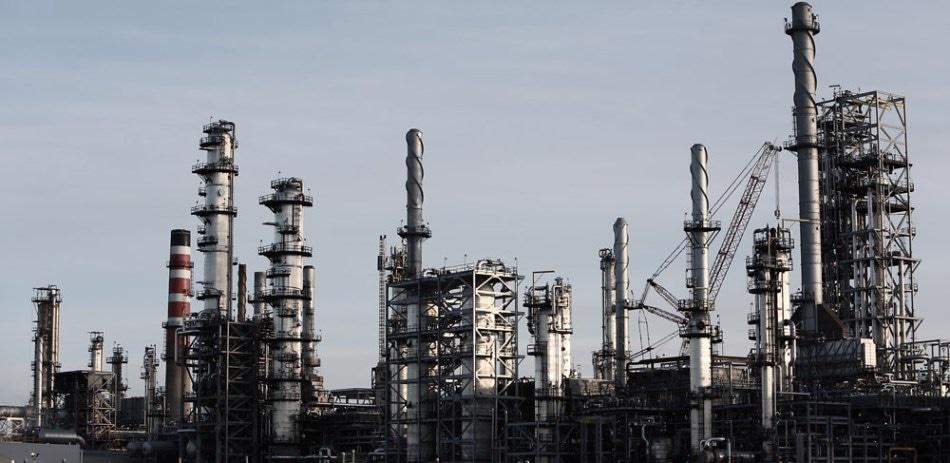
This article looks at solving process sampling problems by focusing on the three Ms. The three Ms are as follows:
- Materials
- Manage
- Maintenance
This article will discuss:
- How managing three key aspects of the sampling flow path can prevent failures and improve results
- How a few simple maintenance tips can go a long way in preventing failures and saving money
- How to improve air quality measurement and process control through material selection
Materials
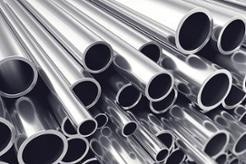
Material selection is seldom as easy as pulling an available tube from the stock room. Good sample transport system design incorporates various factors in material selection. These include surface inertness/adsorption, corrosion resistance, workability, functionality, cost and durability. The materials used in the sample flow path need to address all the factors and requirements of the sample system.
Selecting materials that are compatible can help to avoid sample system failures such as:
- Slow calibration or inability to calibrate systems
- False analyzer readings
- No results, then spikes in readings
- Variable readings
- Poor system durability and wear resistance
- Frequent maintenance and component replacement
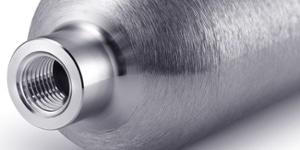
Stainless steel is the most commonly used material sampling transport systems because it checks nearly all of the design boxes. However, stainless steel can corrode and absorb test analytes under extreme conditions which causes inertness issues and premature system failure.
Inert materials, for example silicon coatings, are used as a backstop to stainless steel’s weak points. This improved process measurement quality and durability. The process can be started by selecting the right inert material, or coating, for the application.
Inert materials should be selected based on:
- Target performance (i.e. ppm or ppb inertness, corrosion, etc.)
- System exposure/environment
- Maintainability
- Expected life of the sample system
- Analyte
Manage Corrosion, Inertness and Design
Managing corrosion helps to assure that the sample flow path does not become contaminated or damaged by corrosion. A corrosion free flow path assures nonreactivity by preventing particulate generation and adsorption. Coat analytical flow paths with inert materials that will not interact with cleaning materials or analytes and will act as a barrier to corrosive effects.
Comparative immersion tests of Dursan®, an inert silicon coating, and an uncoated stainless steel test coupon in 10% (vol.) hydrochloric acid shows the high corrosion potential of stainless steel. The beaker and test coupon (below) show pitting of the coupon surface and green metal ion contamination of the acid solution. When the acid beaker remains free of contamination the Dursan coupon shows littles corrosion.
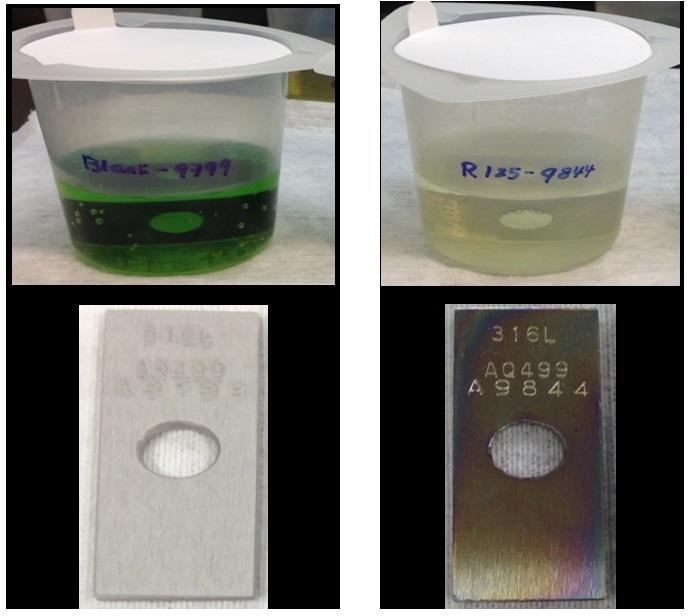
The adsorptive particulates produced by corroded stainless steel surfaces can impact operating integrity. Robust coatings, like Dursan, prevent corrosive attack by orders of magnitude. Sulfuric acid comparative tests (below) show the Dursan coated coupon improves corrosion resistance by approximately 90%. Selecting appropriate material can have a big impact on operating cost, test quality, safety and system durability.
