In areas where side-draw quality estimates are required, it is typical to use inferential models, depending on empirical correlations between the process parameters (flow/pressure/temperature) and the reconciled true boiling point (TBP) curve of the nominal crude feed assay.
.jpg)
Refinery. Image Credit: ABB Ltd.
Process FTIR employing a fiber-optic-based configuration with separately heated sample flow-cell cabinets for individual process streams enables feeding multi-stream, multi-property, real-time, accurate product quality data rapidly at a suitable data rate to the CDU on-line optimizer. This will enable control of side-draw stream cut-points and qualities, allow more effective optimization of the unit, and crucially prevent yield losses from a high-value product into lower-value streams owing to pump-around control and poor heat-balance.
The Crude Distillation Unit (CDU)
The crude distillation unit (CDU) is probably the highest throughput process unit on the entire refinery, and considering that commonly there may be two, three, or even more parallel crude distillation trains, one may expect that the operation of the CDU will receive considerable attention in terms of advanced process control (APC) — and this expectation would be right. Yet, at the same time, the CDU is not essentially the unit in the refinery where the most attention has been paid to on-line process analytics, until recently. What is the reason for this obvious contradiction?
.jpg)
Crude distillation unit (ADU and VDU) in a whole-refinery context. Image Credit: ABB Ltd.
The nature of the CDU is responsible for this. Conversion units are the operating units further downstream in the refinery, and they do chemistry — alkylation, cracking, hydrotreating, reforming, and isomerization — all involving (at times significant) molecular rearrangements.
No (deliberate) chemistry occurs within the CDU — it is only a fractionator. As a result, a mathematically rigorous model of the CDU operation can at least be tried out, and APC implemented with the help of standard techniques through multiple control loops, pressure/temperature/flow measurements, and heat/mass balances. In areas where set points and side-draw stream quality estimates are required as part of the APC scheme, it is typical to use inferential models, based on empirical correlations between the physical process parameters (flow/pressure/temperature), laboratory determined product stream qualities, and the reconciled (that is corrected) TBP curve of the nominal crude feed assay.
It must be noted that this type of modeling exercise is substantial and the models applied in these inferential techniques can be incredibly complex, needing hundreds if not thousands of laboratory check samples.
.jpg)
Heat balance, pump-arounds, and cut-points in CDU operations. Image Credit: ABB Ltd.
Real-Time Analysis of CDU Process Streams
Throughput and Quality
A proper understanding of the nature of the crude feed is the starting point for optimized CDU operation. Considering the extremely high and variable value, in terms of dollar price, of crude, it is increasingly significant to know this so that economically optimized buying and blending choices can be made.
Crude feeds are traditionally characterized by a generic assay (that is typical of the field, and not specific to any shipment) with a TBP curve. This is the main input to the typical APC model — without it, the estimations of side-draw quality, and thus the accuracy with which precise cut-points can be set, are useless.
Often, this input is often neither known nor estimated with adequate certainty. It would usually have to be achieved, if an update was required, through a lengthy and costly lab test procedure in which a complex physical distillation apparatus is involved. Actually, lab-based FT-NIR techniques have plenty to offer here, and crude assay databases exist, which enable fast lab assay using that technique.
The side-draw end boiling points and the middle distillate cold properties (for example, cloud point, flash point) will be the most critical control parameters for the APC scheme. Moreover, true on-line direct measurement of the desired large number of properties through discrete, slow physical property analyzers is prohibitive in terms of capital cost, maintenance cost, and installation cost.
These traditional analyzers also provide data over extended 20–80 minute cycle times, in strong contrast to the input to APC from inferential models providing estimations every few minutes.
Real-Time Analysis of Crude Feed and Side-Streams Using Process FT-NIR Spectroscopy
Process FT-NIR using a fiber-optic-based configuration with separately heated sample flow-cells for each necessary process stream (crude feed and side-draws), complete with appropriate sample conditioning for water removal, enables rapid multi-stream, multi-property, real-time, accurate product quality data to be fed at a suitable data rate to the CDU on-line optimizer.
Considering the rapidly changing and dynamic patterns of crude purchasing and blending, pushed by harsh market economics, combined with the misgivings of TBP reconciliation and the complexity for inferential model estimators of precisely predicting side-draw end-points, real-time on-line analysis with Process FT-NIR is turning out to be both increasingly attractive and increasingly implemented.
.jpg)
ABB FTPA2000-HP260X multi-channel FT-NIR on-line analyzer for multi-stream CDU optimization. Image Credit: ABB Ltd.
