Ceramic and metallic high-temperature materials present a fundamental area of research within energy technology and mobility. Usually, the overall efficiency of aircraft or power plant turbines is dependent on their performance.
It is necessary for the materials to endure high mechanical and corrosive loading at high temperatures of more than 1000 °C. Meanwhile, it must be ensured that the density does not get too high, specifically during turbine construction, as the loading in the material is dependent on its own mass for rotating parts. ZwickRoell has launched a number of testing systems for materials testing at up to 2000 °C.
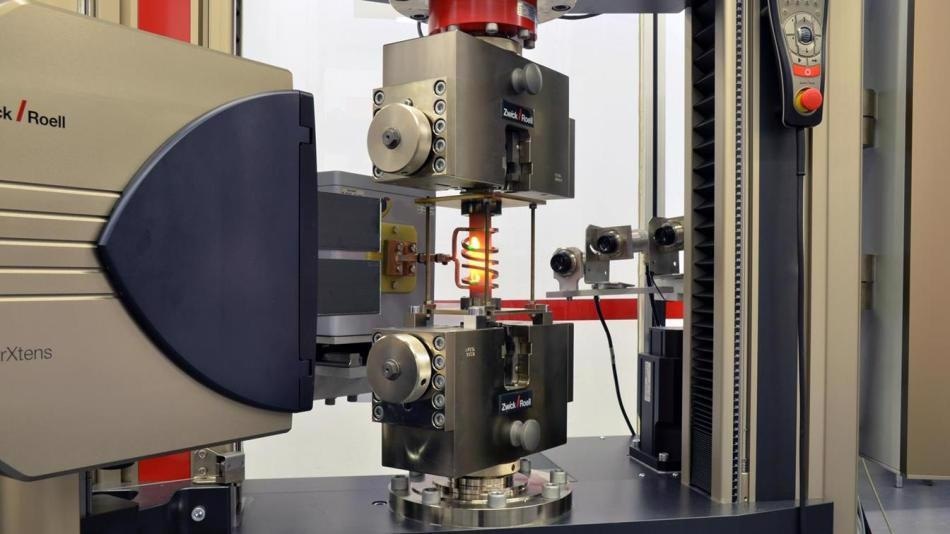
Successful conversion of energy not only needs a greater focus on regenerative energy sources, but it is also crucial to optimize traditional power plants by equipping them with the latest technology as well as implement novel energy policies for automotive technology.
In the case of energy conversion systems that involve single cycle operation (for example, combustion engines and gas or steam turbine power plants) and in multi-cycle systems (for example, steam and gas turbine combined power plants), higher thermal efficiencies and therefore lower CO2 emissions can be realized only by increasing the process pressures and temperatures. This is also applicable to aircraft turbines.
For technical implementation, it is essential to further develop the capability of existing ceramic and metallic materials, such as for combustion chambers, compressors, boilers, and turbines, on a continuous basis. Metallic materials increasingly undergo corrosive loading at higher temperatures due to the environment in which they are used.
Therefore, it is crucial to protect the materials from corrosion. One way to protect them is to form a passivation layer through the material itself. In the case of higher temperature range, the oxides of chromium (Cr2O3, up to roughly 900 °C), aluminum (Al2O3, up to roughly 1500 °C), and silicon (SiO2, up to roughly 1800 °C) are ideally suited for use as protective coatings.
