Metallic fine powders and granular materials are extensively used in several industries such as sintering, 3D printing, alloys, and so on. The physics of powders should be accurately analyzed to control and optimize processing techniques. This article demonstrates user cases and concrete examples concerning the selection of powders and optimization of processes for additive manufacturing (AM).
Company Presentation
GranuTools enhances powder understanding by offering cutting-edge physical characterization tools. Integrating years of experience in scientific instrumentation with fundamental studies on powder characterization, GranuTools provides a special set of complementary instruments.
A Set of Complementary Tools
Named after their purpose, GranuTools’ instruments are tools for understanding the powders’ macroscopic behavior — GranuFlow is an automatic funnel flow meter, GranuCharge is a triboelectric charger, GranuPack is a high-resolution tapped density meter, and GranuDrum is a dynamic angle of repose analyzer.
Powder Properties
The quality of the powders employed in additive manufacturing is extremely important as these powders will affect the physical properties of the end product. Furthermore, advancements in the quality of the powders used will help in increasing the number of products that can be made and also aid in saving money.
For this reason, powder quality evaluation is a vital question for the AM process. To address this query, properties such as flowability, spreadability, and compaction dynamic of powders must be examined.
Powder Bed Fusion (PBF)
Figure 1 illustrates a schematic diagram of a typical laser PBF machine. The metallic powder is stored in a hopper and gradually exposed by a rising piston to the recoater. This component can either be a blade or a roller that disperses the exposed powder across the bed. Generation of a thin and uniform layer is the main objective of this operation. The remaining powder is captured in a secondary container for recycling/re-use. To build a component layer-by-layer, the same cycle of spreading and melting is repeated for a number of times.
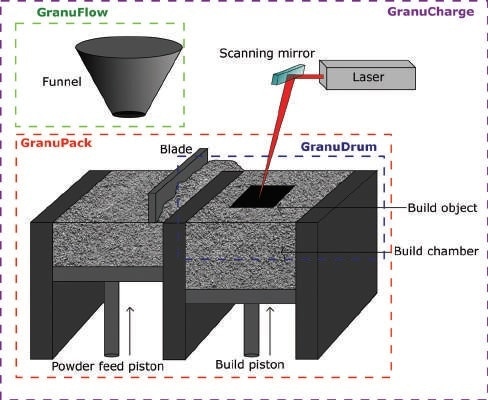
Figure 1. Schematic diagram of a PBF process.
In SLM (selective laser melting), EBM (electron beam melting), and SLS (selective laser sintering) methods, consecutive thin layers of powder are produced with a rotating cylinder or with a ruler. Each layer is partly sintered or melted with an energy beam (electron or laser beam). The vertical resolution is defined by the layer thickness. Therefore, a thin layer brings about a better resolution. The powder should be as fine as possible for obtaining a thin layer.
Unfortunately, the cohesiveness increases and the flowability decreases when the grain size decreases. The powder also becomes increasingly sensitive to moisture. Therefore, a tradeoff between flowability and grain size has to be found. The quality of the components made with AM is directly related to the flowing properties of the powder. The flowability must be satisfactory to obtain homogenous consecutive powder layers.
For all the processing techniques dealing with powder, the measurement technique used for characterizing the powder should be as close as possible to the process. Particularly, the flow field and the stress state of the powder must be similar in the process and in the measurement cell.