Case Study Using FT-NIR for CDU
This article describes the installation and operation of an on-line process FT-NIR analyzer system in a European refinery with a vacuum and crude distillation capacity of about 160,000 barrels per calendar day (bpcd), roughly 6.1 million tons per annum (Mtpa). While the refinery in question has a Nelson Complexity Index of 11.5 and extensive hydrocracking and thermal capability, it has restricted deep residue upgrading capacity. Therefore, correct and optimal operation of the CDU is crucial for the effective production of middle distillates.
The project was intended to offer real-time feed and product stream qualities for the crude feed to the CDU as well as for six rundown side-streams, such as heavy naphtha (HN), light naphtha (LN), straight-run gasoline (C5-C6), atmospheric gasoil (AGO), heavy gasoil (HGO), and kerosene (KERO). There is a wide range of different arrangements of on-line process FT-NIR, including extractive multi-cell using fiber-optics, extractive single cell, and in-line using fiber-optics and probes. For FT-NIR analyzers, the different aspects of the CDU application are likely to converge on the extractive multi-cell method.
Firstly, these are the extensively different temperatures, viscosities, and densities of the sample streams, which render it unfeasible to physically stream-switch between streams in one or several cells, and secondly, the spectroscopic requirements of the application. At large, heavier samples’ FT-NIR spectra change less quickly with variable sample qualities; therefore, an application on naphtha or gasoline is usually inherently simpler, from a modeling standpoint, when compared to a crude feed or heavy gasoil application. The lack of sample control inherent for in-line sampling with fiber-optic probes and the potential for extra distortion in the spectra make the multicell extractive sampling method the most reliable.
An ABBFTPA2000-HP260 8-channel fiber-optic multiplexed FT-NIR instrument was the analyzer used in this application. One benefit of this specific analyzer arrangement is that it enables assigning separate NIR detectors to individual sample streams. This is very useful when a crude feed stream is included in the application. Perfectly usable is the NIR spectrum of a raw crude feed sample and similar to the spectra of light hydrocarbons in the long-wavelength NIR (4000–5000 cm-1) combination band region.
Conversely, in the shorter wavelength overtone band region (5500–9500 cm-1), the crude oil’s spectrum quickly becomes unusable because of the absorbance baseline offset and curvature caused by asphaltene particulates and the tail of near-visible region optical absorbance bands. In brief, while crude oil is transparent in the long-wave NIR, it is black elsewhere.
.jpg)
Combination region (4000 to 4800 cm-1) FT-NIR spectra of white to black hydrocarbon products. Image Credit: ABB Ltd.
The following table shows a summary of the fiber and detector stream allocations for the FT-NIR analyzer used here.
Stream allocations with cell pathlengths, detector types, and operating range
Stream name |
Range
(cm-1) |
Fiber type |
Detector type
(all te cooled) |
Cell pathlength
(mm) |
Cell temperature
(°C) |
c5c6 |
5500 to 9500 |
Low OH silica |
InGaAs 2.1 |
2 |
25 |
Light Naphtha |
5500 to 9500 |
Low OH silica |
InGaAs 2.1 |
2 |
25 |
Heavy Naphtha |
5500 to 9500 |
Low OH silica |
InGaAs 2.1 |
2 |
25 |
Kerosene |
5500 to 9500 |
Low OH silica |
InGaAs 2.1 |
2 |
25 |
AGO |
5500 to 9500 |
Low OH silica |
InGaAs 2.1 |
2 |
75 |
HGO |
5500 to 9500 |
Low OH silica |
InGaAs 2.1 |
2 |
75 |
Crude Feed |
4000 to 4800 |
ZrF4 |
InAs |
0.5 |
35 |
Each stream including the crude feed stream is directed through a suitable sample conditioning system to a temperature-controlled fiber-optic liquid sample transmission cell, where the FT-NIR spectrum is recorded (about 1 minute data acquisition per stream).
The FT-NIR analyzer model in question employs merely software selection of a dedicated detector for each measurement channel, and therefore, opto-mechanical selection is not needed.
Sample Conditioning for CDU Streams
In this type of application, each fiber-optic-coupled sample liquid flow transmission cell was incorporated into the slipstream of a sample conditioning system. The design of the cell enables numerous sample temperature-control strategies, such as independent sample temperature control using a heat exchanger upstream of the cell, thermostat-controlled heat-exchange fluid flowing through the cell body, or enclosure of the entire cell assembly and sample conditioning system in an insulated temperature-controlled cabinet.
Each of these methods are valid, and the physical circumstances of the installation will decide the choice.