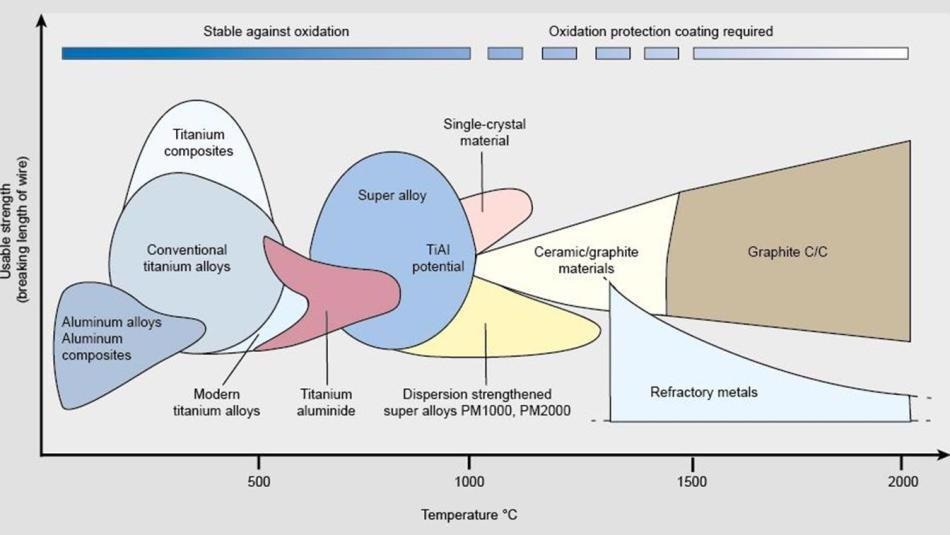
In order to ensure optimized material development, it is crucial to have in-depth knowledge of the correlations between microstructures, chemical compounding, and mechanical properties/long-term stability. On one hand, it is necessary to determine reliable material characteristics under practical loading (for example, creep, tensile loading, fatigue, and fracture mechanical behavior in application-relevant environmental conditions and also thermo-mechanical fatigue) to guarantee optimal utilization and hence economical use of these high-performance materials, which are usually expensive.
On the other hand, care must be taken to prepare models for durability forecasting under complex loading to prevent over-dimensioning and at the same time realize the best possible reliability in long-term operation.
Not only improved base materials but also thermal barrier coatings and metallic oxide protective coatings in combination with appropriate cooling methods can largely contribute toward increasing the process temperature. When new materials are developed, it is crucial to ensure that the compiled results are not just technically feasible but are also reliable and economically advantageous under long-term operation.
High-Temperature Tests for the Determination of Thermal-Mechanical Properties
High-temperature tests (for example, flexure and tensile tests) are employed to ascertain the heat resistance, thermal-elastic behavior, and re-crystallization temperature of materials. It is customary to set up the high-temperature unit (up to 2000 °C) directly in the materials testing machine. This arrangement enables tensile tests to be carried out at both room temperature to ISO 6892-1 or ASTM E8 and at higher temperatures to ISO 6892-2 or ASTM E21.
While performing tests at room temperature, components such as the high-temperature extensometer and the high-temperature furnace (1- or 3-zone furnaces) are simply swiveled out of the test area. Using a centrally divided hinged furnace enables the pull-rods in use to be inserted and withdrawn easily via a quick-change system. These ZwickRoell solutions feature optimal coordination of furnaces including temperature controllers, the correct specimen grips for tensile and flexure tests, and the appropriate extensometer.
With the laser Xtens (up to 1800 °C) and the videoXtens video extensometer (up to 1200 °C) based on the laser speckle principle, ZwickRoell offers two non-contact measuring solutions that are ideally suited for high-temperature tensile testing. These systems have clear advantages particularly when used with sensitive specimens and at high temperatures in the air and in a vacuum.
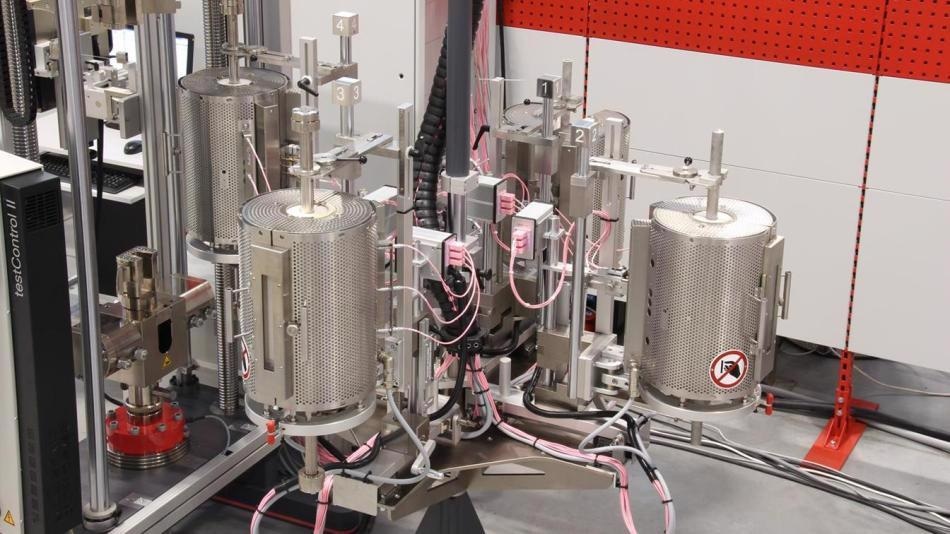
In general, the duration of tests is predetermined by the combination of the hold times and temperature tolerances specified in the standard, the volumes in the furnace, along with the heating and cooling times. Systems with up to six furnaces are available to reduce specimen throughput time.
