A process which involves deterioration or degradation of metal is referred to as corrosion. The most typical example of corrosion is the degradation of alloys or metals. Usually, corrosion phenomena are electrochemical in nature and consist of two or more reactions on the surface of the corroding metal.
One of the reactions is a reduction reaction (e.g., reduction of oxygen), and is referred to as the cathodic partial reaction. The other is the oxidation (e.g. dissolution of iron), also referred to as the anodic partial reaction. The products of the electrochemical reactions can chemically react with each other to create the final product (e.g., rust). For example, the corrosion of iron to create rust happens according to the overall reaction:
.jpg)
This reaction includes the reduction of oxygen, the dissolution of iron, and formation of rust:
.jpg)
Types of Corrosion
Microbiologically Induced Corrosion (MIC)
Microbiologically Induced Corrosion (MIC) refers to the corrosion which is caused by biological organisms or microbes. These microbes are categorized by common characteristics such as compounds they effect (i.e., sulfur oxidizing) or their by-products (i.e., sludge producing).
They are all categorized in one of two groups based upon their oxygen requirements; one being aerobic (requires oxygen) such as sulfur oxidizing bacteria, and the other being anaerobic (requires little or no oxygen) such as sulfate reducing bacteria.
Crevice Corrosion
Crevice corrosion is a localized form of corrosion that happens in the presence of stagnant solution in a small (micro) crevice. Local chemistry changes in crevices (shielded areas) such as those formed under insulation material, gaskets, disbonded coatings, threads, fastener heads, surface deposits, washers, lap joints and clamps, can cause crevice corrosion.
Galvanic Corrosion
Galvanic corrosion refers to corrosion damage which occurs when two dissimilar materials are coupled in a corrosive electrolyte. It happens when two or more metals that are dissimilar are brought into electrical contact under water for example.
When a galvanic couple forms, one of the metals in the couple becomes the cathode and corrodes slower than it would alone, the other becomes the anode and corrodes faster than it would on its own. When in seawater, either metal in the couple may corrode.
Uniform Corrosion
Uniform corrosion results in the loss of material until failure. It is characterized by corrosive attack proceeding evenly over the entire surface area, or a large fraction of the area of the metal under attack. This is the most widespread form of corrosion seen.
Pitting Corrosion
Pitting corrosion is a localized form of corrosion by which pin holes or pits are created in the material. Pitting is seen to be more dangerous than uniform corrosion damage as it is more difficult to predict and therefore design against. Corrosion products often cover the pits, which often makes the detection extremely difficult. A narrow, small pit with minimal overall metal loss can result in the failure of a whole engineering system.
.jpg)
Figure 1 - Different types of corrosion:
1. Uniform corrosion 2. and 3. Pitting corrosion 4. Galvanic corrosion 5. Crevice corrosion 6. Microbiologically induced corrosion
Electrochemical Characterization Methods for Corrosion
Electrochemical Noise (ECN)
During localized corrosion, electrochemical noise is produced by a combination of stochastic (random) processes, for example the breakdown of passive films and repassivation. ECN is the measurement of the current and/or potential noise and analysis of the data by utilizing Fast Fourier Transform (FFT).
Electrochemical Impedance Spectroscopy (EIS)
Electrochemical Impedance Spectroscopy or EIS has been successfully applied to the study of corrosion systems in recent years. One benefit of EIS over direct current (DC) methods is the possibility of utilizing extremely small amplitude signals without disturbing the properties which are being measured significantly.
Linear Sweep Voltammetry (LSV)
One of the most commonly employed techniques for characterizing corrosion phenomenon is linear sweep voltammetry or LSV. It involves sweeping the potential of the working electrode and then measuring the current response. Valuable information can be discovered about the corrosion rate, corrosion mechanisms, and susceptibility of specific materials to corrosion in various environments by using LSV.
Measurement of Corrosion Rates
Exposing the sample to the test medium (e.g. sea water) and measuring the loss of weight of the material as a function of time is the simplest way of measuring the corrosion rate of a metal. Yet, even though these tests are simple, there is no easy way to extrapolate the results to forecast the lifetime of the system under investigation.
In addition, some corrosion processes happen with no significant mass change (e.g. pitting corrosion) which makes them hard to detect by gravimetric methods. Electrochemical techniques deliver an alternative to traditional methods employed to establish the rate of corrosion. Direct and quantitative determination of corrosion rates can be established by using a simple electrochemical measurement like LSV.