In this specific case, there was a dedicated environmentally stabilized sample flow panel room so that the sample’s simple upstream temperature control was adequate. Each CDU stream will include different sample conditioning. For most, minimum temperature control and surplus water removal through coalescing filtration will be needed. Ahead of any coalescing filter, it is incredibly important that the temperature of the sample stream is reduced below the temperature of the measurement cell so that all water falling out of solution at that temperature is removed beforehand.
All flow cell circuits and flow cells were fitted with low-flow alarms and flow metering, and also RTD temperature probes were integrated into the cell body and connected through an internal Modbus to the FT-NIR analyzer to give positive assurance of system status.
.jpg)
Sample conditioning systems and sample flow-cell panel, typical functional blocks. Image Credit: ABB Ltd.
Sample Conditioning for CDU Streams
A sample-shutoff stop valve (SSOV) assures the sample phase integrity at the time of measurement. This SSOV operates on each measurement cycle in order to block the sample in the flow cell under the operating pressure of the sample system (check valves, pressure regulators, and other system details are not shown in the Figure).
Operation of the SSOV is done with the help of an air-actuator, whose solenoid is under the control of the analyzer through an internal ABB PLC module. In practice, based on the physical space available for installation and the ambient temperature control of the environment (well-controlled in this case), the functionality of the two cabinets in the schematic can be integrated together in a single panel as in the site photograph illustrated below.
For the two heated sample streams — HGO and AGO — an extra cabinet enclosure with active heating and temperature control, performed by the FT-NIR analyzer controller, was given for each panel.
The sample flow cell itself is developed with two main design objectives — firstly, ease of use and maintainability in the field, and secondly, spectroscopic transferability and equivalence compared to data from a traditional laboratory FT-NIR analyzer sample transmission cell. The majority of sample fiber-optic flow cell designs employ short focal length quartz lenses so as to combine the fast-diverging light exiting the fiber tip, with a compact-size flow cell.
.jpg)
Sample conditioning and sample flow-cell panel with fastloop filter, heat exchanger, and coalescer. Image Credit: ABB Ltd.
This presents two issues. First, the fast refractive optics produce chromatic aberrations that distort the NIR spectra and prevent achieving the second design objective, and second, the close coupling of the fiber-optics and cell implies that any maintenance operation will force the removal of the fiber-optic connection. Both problems are avoided by the present cell design, which uses reflective coupling (off-axis parabolic mirrors that prevent spectral distortion) as well as a large-size separated sample flow cell block that can be easily removed and maintained without causing any disturbance to the fiber-optic arrangement.
.jpg)
Fiber-optic sample flow cell (detail). Image Credit: ABB Ltd.
Conversely, the sample conditioning requirements for the crude feed stream are more substantial, and go further than simple water removal and temperature control. Normally, the stages involved in such a crude feed sample conditioning system must include a dual-stage switchable back-flushable sample fastloop system with a gasoil backflush for filter regeneration, a sample take-off after the de-salter, and a heat-exchange circuit to regulate the temperature of the crude feed sample before the required coalescing filtration to remove free water. The overall calibration modeling development strategy is also a major consideration.
An important aspect of the present project was that all calibration models were pre-developed through a compatible laboratory FT-NIR analyzer, and process samples were captured over a prolonged period of CDU operation. This also included crude feed samples. This approach offers many advantages — project startup times are cut down as candidate models are already available for corroboration, and the model development process is prolonged over a period so as to capture a representative range of the crude slate as well as the dynamics of CDU operation. Yet, this method does imply that care should be taken to reconcile the equivalence of on-line process samples at the process FT-NIR analyzer and also those captured and presented to the equivalent laboratory FT-NIR analyzer.
Results and Discussion
Shown below is the entire set of 467 calibrations samples for the six CDU rundown streams. Here, each Class (equivalent to stream type) is color-coded.
.jpg)
Composite data set for all CDU rundown stream samples—recorded at 8 cm-1 resolution and 2 mm pathlength. Image Credit: ABB Ltd.
Calibration models were created for all streams with the help of standard Partial Least Squares (PLS) methods via a standard commercial software package (Infometrix Pirouette, Seattle, WA USA). Before using for calibration, all spectral data were subjected to a simple spectral data pre-processing process — restricted to a fixed point baseline offset and an area normalization. No other procedures, for example, multiplicative scatter correction or orthogonal projection, were used or required.
.jpg)
Factor analysis (PCA) plot showing the separation of the different rundown streams in the modeling space. Image Credit: ABB Ltd.
