This article looks at how the rapid response times and outstanding repeatability of an on-line FT-NIR analyzer provide comprehensive and safe real-time data while enhancing the running of hydrofluoric acid alkylation units.
.jpg)
Refinery. Image Credit: ABB Ltd.
Overview
In the initial years of petroleum refining, the majority of gasoline blending components were composed of straight-run material taken directly from crude oil distillation units. Refineries were essentially simple oil boilers. The first conversion units were straightforward and aimed at the reforming of straight-run naphthas to produce higher octane blending components for better product quality. During World War II, the situation was given a substantial boost when, for obvious reasons, there was a frantic need for high-octane aviation gasoline (military aircraft during that period were fitted with reciprocating piston engines fueled by high-octane gasoline, instead of jet engines running on kerosene).
One of the solutions to this requirement for high-octane gasoline was the development of a refinery conversion unit — the hydrofluoric acid (HF) alkylation unit, producing alkylate, which is made up mostly of c7 and c8 isoalkanes that possess superb gasoline blending properties, high octane and zero aromatics content.
HF Alkylation Unit
The HF alkylation unit (HFU) is still of key significance to this day. It has a critical role to play in providing one of the most vital feeds to the end products of gasoline blending pool. Its importance has increased side by side with the growing number of fluid catalytic cracking (FCC) units in refineries. The FCC enhances the heavy end of crude distillation by catalytically cracking heavy feeds into lighter products such as FCC gasoline and light cycle oil which can be used, either directly or after hydro-treating, in end product blending operations. The shortcoming of this process is that light olefins, usually propene and butene, are also created in FCC operations. These are basically worthless as feedstock.
Likewise, in any crude distillation process, an excess of light end products such as butane tend to be formed that are of limited use; n-butane can simply be converted to isobutane, and in this form, it joins the FCC c3 or c4 olefins (propene or butene) as the blended feeds to the HF alkylation unit. The HF alkylation unit performs the crucial role of upgrading these byproducts to high-value alkylate, which is then used as a gasoline blending component. This economically vital task of sweeping up the c4 olefins from the FCC and the c4 isoalkanes from the crude oil distillation unit and changing them, through the HF alkylation process, to isooctanes continues to be of great importance in petroleum refining.
In the last 15 years, gasoline formulation requirements, as driven by government environmental agencies in most countries (but led by the EU and the US), have been considerably sharpened. Demands for lower sulfur, lower RVP, lower aromatics, lower benzene, and lower drivability index (a mixture of fuel distillation properties) strictly limit the options for refiners in their final product gasoline blending operations. Therefore, alkylate made by the HFU is of extraordinary value to refineries in their struggle to cope with environmental and other legal restrictions on their operations.
As a result, refiners operating HF alkylation units are under growing pressure to maximize unit throughput, refine product quality and yields, and at the same time ensure safe operations with low environmental impact. Legislation is becoming tighter and tighter on gasoline quality, and public and regulatory scrutiny of the use of hydrofluoric acid has increased, thus leading to reliable and efficient operation of HFUs of crucial importance to the overall profitability and reputation of petroleum refineries.
The efficient running of an HFU is a tough task and dependent on the maximum testing of operating systems. This is because of several industry-specific limitations and operating problems that stretch the processing capability of the plant.
.jpg)
The HF alkylation unit processes olefin feed and isobutane to create high-value alkylate product. Image Credit: ABB Ltd.
Operating Issues
- HFUs should be able to handle feedstocks that regularly differ in contaminant levels, hydrocarbon composition, and volume because of upstream operating complexities. Operators have the tough challenge of reducing iC4 recycling and related utility costs while making alkylate of the preferred quality with minimum acid consumption.
- The units should be run in a safe manner regardless of the ever-present potential for acid runaway, accelerated equipment corrosion, and related HF release.
The stress on HF alkylation units is further increased due to the continuing trends within the petroleum refining sector.
Industry Trends
- The continuing expansion of FCC units and the addition of new cracking catalysts to gratify gasoline growth also give rise to the creation of more alkylation feedstock
- The ongoing trend of increased residue cracking and upgrading capacity creates more complex and difficult alkylation feedstock
- There is a growing interest in C5 olefin processing as a way to return volatile components to the gasoline pool while boosting product volumes
- The constant tightening of legislation regarding gasoline quality further limits the use of certain current blend components
Each of the trends requires the HF alkylation unit to be more versatile in managing increased and varying feedstock while preserving unit effectiveness and alkylate quality. The perfect blending characteristics of alkylate make it a crucial element in matching refinery profit targets and fulfilling fuel quality legislation.