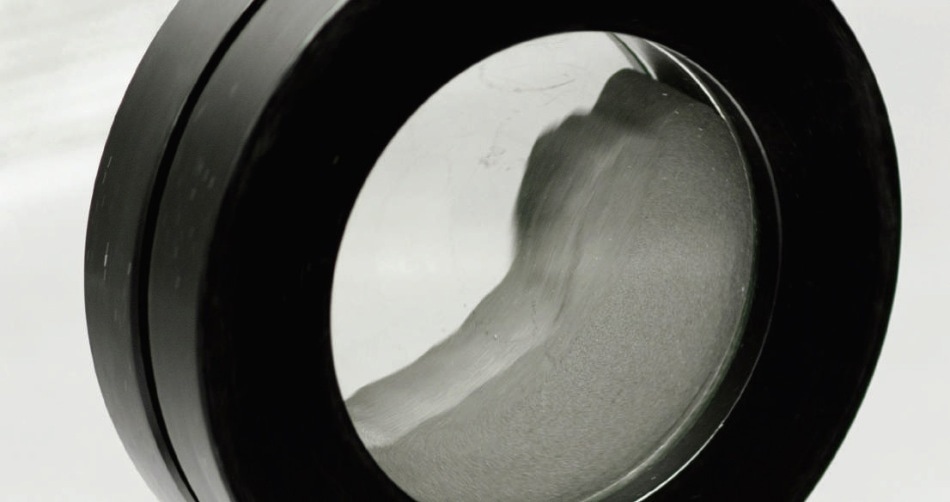
A range of new publications have demonstrated that the classical flow meters are not capable of providing relevant information about powder spreadability in powder-bed-based additive manufacturing.
In classical rheometers and shear cell testers, the existence of a compressive load is not compatible with the free surface flow used in AM devices.
On the other hand, the measurement technique based on the rotating drum can serve this purpose because the powder flow is accurately analyzed (2.2%) at the powder/air interface without any compressive load.
The rotating drum geometry also makes it possible to examine the relevant powders properties for AM, specifically the spreadability of powders. GranuTools have demonstrated recently that the probability to obtain waves at the time of layer formation is proportional to the Cohesive Index measured by the GranuDrum instrument [1]. Furthermore, GranuDrum can also estimate the optimal ruler speed to achieve a homogenous layer.
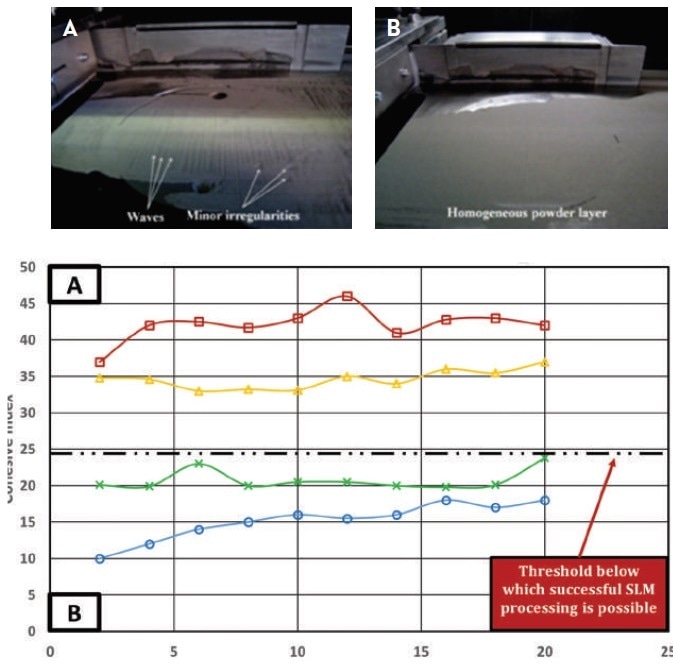
Figure 2. Evolution of the Cohesive index versus drum rotating speed for TiNb, TNZ, NiTi and Ref-Ti titanium powders (adapted from Yabokova et al., 2015).
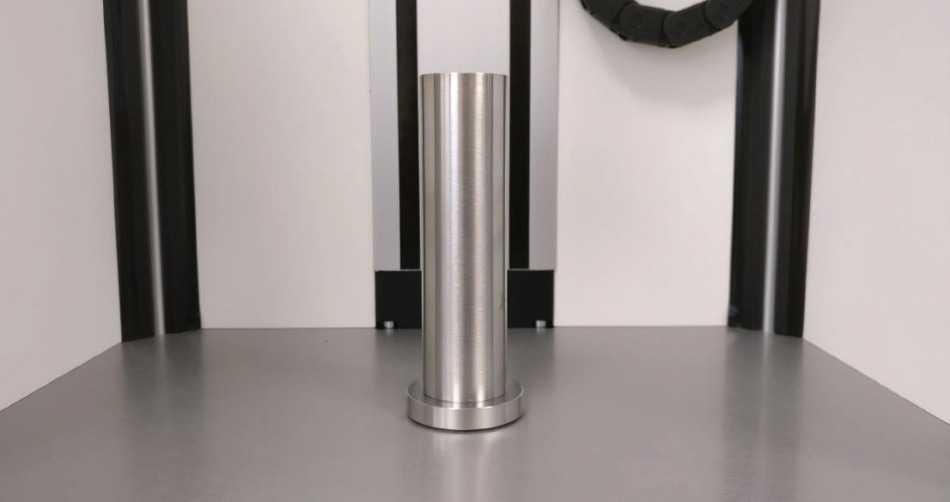
Apart from the spreadability and flowability, the powder packing fraction is another main parameter. Indeed, the porosity of the produced part is reduced by a high packing fraction. Thus, an exact measurement of the range of packing fractions accessible by the powder is also required as precursors quality control with batch-to-batch differentiation.