Stream property calibration model data (rundowns)
Stream |
Property |
Units |
Model accuracy* |
Model range |
Number of samples |
Number of factors |
C5C6 |
D5% vol. |
°C |
0.2 |
38 to 43 |
76 |
6 |
D95% vol. |
°C |
0.5 |
65 to 72 |
76 |
3 |
FBP |
°C |
1.3 |
66 to 78 |
75 |
3 |
IBP |
°C |
0.6 |
30 to 38 |
76 |
5 |
Light Naphtha |
D5% vol |
°C |
0.8 |
75 to 85 |
72 |
5 |
D95% vol |
°C |
1.1 |
120 to 150 |
68 |
6 |
FBP |
°C |
2.5 |
135 to 170 |
60 |
6 |
IBP |
°C |
1.4 |
60 -to 75 |
66 |
6 |
Density |
g/l |
0.5 |
716 to 728 |
69 |
6 |
Heavy Naphtha |
D5% vol. |
°C |
1.3 |
108 -to 120 |
80 |
3 |
D95% vol. |
°C |
1.5 |
160 to 180 |
78 |
6 |
FBP |
°C |
2.2 |
168 to 186 |
74 |
7 |
IBP |
°C |
1.6 |
96 to 114 |
72 |
3 |
Kerosene |
D5% vol. |
°C |
0.6 |
175 to 200 |
74 |
5 |
D95% vol. |
°C |
1.2 |
220 to 255 |
74 |
6 |
FBP |
°C |
1.5 |
235 to 260 |
66 |
6 |
IBP |
°C |
1.8 |
160 to 185 |
70 |
4 |
Flash Point |
°C |
1.7 |
45 to 70 |
73 |
6 |
AGO |
D5% vol. |
°C |
1.8 |
240 to 255 |
73 |
4 |
E250 |
vol % |
0.6 |
4 to 10 |
70 |
5 |
E350 |
vol % |
1.1 |
82 to 97 |
69 |
6 |
FBP |
°C |
2.4 |
355 to 372 |
76 |
6 |
IBP |
°C |
3.6 |
200 to 215 |
68 |
7 |
Flash point |
°C |
1.8 |
70 to 82 |
76 |
5 |
Cloud point |
°C |
1.0 |
–4 to +4 |
75 |
6 |
HGO |
E350 |
vol % |
0.4 |
1.5 to 6.5 |
43 |
6 |
Flash point |
°C |
2.3 |
196 to 208 |
48 |
3 |
Density |
g/l |
0.4 |
892 to 906 |
78 |
4 |
Viscosity |
cSt |
0.5 |
18 to 35 |
70 |
5 |
*SECV at 1 Sigma
.jpg)
Example calibration plots for CDU rundown streams. Image Credit: ABB Ltd.
Here, it would be appropriate to make a few remarks on these data. First, it must be noted that the spectral difference among the data for any one side-draw stream is very low — even for the lighter streams, but increasingly the case for the heavier cuts. Higher molecular weight components make less use of near-infrared spectral absorbances; this places a very high premium on spectroscopic measurement stability and equivalence between analyzers, and thus makes FT-NIR as the only NIR technique that can reliably achieve stable calibrations for CDU applications.
An extra factor in the limited data difference is typical of CDU operation — the qualities of the side-draw stream do not differ too much, and again this places a premium on (low) measurement noise in order to achieve successful calibration models. For these data sets, the reported calibration model accuracies fall within or close to the ASTM reproducibility (R) of the standard laboratory technique used for producing the reference data.
On the whole, the predicted performance of an on-line FT-NIR analyzer when compared to the validation data produced by a standard technique is given by:
ASTM (R) > RMSEP > ASTM (r)
Where:
ASTM (R) = the reproducibility/accuracy of the ASTM laboratory reference method
ASTM (r) = the repeatability/precision of the method
RMSEP = the Root Mean Square Standard Error of Prediction of the FT-NIR analyzer calibration model versus the standard laboratory method
This claim bears some explanation. Calibration datasets for correlation-based techniques (for instance, PLS techniques using site laboratory reference property data and FT-NIR spectra) are, and should be, built up over a time period to maximize the variability in sample quality, to span as far as possible unexpected process variations, as well as to cover seasonal or other periodic difference in feedstocks. This implies that ASTM (r) — the short-term, single-operator repeatability of the laboratory technique) — will underestimate the lab-origin error in the dataset.
In effect, service or maintenance interventions may occur in the laboratory standard equipment over the time the calibration dataset is accumulated. Yet, ASTM (R) — the full inter-laboratory, multi-analyzer reproducibility of the laboratory technique) — may overestimate the local lab-origin error injected into the calibration dataset by the sample property reference values. Therefore, the possible outcome of the PLS/FT-NIR calibration exercise, with respect to calibration model accuracy, lies between the two.
