For automotive tire manufacturers to predict how tires will act on the road, it’s important to understand the elongation properties of the rubber. Tire rubber can be quite stretchy as it is an elastomer. So not only do you need a way to accurately measure high elongations, your tensile testing machine also requires a lot of travel on it.
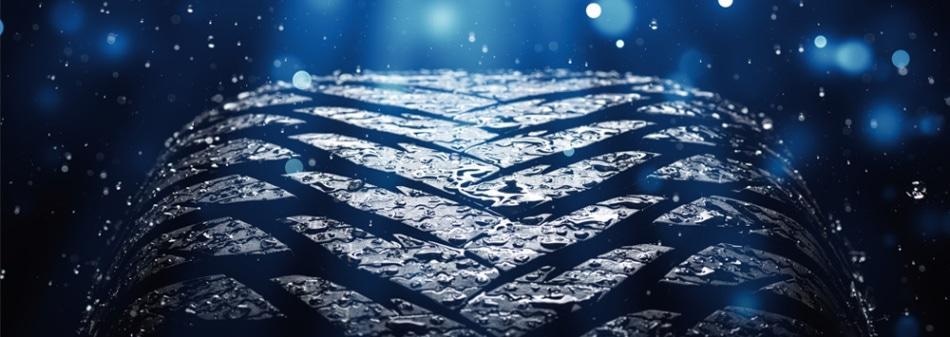
Elastomer Testing Challenges
For common standards, such as ASTM D412 and ISO 37, an extensometer isn’t needed, but they are normally recommended to ensure repeatable and accurate results. There are dozens of available options when it comes to picking an extensometer – so how do you pick the correct one?
Important considerations:
- Non-Ambient Testing – Elastomers are usually tested at a wide range of temperatures, so if that’s the case for your application, ensure your extensometer can be utilized with an environmental chamber.
- Operator Influence – Extensometers that need the operator to manually take them on an off could mean variance between tests and operators. For the most consistent results, remove as many operator-specimen interactions as possible.
- Travel – Tire rubber and other elastomers are usually quite stretchy, so your extensometer should have sufficient vertical travel, and high accuracy throughout the entire elongation.
- Throughput – Many extensometers must be put on manually, and some cannot stay on through break – which can slow down the testing process. To test a lot of specimens, automatic contacting and non-contacting extensometers can increase your throughput significantly.
Top 3 Extensometers for Testing Tire Rubber and Elastomers
1. A Non-Contacting Video Extensometer
The SVE 2 and AVE 2 non-contacting video extensometers are extremely popular because they have a large field of view which can measure high elongations, they save the operator a lot of time, and they’re the only option on this list that can be employed with an environmental chamber for non-ambient testing.
A Revolution in Strain Measurement: Instron AVE 2 Non-Contacting Video Extensometer
Features and Benefits
- Wider application range because they can be utilized with environmental chambers across a wide temperature range
- Large field of view allows you to measure up to 840 mm/34.46 in to provide strain at failure results for most materials
- Consistent results regardless of operator due to automatic gauge length measurement
- Stops premature damage to the specimen by measuring strain without touching for the most accurate results
- Meets or exceeds the accuracy requirements for elastomers, including ASTM D412 and ISO 37
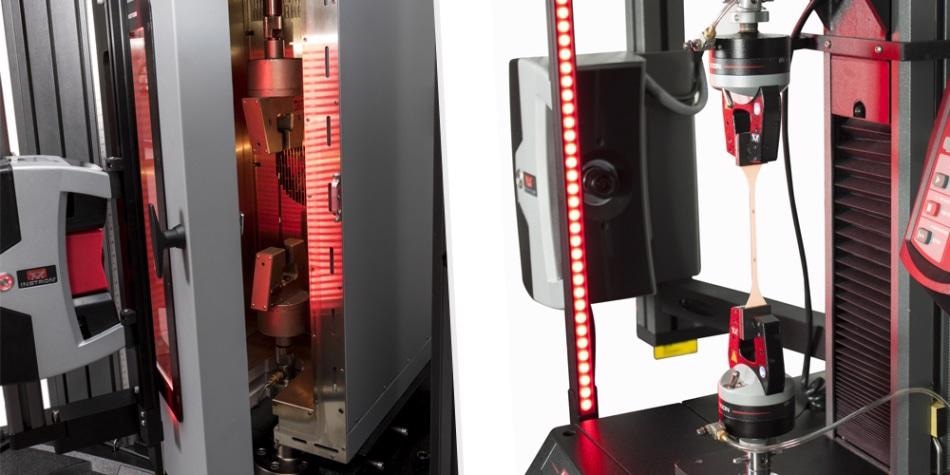
2. Automatic Contacting Extensometer
Long vertical travel and high accuracy make the AutoX750 popular for testing tire rubber. By allowing labs to take advantage of automatic gauge length positioning and attachment to the test specimen, they can also increase specimen throughput – by freeing up the operator from having to do these time-consuming steps themselves.
