes because of the surface reactivity of stainless steel. The silicon coated sample receptacle did not react with the Mercury sample, preserving test integrity and reliability.
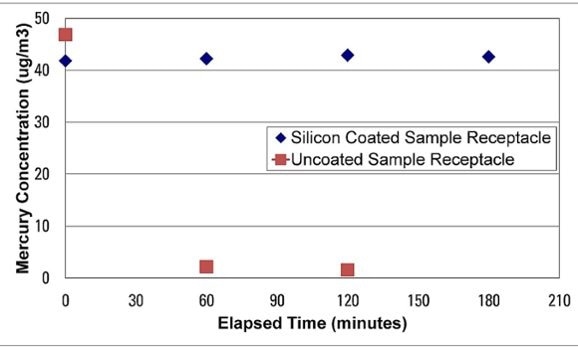
Silicon and moisture analysis
Increased reactivity can be intensified by moisture adsorption. There will be less trace moisture available in the flow path to adsorb and react with the sample or process material if the surface repels moisture. Corrosion of the surface can be escalated by moisture, which exacerbates reactivity further.
Relative hydrophobicity (moisture repelling water drop) tests show wetting of stainless steel and moisture retention (image below left) and the range of hydrophobicity available to silicon and surface modified silicon. The below right image shows the wetting of unmodified silicon compared to carbon infused (SilcoNert® and Dursan®) and polymer infused (Notak®) silicon.
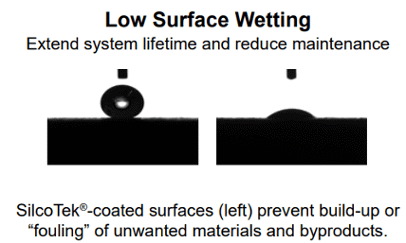
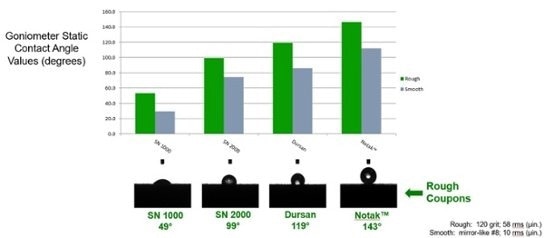
The benefit
Our silicon coatings improve product performance. Our coatings can improve moisture measurement down to part-per-trillion levels.
Benefits include:
- Improved corrosion resistance, less maintenance
- Reduced product contamination, improved product yield
- Better product performance
- Reduced test failures, more accurate results
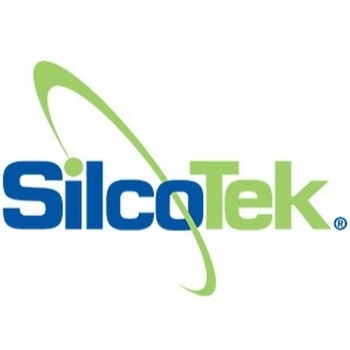
This information has been sourced, reviewed and adapted from materials provided by SilcoTek.
For more information on this source, please visit SilcoTek.