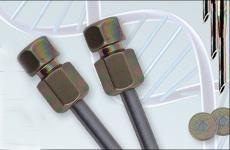
The corrosion resistance of Dursan® was tested in TFA, a common ion pairing agent in the analysis of peptides and small proteins in HPLC testing. Is Dursan resistant to TFA in HPLC testing applications? This article discusses the results.
Trifluoroacetic acid (TFA) is a structural analog of acetic acid where all three of the acetyl hydrogens are replaced by fluorine atoms. This is seen in Figure 1.
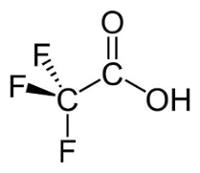
TFA is a much stronger acid than acetic acid because of fluorine’s electron withdrawing nature which weakens the oxygen-hydrogen bond. It is most often used in low concentrations as an ion pairing agent in liquid chromatography to analyze peptides and small proteins. Dursan can be used in liquid chromatography environments to provide an inert coating to the surface of stainless-steel components e.g. columns, tubing, pumps and frits. This article will explore the compatibility between Dursan and TFA and ideas for solving HPLC test problems.
This article will discuss:
- Corrosion rate of Dursan when exposed to TFA solution
- The compatibility of Dursan and TFA
- Application of Dursan in HPLC
- Stiction of TFA to Dursan vs. stainless steel
The Test
The standard Dursan® coating was used to coat corrosion coupons. They were subjected to an immersion test, specified by ASTM G31 methodology. TFA is most commonly used in protein analysis at concentrations of »0.1% however, the foremost concern for the Dursan coating is corrosion and this is typically accelerated at higher concentrations. Therefore, coupons were exposed to 1% and 2% TF solutions for 30 days at room temperature. Coupon mass, water contact angle and film thickness were monitored before and after the 30-day exposure.
Thickness was measured on 5 points of each coupon before and after the 30 day exposure and results are summarized in Table 1 and show no appreciable loss of the Dursan coating due to TFA exposure. Figure 2 shows a before and after picture of one of the coupons exposed to the 2% TFA solution and there is no change in appearance.
The slight change in thickness is due to not measuring the exact same spot on the coupon before and after exposure. With the slight variation in film thickness that happens naturally as a result of the deposition conditions, the values appear to change. However, these changes are all within the error of the measurement.
Table 1: Comparative thickness of a Dursan coated coupon before and after a 30 day exposure to TFA.
TFA concentration |
Average thickness before exposure |
Average thickness after exposure |
1% |
1135 ± 28 nm |
1129 ± 29 nm |
2% |
1128 ± 25 nm |
1139 ± 30 nm |
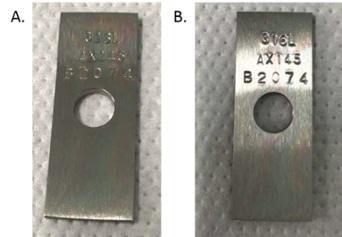
Figure 2: Dursan coated corrosion coupon before (A) and after (B) exposure to 2% TFA for 30 days. There is no visual difference in the appearance of the coupon.
Contact Angle Measurement
Contact angle was monitored to investigate the surface chemistry before and after exposure to TFA. The Dursan coupon had a water contact angle of ~90° before exposure which is typical for Dursan. After the 30 day exposure, the water contact angle decreased to ~55° in both the 1% and the 2% TFA. This is similar to what happens when the coating is exposed to a bleach solution for 30 minutes.
Despite this change in contact angle, the Dursan surface still shows remarkable anti-fouling properties for proteins. The bare stainless steel coupon started with a contact angle of ~35° and ended up with a contact angle of ~110° after exposure to TFA, a DI water rinse, 30 minute sonication in DI water, and being dried at 230 °C. This suggests that the TFA sticks to the bare stainless steel readily and is hard to remove.
This is a well-documented problem with TFA in PHLC applications. The Dursan coupons (which saw the same post exposure conditions) show that TFA does not adhere well to the surface. This is an added benefit when using Dursan coated HPLC components for protein and peptide analysis. Want to know more about how Dursan can improve HPLC test results?
Dursan Use in HPLC
Dursan® can be applied to most stainless steel PHLC flow path surfaces which improves corrosion resistance in inertness of HPLC systems.
Apply Dursan to:
- Valves and fittings
- Needles
- Stainless steel tubing
- Columns
- Ampules and vials
- Glassware
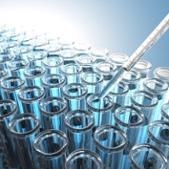
Conclusion
In conclusion, TFA does not pose a risk to Dursan coated parts. There is no change in thickness of the coating and no corrosion to the underlying substrate (in this case 316L stainless steel) during 30 day exposure to 1-2% TFA solutions at room temperature.
The contact angle of the coating does change to become more hydrophilic but previous studies have shown that this has very little/no effect on the anti-fouling properties for protein analysis. Additionally, the Dursan coating appears not to allow the TFA to stick to the surface of the coupon, where a bare coupon shows evidence of TFA stuck to the solution even after rinsing and sonication of the coupon.
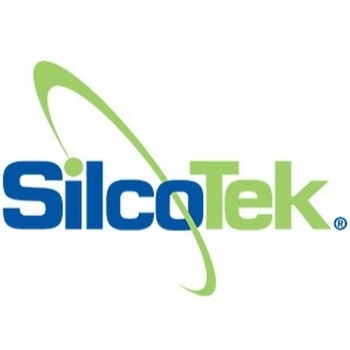
This information has been sourced, reviewed and adapted from materials provided by SilcoTek.
For more information on this source, please visit SilcoTek.