The science of mixing different components to attain coveted properties or specification is called formulating. Often, the ingredients are not compatible, and they have to be mixed following a particular strict procedure to achieve a uniform and durable structure.
When formulating with natural ingredients, the task is even more demanding. The continual need to rethink existing formulations or create new ones requires thorough monitoring of formulation properties and the impact of multiple parameters on final formulation.
Formulations can contain more than 50 different ingredients and the fine adjustment of the compositions is the key to a perfect formulation. Throughout the formulation study, it is of high importance to also consider process, packaging and dispensing, storage conditions and usage conditions. The formula needs to be adapted to all these external parameters.
Formulation Characterization Steps
Whether you are formulating paints, food, cosmetics, electronic slurries, or pharmaceutical suspensions, there are four key steps to be considered for a full and complete characterization of your formula:
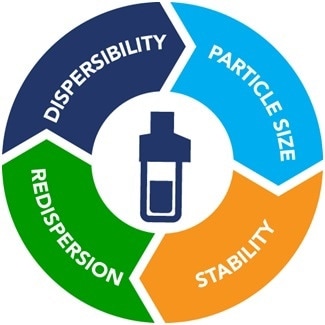
Dispersibility
The capability to “suspend particles” (either solid, liquid or gas) in the continuous phase in a way that enables them to preserve their original size and be distributed equally in the whole volume is known as dispersibility. It can be regarded as the foundation stone of the formulation process.
It is affected by:
- Stabilizer coverage of the interface
- Solvent affinity with the particles
- Preparation process: mixing tool used, time and speed of mixing
- Interactions between the continuous phase and stabilizer
- Interactions between the stabilizers and particles
A poor dispersibility will have a substantial impact on final product specification as the homogeneity and particle/droplet size will affect overall stability and so durability in time of colors for inks, polishing efficiency for CMP slurries, taste for flavored food emulsions, etc.
Monitoring the dispersibility will save time in decision making and formulation development. The dispersibility ratio (Dr) introduced by Formulaction is a useful parameter that allows to evaluate if the particle size in suspension corresponds to the so-called “primary particle” size.
Particle Size
When the particles are well dispersed, it is essential to be able to characterize their size. In order to understand the behavior of the particle in presence of other ingredients and upon the process utilized, recent studies show the importance of calculating the particle size in the real sample (i.e. without mechanical stress or dilution).
The capability to characterize the particle size without sample dilution is very important, particularly when working with nanoparticles where dilution can have a massive impact on the size (it can trigger agglomeration for example).
Shelf Life and Stability
Well dispersed particles within the size range required must remain in that state until use of the formulation. Therefore, stability is the next important parameter which should be considered.
So colloidal stability, with respect to predefined criteria, is the capacity od a dispersion to remain unchanged, over a predetermined time under conditions of use and storage. Many formed dispersions are thermodynamically unstable and over time, destabilization is to be expected.
There are a number of destabilization phenomena which have different origins. They can be classified in two main categories:
- Particle/droplet migration: sedimentation, demixion, creaming, phase separation
- Size growth: ostwald ripening, agglomeration-aggregation, coalescence
In terms of thermodynamics, except for microemulsions, a “stable” formulation does not exist. Nonetheless, a certain amount of destabilization (normally not observed visually) over a given period is accepted for emulsions. Therefore the need to quantify the magnitude of occurring phenomena.
This can be accomplished by using a Turbiscan Stability Index, which can quantify and rank formulations according to their destabilization at a particular time. This acceptable amount of variation and “period" is established depending on the formulations final application and can vary from a few minutes – for example inhaler or vaccines, up to several years – for example paints or cosmetics.
Redispersion
The “shake before use” strategy.
Destabilizations are inevitable but reversible for some applications. Injectable drugs, paints, and dairy drinks are just some examples of these formulations and are required to be shaken before use.
The following questions must be considered, and recommendations made to the user:
- Can the formulation retrieve its initial dispersion state?
- What method to use: stirring, shaking, mixing, ultrasound bath?
- Would the manual shaking be enough to well re-disperse the formulation?
- How long should it be shaken for?
After the sample redispersion is attained, the formulation is renewed and parameters like stability, size, and re-redispersion can be examined over and over. It is of huge interest to understand if the formulation can recover its original properties and state. How many of these “life cycles” the formulation can undertake before destabilization is irreversible.
Turbiscan: The Global Approach
For formulation characterization, Turbiscan® technology is the most complete tool: from particle size, dispersibility, stability quantifying and monitoring, through to the redispersion studies.
Particle size and dispersibility are measured with a single measurement (which takes less than 30 seconds), without sample preparation or dilution. Stability is characterized up to 200 times quicker than the naked eye and gives full understanding of the destabilization mechanism and stability ranking of the formulation.
- From concentration 0.001 up to 95% v/v
- From nm up to several hundred µm

This information has been sourced, reviewed and adapted from materials provided by Microtrac.
For more information on this source, please visit Microtrac.