Modern composites such as Kevlar can protect against knives and bullets, but high-speed rain impact can destroy these materials in minutes. The problem is that no material will survive rain impact at today’s flight speeds, although some materials are more resilient than others. The damage caused by rain erosion could easily turn into a serious and dangerous situation. The Rain Testing Rig This is where DERAs special rain rig testing facility, the only one in the UK and one of only four in the world, can help. The rain rig provides a unique service with the testing, analysis and evaluation of rain erosion. The rig offers the opportunity to test materials used for components before they are put into service and subjected to rapid deterioration, so avoiding costly repairs. Aircraft Areas Prone to Airborne Erosion It is now known that all forward-facing surfaces of aircraft and airborne stores, such as fuel tanks and munitions, are susceptible to impact erosion. Additionally, all materials fail at impact velocities over 100ms-1 - with the rate of erosion dependant on impact velocity and angle of impact. How the Rain Test Rig Works DERA (Defence Evaluation and Research Agency) began research into rain impact erosion in the 1950’s, employing methods such as rocket sleds and pouring water into a jet engine efflux. None of these methods were cost-effective so a whirling arm-type rig was created, in which a water jet impinging onto a spinning disc produced droplets. Testing is conducted on 25mm square samples, as whirling arms have limits on the mass and physical size of end fittings. The testing is carried out at impact velocities of up to 223ms-1, through a rain field of 25mm per hour. The predominant droplet diameter is 2mm, matching that of rain of this intensity. 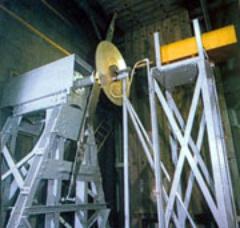 | Figure 1. The whirling arm rain test rig. | Rain Simulation Levels Twenty-five millimetres of rain in an hour is considered to be heavy. Any one location in the UK might only encounter a total of a few hours of rain at this level in a year. Therefore, testing of this sort is considered to be a worst case scenario - there are calibration tests to allow the facility to operate at lower intensities. Comparison to Practical Simulations As a comparison to the testing, a Javelin fighter was flown through the rain, with a range of material samples attached to an external pod. The rain characteristics were measured by the use of a device similar to a cine camera. This device ran a thin film of aluminium ribbon passed a gate and the rain left indentations on the ribbon. The damage to test samples compared well with those from real flight. How Water Droplets Cause Damage High-velocity water droplet impact can generate pressures of many tons per square inch on the sample surface. This pressure causes stresses, which can create cracking in brittle materials and deformation of more ductile materials. The outflow of the droplets then picks up on this damage and erodes the material. In the case of laminates, the interface of the layers can be subjected to shear stresses causing delamination. 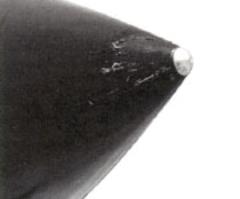 | Figure 2. Nose cone damage, similar to what would happen on other external pods and stores. | Summary Even modern metals such as titanium succumb to rain impact eventually. But by using rain rigs, rates of degradation can be measured and remedial action taken before materials fail. |