Today, both manufacturers and consumers alike find that fuel economy is a hot topic that warrants attention. In the automotive market, governments globally are implementing stricter fuel consumption standards for passenger cars and light trucks. For instance, in the United States, regulations around the Corporate Average Fuel Economy (CAFE) aim to achieve a fuel efficiency of 54.5 mpg for passenger vehicles by the year 2025.
.jpg)
In contrast, the latest reports from the U.S. Environmental Protection Agency (EPA) reveal that the current automotive fuel economy stands at 28.5 mpg, hence the need for innovation is real and extremely urgent. Similarly, the aerospace industry also harbors the goal of improving fuel efficiency. While the labor and other operating costs for U.S. passenger airlines continue to rise, the reduction in fuel costs can facilitate increasing profitability and stable competitiveness.
In order to meet the challenges and ever-increasing demands for cost savings, enhanced performance, and sustainability, automotive and aerospace manufacturers adopt a common practice called lightweighting. When the weight of cars and aircraft is decreased, less fuel is needed to move the transportation vehicle. Further, according to the U.S. Department of Energy Vehicle Technologies Office, “A 10% reduction in vehicle weight can result in a 6%-8% fuel economy improvement. Using lightweight components and high-efficiency engines enabled by advanced materials in one-quarter of the U.S. fleet could save more than 5 billion gallons of fuel annually by 2030.”
The aerospace industry has been a pioneer in this field and therefore has quite the head start. For instance, the 2009 Boeing 787 Dreamliner comprised of a 50% composite structure, whereas in 2013, the Airbus A350 was constructed using 53% composite materials, thereby improving the fuel economy.
The automotive industry is now following suit and ramping up its lightweighting efforts, as seen by the GMC 2019 Sierra’s advanced carbon fiber/thermoplastic composite truck bed or the considerably lighter 2015 Ford F-150, with its 700-pound-lighter aluminum frame. In fact, Ford took a big leap when it replaced steel with military-grade aluminum in its vehicle, but the risk paid off. The F-150’s sales skyrocketed post the release of the new lightweighted design, proving the logic behind alternative lightweighting materials.
In the end, manufacturers are on the hunt for materials that can satisfy requirements of both quality and performance, without adversely affecting the project deadline or budget. This article discusses three important lightweighting methods, as well as practical applications of lightweighting for the automotive and aerospace industries.
Three Methods For Lightweighting
General Plastics believes that lightweighting solutions can be successfully implemented using three different approaches. These techniques may be used individually or in conjunction with one another.
1. Use Lighter Materials for Each Component
The first approach is the most commonly understood meaning of the term “lightweighting” – simply using lighter materials. However, design engineers often only consider metals and alloys by default because of their higher strength. The following chart compares the strength and density of different automotive materials:
.png)
Tensile Strength and Density of Automotive Lightweighting Materials. Image Credit: Granta Design
Today, fortunately materials science has progressed so much so that there are other viable options in the composites world. Depending on requirements of strength, safety, and other requirements, there are a number of different, lighter-weight materials that can be considered for each component of cars and airplanes.
For instance, rather than using solid metal or plastic decorative parts in a vehicle, there are a number of components made out of high-density polyurethane foam that can be coated to look like the real thing. When multiplying a single lightweighting adjustment across an entire passenger jet, the weight reduction suddenly translates into pounds and the fuel reduction turns into profitability.
2. Use Fewer Components
The second lightweighting technique doesn’t merely involve a decrease in overall vehicle parts. If anything, owing to the advancements in technology, the number of electronic components in cars has only increased over time – such as for wireless communications, advanced driver-assistance systems (ADAS), and vehicle electrification – making it all the more imperative to ensure weight reduction to offset these additions.
Thus, if the possibility of reducing the number of components for a vehicle isn’t possible, consider choosing a lightweighting solution where the material itself can have fewer components.
Take, for example, honeycomb panels that are made from paper blends and composites, which are often a popular choice for lightweighting due to their high strength. However, since their core consists of a grid of large, open cells, the panels must be wrapped in multiple adhesive and skin layers to prevent the entry of water and dust. These films also need to be thick enough to create a smooth surface and prevent the transfer of the honeycomb pattern from being visible.
Materials like polyurethane foam can be produced using a closed-cell structure that is water-tight and therefore won’t rot, warp, bow, or delaminate from water intrusion. Moreover, the foam is equipped with self-skinning properties that automatically seals and is ready for painting or coating, thus achieving the appropriate appearance and texture. Naturally, the fewer manufacturing steps it takes to create a component, the greater the cost and time savings.
3. Use Processing with Less Waste
Concerns regarding environmental impact and sustainability often go hand-in-hand with considerations surrounding fuel economy. One needs to consider questions such as, how much waste is being produced to achieve a light truck or helicopter? With a few materials, such as wood or honeycomb panels, the structure is made by building up a block with the appropriate dimensions and then machining it down to the required shape. However, this method can involve a lot of wastage and excess. Depending on the lightweighting material chosen, it may be less wasteful and more cost-efficient to use other processing techniques. For instance, consider the following manufacturing methods used for high-density polyurethane foam:
- Custom molding: Instead of machining a sheet stock or block into the shape of the component, a custom tool is created to mold the part from a lightweighting material. This technique has the advantage of high levels of detail, complex shapes without machining, and smooth or textured skin as desired. Components can be further created with naked skins that are ready for further processing or paint-ready, or in-mold painting can be conducted for enhanced process efficiency.