Manage Inertness
Molecules that can adhere or be adsorbed by stainless steel include sticky compounds like H2S, mercaptans and protein molecules. Compounds can stick to the surface and cause inaccurate results even in high velocity flow paths. Inert coatings such as Dursan® and SilcoNert® prevent surface interaction with stainless steel which allows the complete sample to reach the analytical instrument.
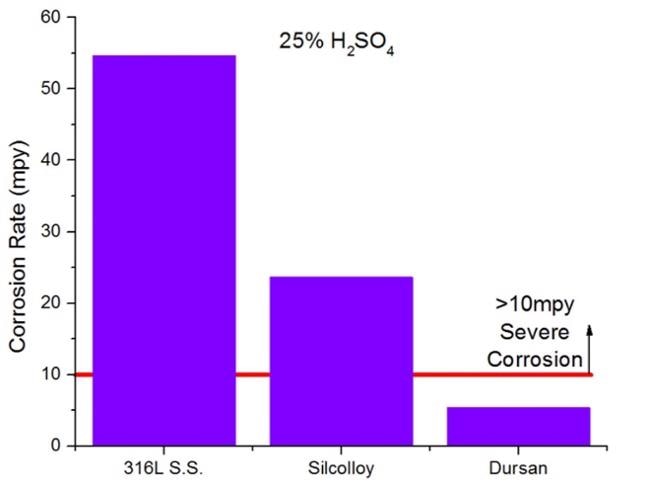
Adsorption/Desorption Effects
The release of active compounds in the sample transport system as a result of adsorption can severely distort analyzer results. Failing to manage adsorption can result in false negative results or delays in response. Adsorption of the sample can result in delays of 90 minutes or more. After the delay in response sticky compounds like sulfur can desorb or release from the surface which causes spikes in analyzer readings.
Comparative testing of PTFE, aluminum, gold, SilcoNert®, Dursan® and stainless steel exemplifies the difference an inert, non-reactive surface can make on overall test performance. Even after 15 minutes of exposure, the uncoated stainless steel surface showed zero response (complete adsorption) of the sample. The SilcoNert coated surface showed consistent results and almost immediate response with little adsorption.
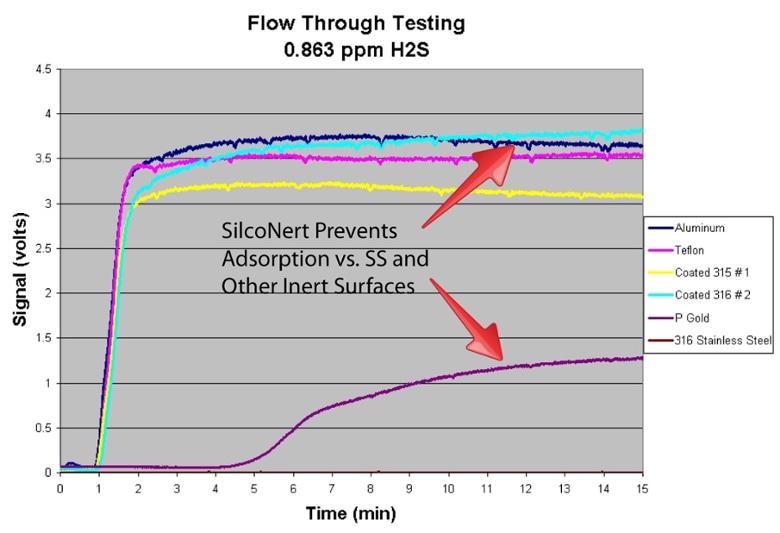
Design Factors for Improved Process Analytical Performance
A recent paper by Phil Harris, Hariteck, and O’Brien Analytical highlights how common sample transport design issues can distort analytical results. This paper also recommends ways to improve sample system reliability.
According to the Harris paper, key factors to be considered when specifying the sample flow path include:
- Sample gas composition and dew point/phase behavior
- Length of the sample line run
- Species to be analyzed
- Required gas velocities and response times
- Operating pressure and temperatures
Maintenance
A major contributing factor to achieving reliable process sampling test results is following a maintenance plan. This helps to maintain process yield and regulatory compliance. Maintenance can entail complex test and validation programs but can also include some pretty basic hands-on techniques that don't require much skill, only observation and some organization.
Some easy maintenance tips are:
- Inspect for leaks. Look for signs of leaks such as drip stains or unusual odors.
- Visually inspect for corrosion by looking from rust stains. Disassemble sample cylinders or sample flow paths to inspect internal components.
- Look for worn seals and gaskets. When inspecting for corrosion, check seals and gaskets for wear. Replace gaskets whenever disassembling a system.
- Observe wear points. Check for areas of metal-to-metal wear or trace metal shavings.
- Document inspections and key component age and use.
- Inspect SilcoTek® coated components for wear or damage. The rainbow color will begin to change or be lost entirely if a coated surface is being eroded or compromised. The Recommended Care Guide contains some easy ways to maintain coated surfaces.
- Check for delamination of PTFE coated components. PTFE coatings can delaminate from surfaces and compromise test results.
This article has described some of the key factors to consider when designing for and solving process sampling problems. There are undoubtedly other key areas to consider but the Ms will get you started on the track to error-free, low-cost process sampling.
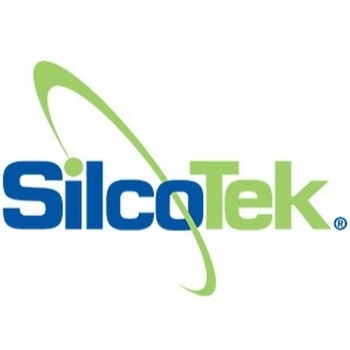
This information has been sourced, reviewed and adapted from materials provided by SilcoTek.
For more information on this source, please visit SilcoTek.