Increasing demand for more fuel-efficient and environmentally friendly road vehicles has focused interest on weight reduction and improved performance. Automotive applications of titanium follow logically from the high strength, low density, and in select applications, low modulus of titanium alloys, and their excellent resistance to corrosion and oxidation. Titanium has a long record of success in performance and racing cars. Applications include:
• Valve Springs
|
• Exhaust systems
|
• Valves
|
• Steering gear
|
• Valve retainers
|
• Suspension linkages
|
• Rocker arms
|
• Torsion bars
|
• Gudgeon (wrist) pins
|
• Suspension springs
|
• Cam belt wheels
|
• Wheels
|
• Connecting rods
|
• High strength fasteners
|
• Clutch discs, springs and housings
|
• Brake calliper pistons
|
• Gearbox housings
|
• Bumper supports
|
• Driveshafts
|
• Damage tolerant under panels
|
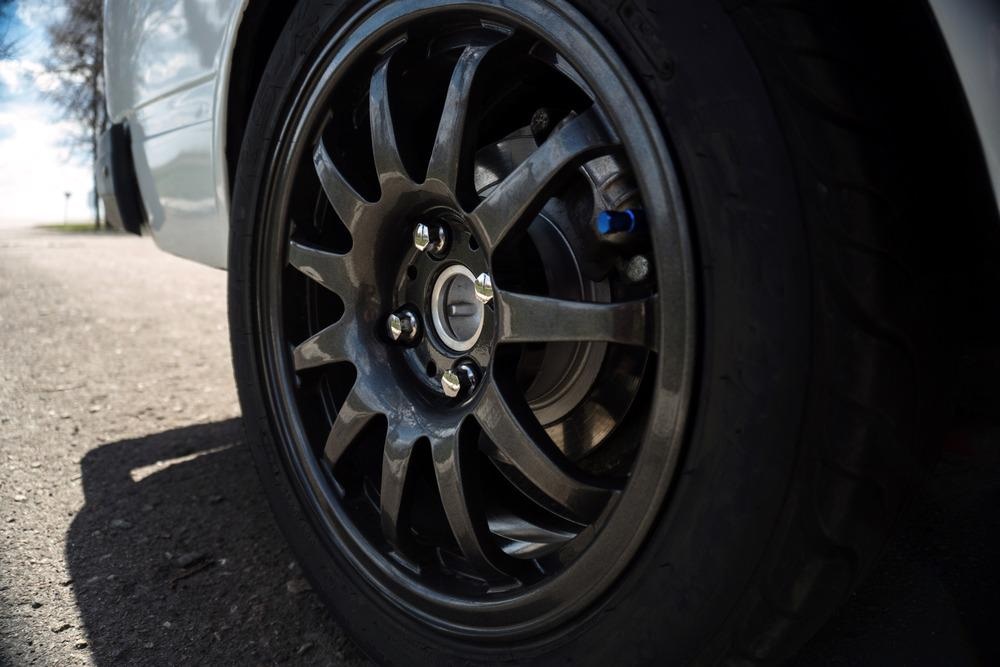
Image Credit: yuriy23/Shutterstock.com
Titanium and Weight Savings in Cars
Reducing the weight of motor vehicles, private cars, in particular, is just one aspect of the complex challenge which today’s automotive designers are facing. Making cars smaller, - an apparently obvious strategy creates problems in providing acceptable free space inside the vehicle for passengers and their effects. Small, lighter-weight cars are unlikely to satisfy the aspirations of every owner or driver. Weight reduction in this class of car, - without compromise to space, contributes to the reduction of fuel consumption, and the 'green' image of the manufacturer. Cost represents a particular challenge for fundamentally more expensive materials such as titanium. A recent check in the US and Europe suggests the following levels of cost are affordable for weight saving.
Table 1. Cost savings brought about by weight reductions in cars.
|
Mass production
|
£1.50 - £2.00
|
$1.00 - $1.33
|
CAFE *limited
|
£3.00 – £15.00
|
$2.00 - $10.00
|
Specialty and Luxury
|
£5.50 plus
|
$3.66 plus
|
* CAFE = Corporate Average Fuel Economy (USA)
Design Concepts
Overall, a vehicle weight reduction of 1% is claimed to give a reduction in fuel consumption of some 0.7%. Weight reduction in the moving parts of the engine are however likely to be much more effective in achieving improved fuel economy than bodyweight reduction. Titanium alloy density is some 60% that of steel, and the elastic modulus is about half that of steel. Direct substitution of steel parts with titanium is rarely the best way to proceed, but in practice should produce an immediate weight reduction of at least 40%. The low modulus of titanium is beneficial for springs, but component redesign may be necessary for stiffness limited applications. Specific strength, and likewise specific toughness and fatigue limits of titanium compare very favorably to both steel and aluminum alloys.
Table 2. Comparison of specific strength of engineering alloys
|
CP Titanium
|
4.51
|
105
|
250 – 450
|
50 - 100
|
Ti-6Al-4V
|
4.43
|
112
|
900 – 1100
|
200 - 250
|
Ti - LCB?
|
4.79
|
110
|
950 – 1400
|
200 - 290
|
Carbon Steel
|
7.8
|
200
|
350 – 450
|
45 - 60
|
Aluminium Alloy
|
2.8
|
70
|
100 – 350
|
35 - 125
|
Springs
Uniquely among engineering alloys, titanium possesses the strength, density, and modulus to make the ‘ideal’ spring for almost every application. The key to successful spring design is to optimize the saving of weight and space. Correctly designed titanium springs can be typically three quarters the height and 60 - 70% lighter than steel equivalents. The aerospace industry has long used titanium alloy springs in a wide range of applications.
How does titanium permit such competitive spring designs? Two equations govern the weight and the deflection under a load of coil compression springs. In the first equation for spring weight, the load L and the spring rate R are fixed by the designer for the application, the low shear modulus and low density of titanium are in the numerator of the equation, and high allowable stress in the denominator. Weight is therefore minimized when titanium is used. In the second equation, the low shear modulus of titanium is in the denominator, thus deflection is increased. As a consequence the number of active coils may be reduced, this, in turn, permitting a reduction of the free height of the spring (50- 80% that of a comparable steel spring), with further weight reduction, and a higher natural frequency.
Equation 1
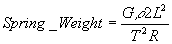
where G = Shear Modulus
ρ = Density
T = Allowable Stress
L = Load
R = Spring rate
Equation 2
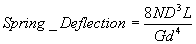
where N = Number of coils
D = diameter of coils
d = diameter of wire
Spring Manufacture
Titanium springs can be produced by hot or cold coiling and should be finished by shot peening, typically to .16 - .18A intensity. Beta alloys such as Beta-Ctm , LCB (Low Cost Beta), as a class offer designers many options to select a final combination of properties for specific applications e.g. as valve or suspension springs. Consultation with the alloy producer and the spring manufacturer is recommended in order that the appropriate method of manufacture and finishing is used.
|