Testing Elastomers to ISO 37 and ASTM D412 with an AutoX750 Extensometer
Features and Benefits
- Automatic centering improves repeatability
- High travel – up to 750 mm/29.52 in in vertical travel – and measure strain through break with most materials
- The AutoXBiax can measure both axial and transverse strain simultaneously
- Automatic attachment eliminates operator influences
- Various knife edge options and the ability to adjust the clamping force to accommodate different materials
- Extremely high resolution and accuracy (+/- 1 um)
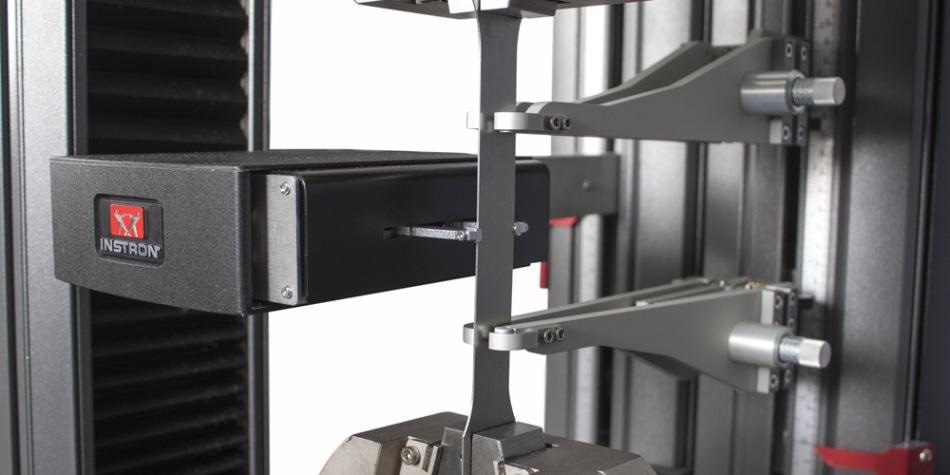
3. XL Long Travel Extensometer
For measuring the elongation of tire rubber, the XL Long Travel Extensometer is also a great choice. It is designed specifically to deliver precise measurements for highly extensible materials, and also permits testing the sample through rupture without damaging the extensometer or otherwise disrupting the test routine.
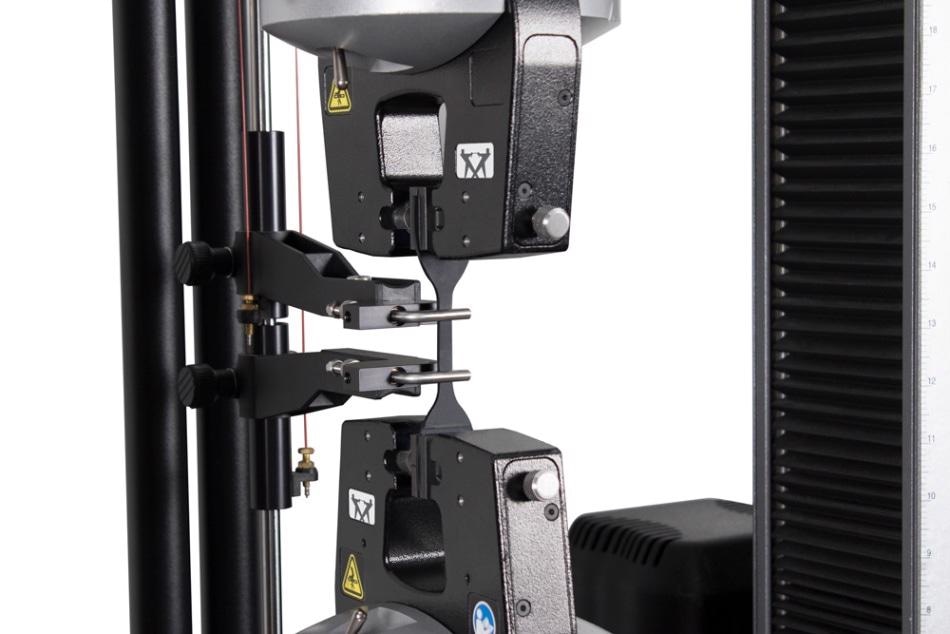
Features and Benefits
- Counterbalanced for minimum force on sample
- High travel – up to 750 mm/29.52 in in vertical travel – and measure strain through break
- Quick release clamps for efficient specimen insertion and removal
- Adjustable clamping force on the knife edges reduces premature failure of the specimen
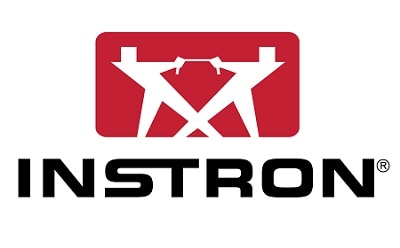
This information has been sourced, reviewed and adapted from materials provided by Instron - USA.
For more information on this source, please visit Instron - USA