The GranuPack instrument determines a compaction curve (density plotted as a function of the tap number) with excellent precision of 0.4% [2]. The precision arises from the use of an initialization protocol and from the measurement automation (operator independence). From this compaction curve, the speed, optimal density, compaction range, and bulk density are extracted. Furthermore, the compaction curves of different samples can be compared to show the differences related to both flowability and density.
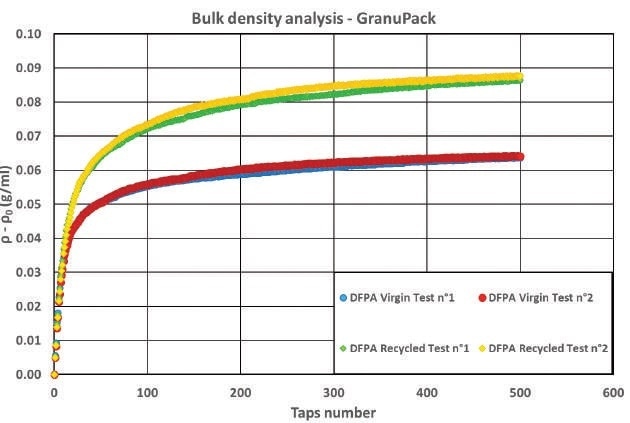
Figure 3. Bulk density variation for a Duraform Polyamide 12 virgin and recycled powder (after a SLS process). GranuPack can make differentiation between the two powders.
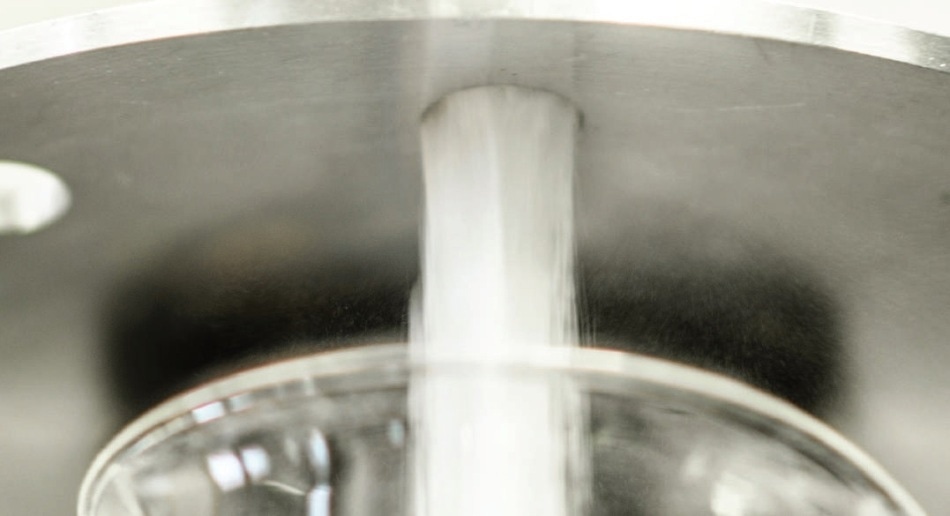
The funnel or silo configuration is a common approach for powder feeding. Thus, the flowability of a product must be perfectly understood. Conversely, nowadays, basic flow meters only provide information for one aperture diameter, typically 2.5 mm. The GranuFlow was developed to fill the gap in terms of the powder flow rate measurements.