Thermo-Mechanical Fatigue (TMF)
Besides reliability during long-term operation, it is essential for the aircraft and power plant turbines to exhibit adequate resistance against start-stop processes and short-term load changes. Thermo-mechanical fatigue (TMF) is the simulation of the mechanical load due to the thermal expansion of the material. When the turbines start operating, there is an increase in the temperature of all the components from room temperature to operating temperature, accompanied by an expansion of the material.
The expansion leads to the formation of stress in the material, which must be accurately determined to avoid component damage. In the case of composite components such as turbine blades with ceramic thermal barrier coatings, the thermal mismatch between ceramic and metallic components results in another loading component that should be taken into account during design. Moreover, adhesive oxide coatings have an impact on fatigue life during operation.
During thermo-mechanical fatigue test, a specimen is cyclically heated; a mechanical strain is superimposed by the materials testing machine in the same or inverse phase. To perform the TMF tests, induction heating systems are usually used as they have the ability to exhibit controlled and very quick heating and cooling phases.
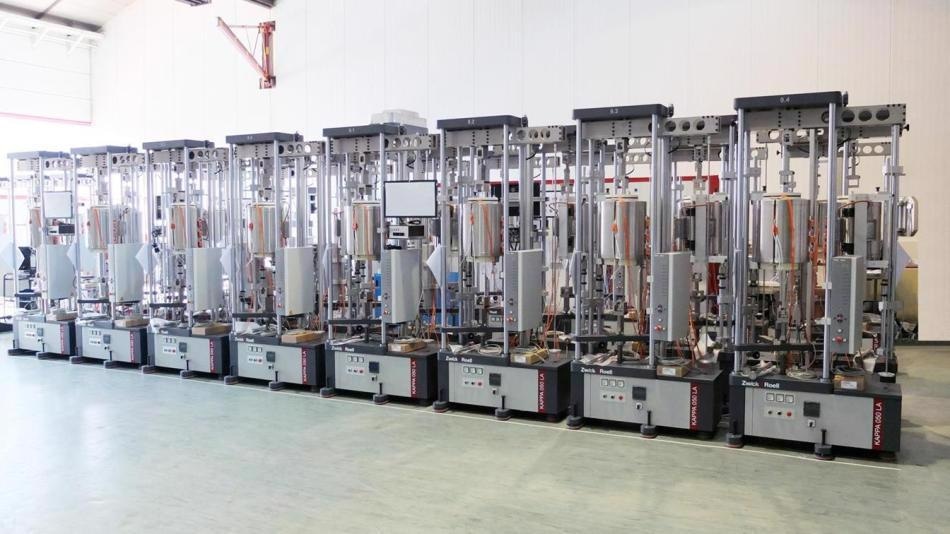
Determination of Creep Behavior
Apart from static-mechanical properties, the time-dependent deformation, failure, and damage behavior is highly crucial for the development of high-temperature materials. Besides temperature and mechanical loading, the surrounding environments in which the materials will be used also play a role in practical application due to probable superimposition from mechanical damage and corrosion. Therefore, stress relaxation tests and creep tests are carried out not only in the air but also under simulated operating environments.
Equipped with the videoXtens non-contact extensometer, the Kappa 50 SS-CF creep testing machine is best suited for these test methods. In addition to the aforementioned test methods, creep fatigue tests and tests for analyzing the tear growth and slow strain rate tests (SSRTs) can also be carried out up to temperatures of 1100 °C. It is quite normal for a single test to take even more than 10,000 hours before reaching any valid conclusions related to long-term behavior.
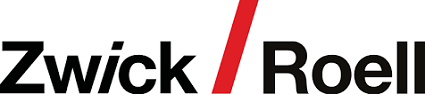
This information has been sourced, reviewed and adapted from materials provided by ZwickRoell GmbH Co. KG.
For more information on this source, please visit ZwickRoell GmbH Co. KG