Most corrosion phenomena are electrochemical in nature and consist of reactions on the surface of the corroding metal. So electrochemical tests techniques can be employed to characterize corrosion mechanisms and predict corrosion rates.
Calculation of Corrosion Rates
The corrosion rate is dependent on the kinetics of both cathodic (reduction) and anodic (oxidation) reactions. There is a linear correlation between the metal dissolution rate or corrosion rate, RM, and the corrosion current icorr according to Faraday’s law:
.jpg)
Where M is the atomic weight of the metal, ρ is the density, n is the charge number which indicates the number of electrons exchanged in the dissolution reaction and F is the Faraday constant, (96.485 C/mol), A is the area of the sample. The ratio M/n is also sometimes referred to as equivalent weight.
Calculation of Corrosion Currents
The determination of corrosion currents is required for calculation of corrosion rates. The corrosion currents can be calculated using Tafel Slope Analysis once reaction mechanisms for the corrosion reaction are established.
The relationship between current density and potential of anodic and cathodic electrode reactions under charge transfer control is given by the Butler-Volmer equation:
.jpg)
In the above equation E is the applied potential and i the measured current density. The overpotential η is defined as the difference between applied potential and the corrosion potential. The corrosion potential, Ecorr is the open circuit potential of a corroding metal. The corrosion current, icorr, and the Tafel constants ba, and bc can be measured from the experimental data.
The Butler-Volmer equation simplifies to the Tafel equation for large anodic overpotentials (η/ba >> 1) for the anodic reaction:
.jpg)
Analogously, for large cathodic overpotentials (η/bc << -1) the Tafel equation for the cathodic reaction is given by:
.jpg)
A straight line is predicted using the Tafel equations for the variation of the logarithm of current density with potential. So, currents are frequently shown in semilogarithmic plots known as Tafel plots. This type of analysis is known as Tafel Slope Analysis.
.jpg)
Figure 2 - Current potential plot for iron screw immersed in seawater.
It is necessary to have information on the electrode surface area, equivalent weight and the density of the material in order to carry out Tafel analysis. The Tafel slope analysis supplies the polarization resistance and corrosion rate. Yet, if the linear Tafel region covers at least 1 decade in current, a correct estimate of the Tafel slopes is possible.
.jpg)
Figure 3 - Tafel plot for iron screw immersed in seawater. The linear parts of the Tafel plot are identified.
Measurement of Polarization Resistance
Polarization Resistance, Rp
When its potential is forced away from its value at open circuit or corrosion potential, an electrode is polarized. Due to electrochemical reactions it induces at the electrode surface polarization of an electrode causes current to flow. The polarization resistance is shown by the following equation:
.jpg)
If ΔE is the variation of the applied potential around the corrosion potential and Δi is the resulting polarization current. The polarization resistance, Rp acts like a resistor and can be measured by taking the inverse of the slope of the current potential curve at open circuit or corrosion potential.
During the polarization of an electrode, the magnitude of the current is controlled by reaction kinetics and diffusion of reactants both away from the electrode and towards it. Using the Butler-Volmer equation for small η, i.e. ,for potentials close to corrosion potential, the Butler-Volmer equation can be reduced to:
.jpg)
Alternately, if the expression is rearranged:
.jpg)
The corrosion currents from the polarization resistance can be calculated using the above equations if the Tafel slopes are known.
If the Tafel slopes are unknown, for example when corrosion mechanism is not known, the Rp can still be utilized as a quantitative parameter in order to compare the corrosion resistance of metals under a number of conditions. Low Rp implies low corrosion resistance and high Rp of a metal implies high corrosion resistance.
.jpg)
Figure 4 – LSV data for the corrosion of an iron screw in seawater.
Measurement of Rp Using LSV
The results of a LSV experiment carried out on an iron screw immersed in seawater can be observed in Figure 4. By performing a linear regression on data from - 0.329 V to - 0.309 V (i.e. 10 mV cathodic and 10 mV anodic relative to the corrosion potential), the slope of the curve at corrosion potential (- 0.319 V) can be calculated.
Figure 5 shows the results of the regression. The polarization resistance Rp is calculated from inverse of the slope (1/slope) and is established as 9.442 kΩ.