ABB TALYS ASP400-Ex FT-NIR Analyzer with HF Acid Area Field Sample System
The key process parameters of HF alkylation units are not easy to monitor. Historically, it depends on slow, costly, and potentially unsafe manual sampling of the recirculating hydrofluoric acid catalyst for laboratory evaluation of its strength and level of critical contaminants (such as water and fluorination by-products [known as acid soluble oils]).
HF acid purity determination is the main control parameter for HFU control and optimization, given that it can be delivered rapidly enough to spot process unit upsets, such as transient shifts in acid strength and contamination events due to upstream disturbances in, for instance, FCC operation.
.jpg)
Image Credit: ABB Ltd.
Monitoring HF Acid Recycle Purity Using FT-NIR
- Alkylate quality optimization — The RON, RVP, and distillation properties of the alkylate product of the HFU are important for its use in downstream gasoline blending. These parameters are impacted by HF catalyst purity, and particularly by water content, which must be enhanced within an appropriate operating window. The water content of the HF acid recycle stream is susceptible to feed contamination events, and these must be picked up and dealt with immediately.
- Corrosion mitigation — Corrosion mitigation causes severe lower limits on HF acid purity and upper limits on water content. Keeping within demarcated operational windows extends HFU turnaround times, greatly decreases maintenance costs, and limits the danger of HF discharge into the environment.
- HF acid consumption — Correct working of the HFU relies on the effective separation of hydrocarbon product from the acid catalyst in the acid settler. If there is an accumulation of acid soluble oil (ASO) byproduct and HF acid is consumed (thus reducing acid strength), the process can fail, resulting in fast consumption of the remaining acid — a so-called acid runaway event. Such an event is very costly, but is an unavoidable risk of HFU operation. A close observation of acid strength and the percentage of ASO byproduct can considerably reduce the probability of this occurrence.
The main breakthrough in the formation of a strong and useful process FTIR analytical solution for HFU monitoring and optimization came with the advancement of an accurate and precise pre-calibrated chemometric model for the necessary process variables (water%, HF acid strength, and ASO%).
The traditional laboratory reference methods for these measurements are not up to the mark and, in contrast to the usual approaches of analyzer calibration, do not provide a dependable basis for the development of a precise calibration model. Luckily, the HF acid recycle stream is a fairly simple composition. This enabled the development of the vital universal calibration model on the basis of a gravimetrically prepared calibration standard run in a laboratory-scale pilot alkylation reactor under real-life process circumstances — but without any olefin feed, to maintain precise acid composition during the run.
This technique, pioneered by Conoco Phillips the 1990s, yields an extremely reliable pre-calibration for the ABB HF Alkylation analyzer, which is always delivered fully pre-calibrated without the need for any additional on-site model development.
A huge part of the success of this application was the creation of a consistent safety-engineered field sample panel that is low maintenance and requires marginal field intervention inside the acid area (which in an HFU requires full C-suit personal safety equipment).
.jpg)
The TALYS-HF on-line process analyzer measures complete HF acid purity. Image Credit: ABB Ltd.
The use of a fiber-optic-based process FTIR analyzer is preferably suited for this type of application. It allows a remote field-based acid-area sample flow cell and related safety and sample conditioning system to be physically separate from the analyzer optics station (which is typically located in a control room or similar safe area). This setup is vital when dealing with the online analysis of an extremely risky process stream such as HF acid.
An extra advantage of ABB’s FTIR technology is its ability to be expanded to track numerous process streams with a single analyzer. In certain HFUs, this enables a requirement for two acid streams to be observed (for instance, the chief acid recycle and the acid regeneration overhead) in real time, which greatly enhances HF acid purity control and regeneration efficiency.
Besides these advantages, there are other valuable process control options for the HFU process FTIR analyzer. Apart from the HF acid catalyst monitoring role, there are a number of crucial hydrocarbon streams in the HFU that profit from reliable, low-maintenance, and fast compositional analysis. The olefin feed stream and the iC4 recycle stream from the isostripper are the most critical. Collectively, these two streams directly impact the purity of the feed to the HFU, which in turn has a direct influence on HF acid consumption. Real-time process data on these streams, together with the HF acid purity measurement, provide a substantial enhancement in unit operational stability.