- Thermoforming: This process involves drape or mold forming and is easy to use and ideal for shaping shallow slopes and angles where machining may prove to be more wasteful or time-consuming. Through thermoforming, parts that require large sheets of foam and complexity can be formed, in a matter of a few minutes.
- Sandwich panel layups: A technique that is commonly used in composite material production, this process uses standard vacuum bag layup or heated presses at temperatures above 275°. However, it is important to note that certain lightweighting materials like poly-ether imide (PEI), while possessing good strength properties, are not entirely suitable for processing under higher temperatures.
Regardless of the manufacturing method you choose, the end product still has the same weight and compressive strength. However, with the ideal solution, you are guaranteed less waste, with a reduced carbon footprint, using raw materials from recycled goods, and so on.
Real-World Lightweighting Applications
General Plastics offers a wide range of rigid and flexible polyurethane foams in a variety of densities, thermal properties, surfaces, and other characteristics to best fit your application needs.
Lightweighting Applications for Aerospace
For the aerospace sector, General Plastics offers the LAST-A-FOAM® FR-3800 FST foam and WSF-1121 impact energy absorption foam meeting the latest FAA and FDA requirements. The FR-3800 was specifically developed keeping in mind the FST and OSU 65/65/200 safety standards for flammability, smoke density, toxicity, and heat release.
Due to its unique physical properties such as density, strength, stiffness, and FST/OSU compliance, the FR-3800 is a core material that is a cost-effective alternative to honeycomb panels, poly-methyl chloride (PMI), poly-ether imide (PEI), and polyethersulfone (PESU).
What's more, the General Plastics’ build-to-print flight deck and passenger cabin molded parts are present in most areas of modern aircraft such as:
- Durable padding – used in heads-up display covers, headliners, post pads, kick strips and assist handle covers
- Aviation gap filler – that provides cushioning and noise reduction in overhead storage bins, passenger cabin dividers, galleys, and lavatories.
.png)
Explore an interactive 360° graphic to find out where polyurethane and foam core products are used in aircraft interior solutions.
Polyurethane foam is often easily used to substitute metal and plastic decorative items in aircraft cabins. For example, foam core covered with a brushed metal coating can replace the aluminum trim around seatback screens – thus decreasing the weight by more than 66% and the price by 33%.
To quote another example, an aerospace OEM customer discussed using polyurethane foam in place of heavier plastics for armrest extensions under the pad. Working with them every step of the way, General Plastics developed the optimal solution to meet their specifications. Owing to savings in cost, weight, and fuel economy, the OEM customer was extremely satisfied with the solution and decided to incorporate standardization on that lightweighting material for that component in their future projects.
Lightweighting Applications For Automotive
The automotive sector sees the use of polyurethane foams to replace thermoplastic elements in the vehicle, such as brackets holding different components in place in the dashboard and door panels. Since these elements are not structural in nature, replacing these functional parts with polyurethane foam does not compromise the safety of the entire dashboard or door panel.
General Plastics recommends the LAST-A-FOAM® FR-7100 Multi-Use Core Series because the variety of its available densities make it applicable nearly all throughout the vehicles, such as cores for load floors, seat backs and rigid support components, dashboard, door panels, visors, antenna housings, and headliners. Similarly, the General Plastics FP-8000 Energy Absorption Semi-Rigid Series is perfect for use in thin sheets for sound dampening in doors.
When it comes to thermoforming applications, the FR-4300 Thermoformable Board Series can be used in the manufacture of bucket seats and speaker boxes. Moreover, for custom molded parts, both the FR-3700 flame-retardant rigid polyurethane foam and WSF-1121 impact energy absorption foam can be used under thermoformed ABS plastic for pads on doors, armrests, consoles, and visors. Each of these foam series possesses unique enhancements and performance improvements to fit a variety of purposes, and can significantly reduce weight and costs in comparison to other materials.
.jpg)
Instead of solid plastic or metallic parts, consider using budget-friendly composite components that can make vehicles not only lighter but also just as strong. Image Credit: General Plastics
Push the Boundaries of Lightweighting
Whether it is aerospace or automotive markets, lightweighting is increasingly becoming all the more important to OEMs, Tier 1 and 2 suppliers, as well as manufacturers who want to create new products to meet the growing needs of the industry and new government standards. Lightweighting materials such as polyurethane foam provide weight reduction, as well as enhanced performance and overall cost savings.
Further, the use of these alternative materials is rarely a one-to-one drop-in replacement, due to differences in properties, processing, supply chain, etc. However, with the guidance of materials experts like General Plastics, the entire process from planning to design to manufacturing is made that much simpler and easier.
With over 80 years of experience working with manufacturers on complex, cutting-edge projects, General Plastics is equipped with both the expertise and extensive knowledge to help plan and coordinate your lightweighting objectives and solution. With a wide selection of innovative rigid and flexible polyurethane foam solutions, the team also offers complete in-house production services to deliver full assemblies and parts.
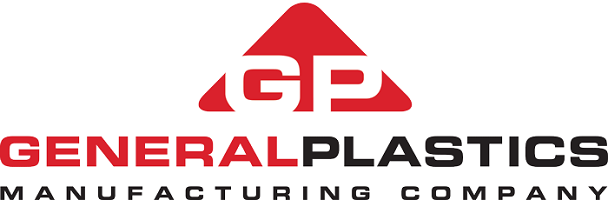
This information has been sourced, reviewed and adapted from materials provided by General Plastics Manufacturing.
For more information on this source, please visit General Plastics Manufacturing.