The latest generation of radars doesn’t consider condensate on the sensor as an issue. In fact, the VEGAPULS 64 is completely unaffected by condensation or buildup on the antenna, and thus accurately detects the liquid level. Equipped with best-in class, smallest antenna of its kind and exceptional focusing, the VEGAPULS 64 delivers outstanding performance – every single time. Simply world-class!
.jpg)
Image Credit: VEGA
Messy Conditions – So What?
The VEGAPULS 64’ antenna system is encapsulated in PTFE or PEEK, thus ensuring the absence of cavities or crevices in which the product can accumulate. The material’s surface is very finely processed with diamond tools, thereby also considerably reducing product adhesion.
.jpg)
Highly resistant encapsulated PTFE antenna for long service life in the chemical sectors. Image Credit: VEGA
.jpg)
Optimized signal processing makes VEGAPULS 64 independent of buildup.Image Credit: VEGA
What’s more, interference caused by buildup on the antenna system are filtered out by unique software algorithms. Moreover, signal attenuation caused by product deposits is largely compensated, owing to the high dynamic range of the sensor. Thus, the level is reliably detected even in cases of sensor contamination.
Key Benefits
- High measurement certainty, even in situations where product deposits collect during operation
- Level measurement that is independent of condensation and the quick availability of the system after cleaning cycles
- Non-contact level measurement, thus enabling maintenance-free operation
A Radar Beam Focused Like a Laser!
Good focusing delivers security
The newest cutting-edge technology from a world leader: the unrivaled focusing of VEGAPULS 64. This enables the radar beam to be targeted at the liquid surface with pinpoint accuracy, thus avoiding internal obstructions like heating coils and agitators.
This new generation of level sensors is also entirely unaffected by condensation or buildup and has the smallest antenna of its kind.
.jpg)
Image Credit: VEGA
Level in the Focus
VEGAPULS 64 has an operating transmission frequency of 80 GHz. With an antenna of 80 mm, this results in a beam angle of only 3°. The radar level sensor receives only definitive, distinct reflections from the product surface. This makes the level measurement more reliable and accurate.
.jpg)
Excellent signal focusing allows use even in confined spaces. Image Credit: VEGA
By comparison: a conventional radar level sensor with 26 GHz transmission frequency and an antenna of the same size has a beam angle of around 10°. As a result of the considerably wider signal beam, agitators, fittings or buildup on the vessel wall cause interference that can affect the measuring result.
.jpg)
A radar beam with 80 GHz only reflects from the product surface. A wider radar beam with 26 GHz also reflects from internal fixtures and agitators. Image Credit: VEGA
Key Benefits
- Considerably more straightforward setup and commissioning, even with complex vessel internals
- High accuracy, even when the level sensor is mounted close to the tank wall
- Increased measurement certainty over the entire measuring range through better focusing
The Ultimate for Small Tanks
Small process fittings extend the area of application for radar
Regarding contactless level measurement of liquids in small containers, smaller is better. With the smallest antenna of its kind, VEGAPULS 64 is simply the best! With excellent focusing and insensitivity to condensation or buildup, this new radar sensor is really exceptional.
.jpg)
Image Credit: VEGA
Small but Mighty
VEGAPULS 64 operates with a transmission frequency of 80 GHz. This corresponds to a factor of 3 compared to the technologies used until now. As a result, the antenna system and the process fitting can have correspondingly smaller dimensions.
.jpg)
Smallest antenna in the world, process fittings down to ¾" thread. Image Credit: VEGA
That makes radar level measurement technology more interesting for a wider range of applications. Existing vessels with small process fittings can be equipped with radar sensors without first carrying out expensive modifications.
.jpg)
With its compact design and process fittings down to ¾" thread, VEGAPULS 64 can be used very effectively on small tanks and containers. Image Credit: VEGA
Key Benefits
- Threaded, flange and hygienic fittings for widely different areas of industry
- Simple retrofitting of existing facilities, without modification
Applications
Thickener for Sugar Beet Juice
Level measurement in a thickener
Thickening of the thin juice extracted from sugar beet by the reduction of excess water in multiple stages at the evaporator station. This evaporation process involves the use of vacuum and heat. The evaporation process involves the liquid in the evaporator to boil so violently that great amounts of vapor are formed. Thus, a level sensor is required in the monitoring and control of the thickening process.
.jpg)
Image Credit: VEGA
Reliable
Accurate, reliable measurement, even under conditions of adverse vacuum and condensation
Cost effective
Reliable measured values that allow efficient control of the evaporation process
User friendly
Narrow beam angle for easier installation in vessel top
Ice Cream “Premix” Mixer
Level and pressure measurement during the mixing of ice cream ingredients
The ice cream ingredients are accurately weighed and fed accordingly into a mixing tank, where the "premix" is made. After this, the premix passes through the homogenizer at a pressure of around 140 bar, following which it is pasteurized at 80 °C. To achieve this, the level in the premix vessel and the pressure in the pipeline leading to the homogenizer need to be constantly monitored, to ensure the continuous production of ice cream.
.jpg)
Image Credit: VEGA
Reliable
Certified materials, as per FDA and EC 1935/2004 regulations
Cost effective
Short delivery time and standardized operation owing to plics® concept
User friendly
Simple installation due to small dimensions
Batch Filler Vessel
Level measurement in the batch filler vessel
The small batch filler vessels approximately 1 m high and 60 cm diameter alongside the production facility supply the filler heads of the tank. The products range from conserve to peanut butter to chocolate spread, with varying viscosity and temperatures.
The product density is also changing from each batch. The level system is needed to allow an optimal filling of jars.
Reliable
Measurement independent of density and viscosity
Cost effective
Accurate level measurement optimizes use of jars and medium
User friendly
Simple setup
.jpg)
Image Credit: VEGA
Process data
Measuring task
Level measurement
Measuring point
Vessel
Measuring range up to
1 m
Medium
Conserves and spreads
Process temperature
+10 ... +70 °C
Process pressure
0 … 0 bar
Special challenges
Changing product density, condensate, small vessel
Mixing Vessel
Level measurement in the mixing vessel
Mixing vessels are used for preparation, storage and transfer of a wide range of pharmaceutical products. These vessels are used for manufacturing antibiotics, injection and infusion solutions and blood plasma products.
After preparation, substances are transferred to a filling station. To guarantee a reliable process, the liquid level in the mixing vessel must be reliably and continuously monitored.
Reliable
Certified hygienic design (3A/EHEDG) and approved materials according to EC 1935/2004 and FDA
Cost effective
Continuous operation with absolute hygiene
User friendly
Standardized adjustment, process data storable and transferable
.jpg)
Image Credit: VEGA
Process data
Measuring task
Level measurement
Measuring point
Vessel
Measuring range up to
1.2 m
Medium
Antibiotics, injection and infusion solutions, blood plasma products
Process temperature
+50…+150 °C
Process pressure
-1…+6 bar
Special challenges
Changing product density, frequent cleaning cycles, small vessels
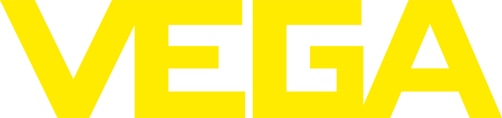
This information has been sourced, reviewed and adapted from materials provided by VEGA.
For more information on this source, please visit VEGA.