.jpg)
.jpg)
ABB FTPA2000-HP20 Multi-Channel System for Full HF Alkylation Unit Optimization. Image Credit: ABB Ltd.
HF Alkylation Unit Optimization Using FT-NIR
In the multi-channel version of the analyzer system, usually one stream is kept aside for the most crucial HF acid recycle analysis (HF stream #1) and a further field acid area sample system can be used either for a second HF stream, for instance, the HF regeneration overhead on a few units (HF stream #2), or further HF-tainted hydrocarbon streams such as the iC4 Recycle. Moreover, HF-free hydrocarbon streams (olefin feed or alkylate product) can be incorporated using sample systems with conventional metallurgy, which may be situated outside the unit acid area.
Overall:
- Alkylate yield, feed rates, and alkylate octane are maximized to an economic best, conditional on operating constraints
- Isobutane-to-olefin ratio (usually around 10:1 to minimize side reactions, but regulating yield) can be decreased while matching alkylate quality and yield targets with minimum acid consumption
- Isobutane makeup rate can be enhanced while keeping in mind iC4 inventory limitations
- Acid quality is maintained in the finest operating range for ASO, HF, and water content
This leads to:
- Alkylate octane improvements made possible as the water content of the catalyst can be properly managed
- Lower acid inventory, as acid makeup requirements are decreased
- One of the leading licensors reports that an increase in water content from 1.0 to 2.0 wt% can deliver over $1 million in profits for a 10,000 bpd unit
- Less frequent approaches to runaway conditions
- Less aggressive regenerator operation and lower acid losses
- Acid-to-hydrocarbon ratios and reactor temperature are regulated to enhance product quality and overpower ASO production
- Higher quality alkylate and yields
- Reactor conditions are enhanced to handle differences in fresh feed compositions
- There is a huge reduction in the risk of unexpected unit corrosion because of better acid strength control
.jpg)
Examples of FT-NIR analyzer measurement points for full HF alkylation optimization. Image Credit: ABB Ltd.
Take into consideration the considerably enhanced precision of the on-line analyzer compared with equivalent laboratory test results. Repeatabilities are 0.1% for HF% and ASO% and 0.03% for H2O% (absolute) by the on-line FT-NIR technique versus 5× to 10× worse by standard test techniques (acid-base titration, gravimetric, and Karl-Fischer titration).
.jpg)
Run-time data from ABB on-line FT-NIR HF alkylation unit analyzer: two days steady-state conditions HF%, Water%, and ASO%. Image Credit: ABB Ltd.
.jpg)
Typical piping diagram and sample take-off arrangement—sample take-off from acid cooler downpipe and return to iC4 recycle pump-suction via eductor or other low-pressure return where available. Image Credit: ABB Ltd.
Conclusion
In this article, the use of a precalibrated on-line process FT-NIR analyzer system for monitoring HF acid purity in the HF acid catalyst recycle stream for HF alkylation units has been reviewed. The critical impurities in the acid recycle stream (acid soluble oil [ASO] and water) have considerable impacts on core process parameters such as alkylate octane and unit corrosion rates.
Furthermore, fast deterioration in HF acid quality can take place because of upstream process unit (and thus HFU feed) upsets.
The traditional analytical control for the unit was based on frequent (daily) manual field sampling for HF acid samples and arduous laboratory workup using standard chemical techniques. These techniques exposed refinery personnel to the probability of HF release, had poor precision, and were slow to implement. The on-line analyzer system, therefore, provides a lot more rapid, considerably more precise, and very much safer data for unit optimization.
References
- NPRA, Annual Meeting, San Antonio, TX, “Advances in Hydrofluoric Acid Catalyzed Alkylation,” March 23-25, 2003
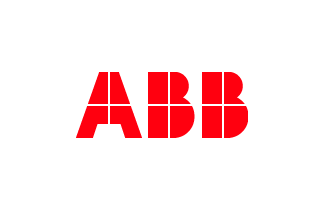
This information has been sourced, reviewed and adapted from materials provided by ABB Measurement & Analytics - Analytical Measurement Products.
For more information on this source, please visit ABB Measurement & Analytics - Analytical Measurement Products.