.jpg)
Do you want to improve your product, process sampling or emission monitoring (CEMS) process? Below are various ideas on solving reliability and contamination problems.
Customers who experience sampling reliability and material contamination problems often ask how they can improve flow path inertness and sample system reliability. Replacing 100 meters of sample tubing routed high up among the pipe-work is a much more difficult task than replacing chromatograph columns. This blog will discuss factors that improve CEMS emission monitoring and process sampling.
This blog will discuss:
- How moisture contamination can impact sample quality
- The keys to reliable sampling
- Sources on proper heat trace tubing installation
- How maintaining sample flow path integrity, inertness and cleanliness prevents test and process failures
Sample Integrity
.jpg)
Sample condition is the biggest consideration with regards to contamination and sampling reliability. It is important to know how clean or dirty the sample stream is. Sample filtration and cleaning are needed to remove contaminants if there is a lot of particulate coming into the line.
A build-up of participates could become adsorptive and degrade test results. After the particulates have been removed, an inert coating should be applied to the entire flow path which will minimize particulate stiction and sample adsorption. An analytical sample flow path should never be cleaned with steam. Steam, particularly process steam systems, contain particulates that adsorb test samples and this will disrupt system calibration. If used in the flow path, particulates can also damage inert coatings.
Manage Moisture
Accumulation of moisture in the sampling system is another area of potential poor reliability. The coating life will be decreased if there is any point of condensation in the system and if there are acids or bases that form in water from the steam/water contact. This will adversely impact sample reliability. If a system is poorly designed or installed, a cold spot or drip can form in the heat trace tubing which will result in moisture condensation and accumulation.
.jpg)
As a result, HCl or Sulfuric acid can form which can attack the tube surface. This will eventually cause a hole in the inert coating layer and the tubing and create active iron particles which ultimately results in tube failure. Moisture can be managed by coating the surface in an inert, hydrophobic coating as this reduces the surface energy and increases moisture repelling properties. The graph below compares H2S stability of a dry vs. wet sample environment. The wet environment had 18% less H2S in the sample after 14 days.
Keys to Reliable Sampling
A well-designed sample system featuring an inert coating will last for many years without issue for most applications. A study presented at the 2011 ISA-AD Conference in Houston, TX, by BP, highlighted a SilcoNert® 2000 coated flare gas sampling line that had been delivering accurate results without issue for two years. The system continues to provide accurate, reliable sampling results despite this being a dirty application with many potential contaminants and failures. This is due to the first-rate design and maintenance.
.jpg)
Keys to reliable sampling are:
- Proper installation – avoiding drips or areas for moisture to accumulate in the tubing
- Install filtration – to avoid build-up of active particles
- Elimination of potential cold spots in heat trace tube
- Proper coating selection for the sampling application:
- Dursan® for extreme environments (particulate abrasion, acid/base exposure etc)
- SilcoNert® 2000 for low level sulfur/H2S sampling
- Proper material selection for the environment:
- Materials specified for the sampling environment
- Inert coatings
Heat Trace References
To get design and installation pointers, ask the heat trace companies about their experiences with installing and servicing lines used in your application. SilcoTek® works extensively with Thermon Manufacturing Company and O’Brien Corporation.
.bmp)
These companies are market leaders and consequently have a large amount of experience and technical expertise with regards to installation and maintenance of reliable sampling systems.
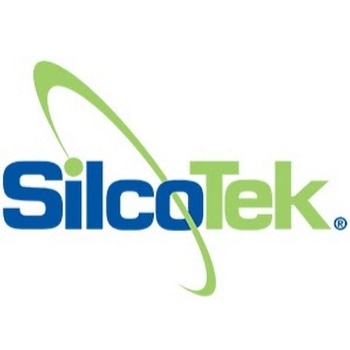
This information has been sourced, reviewed and adapted from materials provided by SilcoTek.
For more information on this source, please visit SilcoTek.