This instrument is a simple powder flowability measurement device composed of a silo with diverse apertures linked to a dedicated electronic balance to measure the flow rate of powders.
This parameter is automatically calculated from the slope of the mass temporal evolution determined with the balance. The aperture size is changed easily and rapidly with an original rotating system. As a result, the flowability in a die filling configuration can be easily obtained with a high precision of 1%.
Software assists the measurement and the result analysis. The flow rate is measured for different aperture sizes to obtain a flow curve. At last, the whole flow curve is fitted with the minimum aperture size to obtain a flow (Dmin) and with the well-known Beverloo theoretical model to obtain a flowability index (Cb, related to the powder flowability). The entire measurement is carried out rapidly, accurately, and easily.
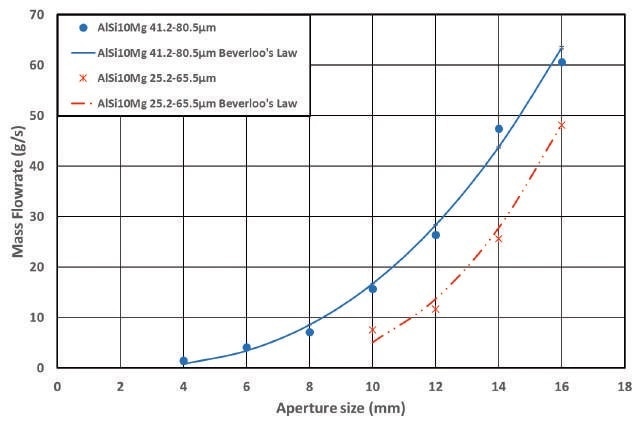
Figure 4. Mass flow rate versus aperture size for AlSi10Mg powders with two different Particles Size Distributions (25.2-65.5 m and 41.2-80.5 m).
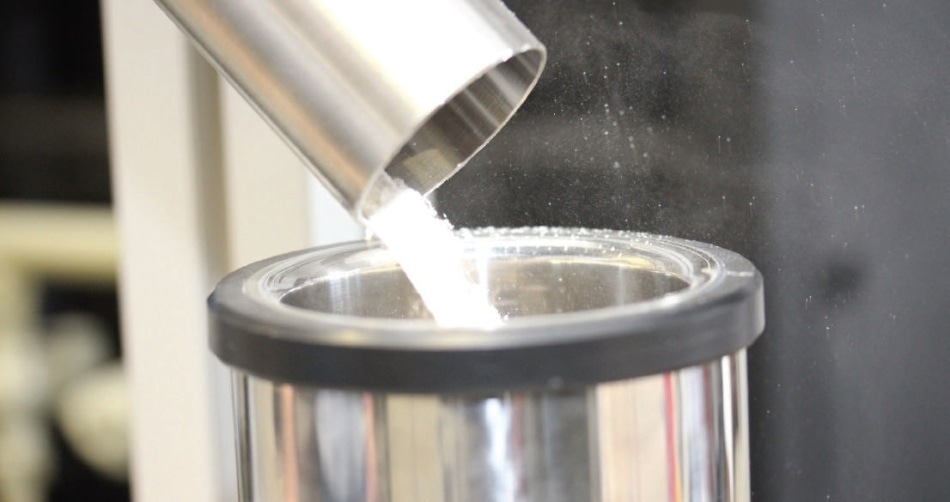
GranuCharge measures the potential of powder to produce electrostatic charges during a flow in contact with a chosen material. The presence of electric charges in a powder induces cohesive forces, resulting in the formation of agglomerates. Therefore, GranuCharge is capable of predicting the flowability deterioration during processing, for instance during the layer formation in additive manufacturing. Furthermore, the outcome of a GranuCharge measurement is extremely sensitive to grains surface state (contaminants, oxidation, and roughness). Subsequently, the aging of a recycling powder can be measured with an accuracy of 4%.
