There has been a rapid growth in the use of aluminum by automobile manufacturers, resulting in aluminum rolling mills increasing in supply demand. In preference to steel, the aluminum industry is consistently resilient as manufacturers take advantage of the materials’ strength and lightness.
For example, the company, Ford, is committing to aluminum for the F-150 pick-up truck. In 2015, Ford Motor took a brave move with a new version of its F-150 pickup truck that was manufactured mainly out of aluminum, rather than steel. Now referred to as a technological marvel, the new F-150 is 700 pounds lighter than the previous version of the truck and it is able to pull heavy loads with a V6 engine compared to a fuel-hungry V8.
Aluminum manufacturers are not short of customers. Demands from the aircraft industry, food packaging and building industry have rocketed, among others. However, one area in which aluminum rolling mills are struggling is the scrapping of aluminum coils. These are damaged during transport, annealing, cooling and handling operations. For aluminum processors, the lessening of this scrap is a large problem. It can be the reason for increased overheads due to the energy costs of melting down and recasting scrap metal.
.jpg)
Image Credit: Mid-Mountain Materials, Inc.
Can Tray Pads Help?
The answer to avoiding bruising and streak damage to coils is easier than you might think. Usually, hot coils are placed on specifically designed steel trays to prevent them from moving during transportation. Much of the surface damage can occur during this stage, and several coils can suffer areas of ‘bruising’.
This is a result of the movement of aluminum on steel surfaces, creating contact predominantly in the heated state, causing abrasions and denting. Thus, it is important to avoid steel to aluminum contact during the transportation, handling, and annealing of hot and cold aluminum coils, billets, slabs, extrusions, and sheets.
In particular, coils have to be treated with careful attention during movement, and trays are only half the battle. The answer is to provide coils, some that could weigh more than 10 tonnes, with a soft landing. This is achieved by adding landing pads to the bare trays which are specifically designed material cushions made from heat-resistant materials, like fiberglass.
According to several studies, coil surface damage can be reduced by over 60% by using tray pads in comparison to bare trays. US company Mid-Mountain Materials, Inc. are specialists when it comes to heat-resistant materials. They have certainly been proactive in reducing scrap from rolling mills through the provision of a range of durable, high-temperature duty tray pads. Tray pads can be used for a variety of applications used in rolling, such as v-racks, sling trays, curved racks, cooling station trays, and annealing furnace rail cars.
The Range of Tray Pads
For many years, Mid-Mountain has realized the advantages of tray pads. For customers, they can lead to a notable retention of usable metal and a significant reduction in the overhead costs. Mid-Mountain has operated in partnership with several rolling mills in order to develop four standard types of THERMOPAK® Tray Pads. They are manufactured according to stringent specifications to be used in diverse applications.
.jpg)
Image Credit: Mid-Mountain Materials, Inc.
CERMEX® MT1000 Needled Fiberglass Mat is the internal padding material used in all versions of the tray pads. CERMEX® is used due to its stability during extended periods at high-temperature, with a melting point over 2050 °F – 1120 °C. On top of this, it has a high density of 9-11 lbs per ft3. Exterior fabrics are changed depending on the specific application and THERMOPAK® Tray Pads can be custom manufactured if required based on specific temperature applications.
Annealing furnaces is a high-temperature application that can require one of the two possible pad types. The ARMATEX® FIRESTAR 35 style pads are suitable for short-term exposure of a maximum 1500 °F (815 °C) and constant use of 1000°F (538 °C). In contrast, HYTEX® 1400 style pads are used for temperatures of 1400 °F (760 °C) maximum.
Additional applications that include the setting of hot coils in trays without the need for actual placement into recirculating annealing furnaces can use lower duty-temperature pads. In these areas, the highest resistance to contact surface abrasion (CSA) results in the use of the HYTEX® 700 or ARMATEX® QF40 Clear style pads.
Equally, both of these pad types display incomparable cut and abrasion resistance and thus can improve the protection of coils from mechanical damage. ARMATEX® QF40 CLEAR pads are suitable for continuous use to 1000 °F (538 °C) and short-term exposure to 2000 °F (1093 °C), while HYTEX® 700 is suitable for temperatures up to 450 °F (232 °C).
HYTEX® Textiles
HYTEX® 700 textiles are made from blended yarns of Kevlar® and glass fibers. For this tray pad cover, the blend of materials used combines the wear resistance of fiberglass with the tensile strength of Kevlar®. This results in a successful product with excellent strength and abrasion resistance at the duty temperature of 650 °F (345°C).
Its exceptional strength and dimensional stability make HYTEX® 700 particularly suited for use in heat shields and insulation. HYTEX® 1400 textiles are formed from low-alkali fiberglass yarn. The benefit of this material is its use at temperatures where E-glass products would fail. With outstanding strength, low weight, and excellent dimensional stability, HYTEX® 1400 textiles should be used where high abrasion or temperatures from 1000-1400 °F (540-760 °C) are met.
ARMATEX® Textiles
An additional and unique textile used for tray pads is ARMATEX® Firestar 35 and is manufactured from heavyweight fiberglass with the addition of a mineral coating. Subsequently, this provides effective abrasion resistance and short-term high-temperature resistance up to 1500 °F. The ARMATEX® QF 40 CLEAR is the most durable and abrasive resistant tray pad because it is embedded with refractory material resulting in the possibility of short-term exposure to 2000 °F.
THERMOPAK® Tray Pads
Furthermore, Thermopak® Tray Pads are created to minimize the in-house scrap produced throughout CSA and bruising. Mid-Mountain’s high durability/high-temperature tray pad solutions are perfect to aid the aluminum rolling mills in order for them to meet their commitments and reduce scrap coils. Thus, usable production is improved reducing overheads and increasing profits for these rolling mills.
References
- Visual Quality Characteristics of Aluminum Sheet and Plate, The Aluminum Association, Fourth Edition, February 2002
- https://mid-mountain.com/thermopak-tray-pads/
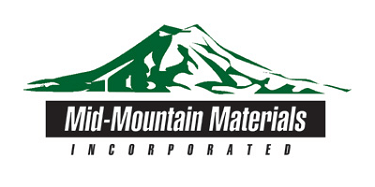
This information has been sourced, reviewed and adapted from materials provided by Mid-Mountain Materials, Inc.
For more information on this source, please visit Mid-Mountain Materials, Inc.