
Image Credit: Andrey Armyagov/Shutterstock
Refractory metal alloys are known for their distinctive specifications and general properties. Among them is the niobium-based refractory metal alloy C-103, which has a variety of applications in space exploration and propulsion technologies.
Though elements such as molybdenum, tantalum, tungsten, niobium, and rhenium are the more well-known refractory metals, this category can be expanded to include up to 16 metallic elements.1,2,3,4
Refractory metals all have some core properties in common. These include exceptional resistance to corrosion, high thermal conductivity and melting points, as well as the retention of mechanical strength at high temperatures (hot strength).
Given the durable and hard-wearing properties of refractory elements, they have been the subject of research for applications in a wide range of fields. These include nuclear power, aerospace applications, drilling, metal cutting, chemical processing and electronics.
To augment these properties, combinations of refractory metals and other components, known as refractory metal alloys, have been developed.
For example, steel is usually formed from a combination of iron and carbon; but steel possesses greater strength than either element individually. These properties are shared by refractory metal alloys, which are formed by alloying tungsten, niobium, molybdenum, tantalum and/or rhenium with other elements.
Refractory metal alloys are an important industry resource, as they can be utilized in a wide range of applications, including corrosion-resistant coatings and parts and load-bearing components.
Refractory Alloys in Aerospace
To build devices that can fly through Earth’s atmosphere or even travel into space requires materials capable of withstanding changes in temperature and mechanical load that can happen quickly over a wide range of measurements.5
Though composite materials and ceramics with these capabilities have been developed, designers regularly discover that these materials are not easily fabricated into the complicated forms required for aerospace applications.6
When compared to composite materials and ceramics, refractory metal alloys have been found to offer an alternative approach. Not only are they somewhat easier to work with, they still provide the desired high temperature- and load-bearing characteristics.
Tungsten, tantalum, molybdenum and niobium have each found applications in the aerospace industry because of their shared refractory metal properties, including high melting points and high temperature strength.6
Niobium has the lowest density of all the refractory metals, being close to the density of nickel while displaying good thermal conductivity. Niobium is also easier to work with than most other refractory metals.
This is attributed to its weldability, as well as its high room-temperature ductility and low ductile-to-brittle transition temperature.
The C-103 alloy is one of the niobium-based refractory metals that researchers have been investigating in their efforts to create refractory metal alloys with the ideal mix of properties needed in aerospace applications.
C-103 displays an encouraging mix of fabrication characteristics and elevated temperature strength.
C-103: A Lightweight, High Temperature and High Strength Alloy
A complex alloy, C-103 is niobium-based, with additions of 1 wt% titanium, 10 wt% hafnium and trace amounts of other elements.7 Though it is a highly-researched material, C-103 is still the subject of much investigation and is constantly at the center of new applications.
Its exceptional mechanical stability and strength across huge temperature ranges have seen C-103 being used in aerospace applications since almost the beginning of the space age.8
The C-103 alloy has long been used in aerospace applications in the 1100-1500 °C temperature range due to its superior stability and strength. This stability and strength can be maintained from cryogenic temperatures up to 1482 °C, while at room temperature, its yield strength is 341 MPa. This decreases to only 65 MPa at 1200 °C.6,7
Unlike other refractory metal alloys, refractory ceramics, or composites developed for aerospace, the C-103 metal alloy is comparatively easy to form.
Despite its high melting temperature, C-103 can be processed via conventional thermomechanical and melting processes. This allows C-103 to be formed into a range of complex shapes and can be TIG welded without any significant loss in either machinability or ductility.
These characteristics make the C-103 metal alloy well-suited to a variety of aerospace applications, for example, rocket engine nozzles, aircraft gas turbines and high temperature valves, while its formability and high temperature performance have seen C-103 put to use in jet engine afterburner liners.
The C-103 metal alloy is now being studied for applications in next-generation aerospace technologies such as thrust augmenter flaps and heat pipes for dissipating heat from hypersonic nose cones and leading edges.
Refractory metals and metal alloys such as C-103 are suitable for use in a wide range of industries, and these are available in sheet rod, bar and plate forms from H.C. Starck Solutions.
Metal alloys including MHC (Mo-1.2Hf-0.1C) and TZM (Mo-0.5Ti-0.1Zr) are available, while custom alloys can be provided on request.
H.C. Starck Solutions has decades of experience in alloys, meaning it can offer customers a thorough fabrication service when manufacturing complex parts from refractory metal alloys.
Refractory alloys and refractory metals are also offered in spherical and irregular powders with precise and narrow size distributions for use in additive manufacturing powder metallurgy applications.
The latest developments in additive manufacturing mean that complicated components can be more easily produced in a wide range of refractory metals.
In additive manufacturing, this characteristic also offers economic advantages.
Refractory metals and refractory alloys are expensive materials, but as components are manufactured using only the precise amount of material required, cost-effectiveness is assured, as there is less waste from the machining process.
Previously, manufacturing refractory metal alloys into useful shapes was an exceptionally challenging process, but these can now be readily formed in additive manufacturing, as traditional thermomechanical processing is no longer required.
References
- Bauccio, M. ASM Metals Reference Book, 3rd Edition. (ASM International, 1993).
- Snead, L. L., Hoelzer, D. T., Rieth, M. & Nemith, A. A. N. Refractory Alloys: Vanadium, Niobium, Molybdenum, Tungsten. in Structural Alloys for Nuclear Energy Applications 585–640 (Elsevier, 2019). doi:10.1016/B978-0-12-397046-6.00013-7.
- Harvell, M. B. What are Refractory Metals. https://www.pickpm.com/wp-content/uploads/2016/08/What-Are-Refractory-Metals.pdf.
- International Journal of Refractory Metals and Hard Materials.
- Zhang, S. & Zhao, D. Aerospace Materials Handbook. (CRC Press, 2012).
- Satya Prasad, V. V., Baligidad, R. G. & Gokhale, A. A. Niobium and Other High Temperature Refractory Metals for Aerospace Applications. in Aerospace Materials and Material Technologies (eds. Prasad, N. E. & Wanhill, R. J. H.) 267–288 (Springer Singapore, 2017). doi:10.1007/978-981-10-2134-3_12.
- Panwar, S. S., Prasad, K., Umasankar Patro, T., Balasubramanian, K. & Venkataraman, B. On the occurrence of dynamic strain aging in C-103 Nb based alloy. Materials Science and Engineering: A 620, 286–292 (2015).
- C-103 Nb Alloy: Properties & Applications. H.C. Starck Solutions https://www.hcstarcksolutions.com/ (2020).
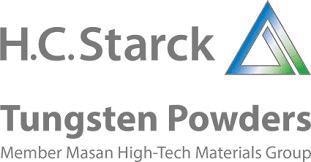
This information has been sourced, reviewed and adapted from materials provided by H.C. Starck Inc.
For more information on this source, please visit H.C. Starck Inc.