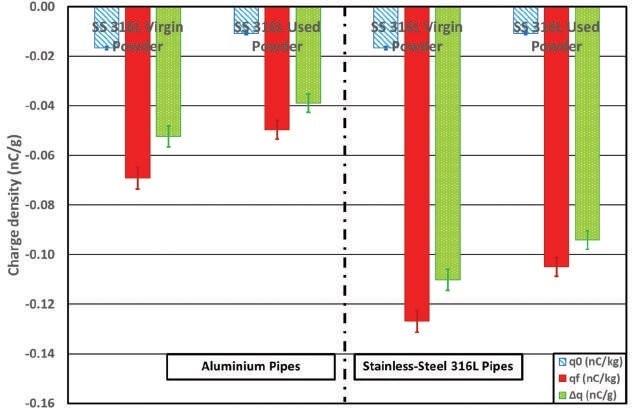
Figure 5. Charge density of a Virgin and Recycled (after only one SLM process) Stainless-Steel 316L powder in contact with different pipe materials (SS 316L and Aluminium). The aging is perfectly highlighted.
Workflow for Process Optimization
Granutools takes pride in introducing the revolutionary workflow for the process optimization of 3D printing. The workflow is important for 3D printer manufacturers, powder companies, and parts producers.
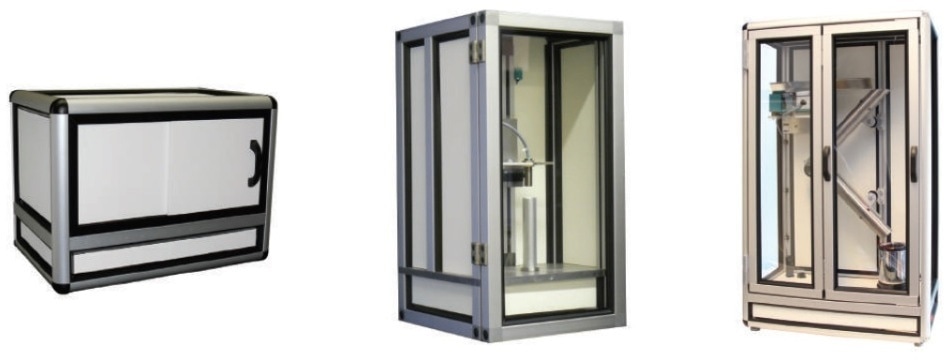
WORKFLOW = GRANUDRUM + GRANUPACK + GRANUCHARGE
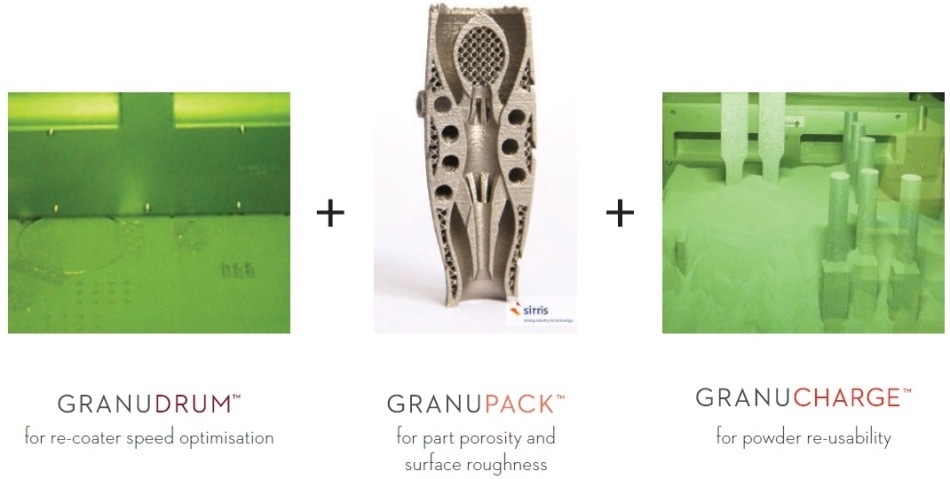
References
- Powder Technology 283, 199–209 (2015)
- Powder Technology 224, 19–27 (2012)
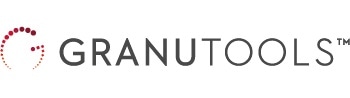
This information has been sourced, reviewed and adapted from materials provided by Granutools.
For more information on this source, please visit Granutools.