On-line FT-NIR Analyzer Results and Data for Process Control
The advanced on-line process FT-NIR analyzer has an analysis time per stream below one minute per stream, when, as in the current case, operating with rapid TE-cooled NIR detectors, software-based selection of detector channel (without any electromechanical selection which would need a settling time delay) and the fast scan time possible when operating in the 1st overtone region (64 scans at a resolution of 8 cm-1). Data is in fact reported to the DCS through Modbus RTU (or TCP/IP) protocol with a stream update across all six rundown streams every 3 minutes.
This data-rate is actually slightly faster than expected or needed by any APC optimizer, and hence for long-term data, a moving average over a set of data points is more than sufficient.
Shown below are some instances of real-time trends obtained from the on-line FT-NIR analyzer data:
.jpg)
Percent evaporated points at 250 and 350 °C plotted for light gasoil (LGO). Image Credit: ABB Ltd.
.jpg)
Heavy gasoil (HGO) percent evolved at 350 °C over 18 hours vs cell temperature stability over same period. Image Credit: ABB Ltd.
Such measurements were important in realizing a good return-on-investment for the system, because it enabled considerably enhanced LGO/HGO cut-point control and avoided the loss of high-value product into residue. The following table shows the observed on-line FT-NIR analyzer precision (repeatability) per property per stream
On-line FT-NIR analyzer repeatability per stream per property
Stream |
Property |
C5C6 |
IBP (°C) |
5 vol% (°C) |
95 vol% (°C) |
FBP (°C) |
|
0.15 |
0.23 |
0.06 |
0.12 |
LN |
IBP (°C) |
5 vol% (°C) |
95 vol% (°C) |
FBP (°C) |
|
0.11 |
0.15 |
0.42 |
0.48 |
HN |
IBP (°C) |
5 vol% (°C) |
95 vol% (°C) |
FBP (°C) |
|
0.34 |
0.21 |
0.15 |
0.33 |
KERO |
Flash point (°C) |
IBP (°C) |
5 vol% (°C) |
95 vol% (°C) |
FBP (°C) |
|
0.77 |
0.46 |
0.42 |
0.89 |
0.74 |
AGO |
Flash point (°C) |
Cloud point (°C) |
IBP (°C) |
5 vol% (°C) |
E250 (vol%) |
E350 (vol%) |
FBP (°C) |
|
1.10 |
0.62 |
0.38 |
0.55 |
0.16 |
0.62 |
0.91 |
HGO |
Flash point (°C) |
Specific gravity (kg/m3) |
E350 (vol%) |
Viscosity (mm2/s) |
|
1.16 |
0.22 |
0.01 |
0.53 |
Conclusions
The above data show the measures taken at the time of the practical implementation of a project to commission a multi-property, multi-stream, on-line FT-NIR analyzer for process control of the CDU operation. The required spectral ranges of operation, fiber-optic types, detector types, and requirements for liquid sample flow cells and sample conditioning have been discussed in detail.
During the analysis of the performance of PLS calibration models developed off-line through a spectroscopically equivalent laboratory FT-NIR analyzer, the restricted spectral difference seen in characteristic CDU rundown streams was noted, and the demands this places on the precision and reproducibility of the FT-NIR analyzer was considered.
The results demonstrate that the FT-NIR analyzer is capable of providing real-time multi-property data on an appropriate timescale and with suitable repeatability to enable simple operation of the CDU advanced process control optimization.
References
- Nakamura, David, “Global Refining Capacity,” Oil and Gas Journal, Special Report, December, 2006, p56.
- Hou, K., Li, Y., Shen, J., Hu, S., “Crude Distillation Unit On-Line Optimization,” Hydrocarbon Processing, June, 2001.
- Friedman, Y. Z., “More About Inferential Models (editorial),” Hydrocarbon Processing, February, 2005.
- Chung, H., “Applications of NIR in Refineries—Important Issues to Address,” App. Spectrosc. Rev., Vol 42, 2007, p251-285.
- Nelson, Wilbur, L. “Nelson Complexity Index,” Oil and Gas Journal, September, 1976.
- Simpson, Michael, B., “Near-infrared Spectroscopy for Process Analytical Technology,” Process Analytical Technology, (Ed. Bakeev, K.), Blackwell Publishing, 2005.
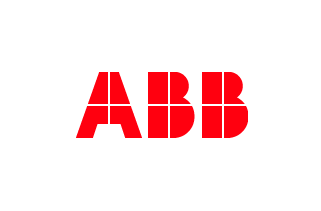
This information has been sourced, reviewed and adapted from materials provided by ABB Measurement & Analytics - Analytical Measurement Products.
For more information on this source, please visit ABB Measurement & Analytics - Analytical Measurement Products.