.jpg)
Figure 5 – The calculated regression line equation for the corrosion of an iron screw in seawater.
Measurement of Rp Using Electrochemical Impedance Spectroscopy (EIS)
Electrochemical impedance spectroscopy can also be used to measure polarization resistance. A Randles equivalent circuit (shown in Figure 6) can be utilized to estimate Rp for simple systems where the Nyquist plot shows one semicircle,
The Nyquist plot of experimental data for the corrosion of iron in sulfate solution is shown in Figure 7. The solid line represents the regression of the Randles circuit to measure the polarization resistance Rp.
.jpg)
Figure 6 – The Randles equivalent circuit.
.jpg)
Figure 7 – Nyquist Plot for Estimation of Rp for corrosion of iron in seawater using EIS.
Corrosion Inhibitors
A corrosion inhibitor is a substance which when added in a small concentration to an environment decreases the corrosion rate of a metal which is exposed to that environment. Inhibitors frequently play a key part in the oil processing and extraction industries where they have always been seen as the first line of defense against corrosion.
Mixed Inhibitors
Mixed inhibitors function by decreasing both the anodic and cathodic reactions. They are typically film-forming compounds which cause the formation of precipitates on the surface to block both cathodic and anodic sites indirectly.
Hard water which is high in magnesium and calcium is less corrosive than soft water. This is because of the tendency of the salts in the hard water to precipitate on the surface of the metal to form a protective film.
The most common inhibitors of this category are the phosphates and the silicates. For example, sodium silicate is utilized in a number of domestic water softeners in order to prevent the rust water occurring. Sodium silicate protects copper, steel, and brass in aerated hot water systems. Yet, protection depends heavily on pH and is not always reliable.
For effective inhibition, phosphates also need oxygen. Phosphates and silicates do not afford the degree of protection given by nitrites and chromates, yet they are extremely useful in situations where non-toxic additives are needed.
Cathodic Inhibitors
Cathodic inhibitors act either by selectively precipitating on cathodic areas to limit the diffusion of reducing species to the surface or by slowing the cathodic reaction itself. The rates of the cathodic reactions can be slowed by the utilization of cathodic poisons. Yet, cathodic poisons can also heighten the susceptibility of a metal to hydrogen induced cracking, this is because hydrogen can also be absorbed by the metal during cathodic charging or aqueous corrosion.
By the utilization of oxygen scavengers which react with dissolved oxygen, the corrosion rates can also be decreased. Sulfite and bisulfite ions are examples of oxygen scavengers that can combine with oxygen to create sulfate.
Anodic Inhibitors
Anodic inhibitors typically act by forming a protective oxide film on the surface of the metal to cause a large anodic shift of the corrosion potential. This shift forces the metallic surface into the passivation region. They are also sometimes referred to as passivators. Some examples of anodic inhibitors are molybdates, nitrates, chromates, and tungstate.
Volatile Corrosion Inhibitors
Volatile Corrosion Inhibitors (VCI), also called Vapor Phase Inhibitors (VPI), are compounds transported in a closed environment to the site of corrosion by volatilization from a source.
In boilers, volatile basic compounds like hydrazine or morpholine, are carried with steam to prevent corrosion in the condenser tubes by shifting surface pH towards less acidic and corrosive values, or by neutralizing acidic carbon dioxide. In closed vapor spaces like shipping containers, volatile solids such as salts of dicyclo-hexylamine, hexamethylene-amine and cyclohexylamine are used.
The vapor of these salts condenses and is hydrolyzed by any moisture to liberate protective ions when these inhibitors come in contact with the metal surface. It is advantageous, for an efficient VCI, to supply inhibition quickly whilst also lasting for long periods. Both qualities depend on the volatility of these compounds; quick action wanting high volatility while enduring protection needs low volatility.
Evaluation of Corrosion Inhibitors
Electrochemical techniques are routinely employed for the assessment of the efficiency of corrosion inhibitors. The benefits of electrochemical methods are short measurement time and mechanistic information that they supply, which help not only in the design of corrosion protection strategies but also in the design of new inhibitors.
The LSV experiments can assess the performance of the corrosion inhibitor. Starting the experiments at cathodic potentials made sure that any oxide layer present prior to the beginning of the experiments was decreased.
The polarization curves for solutions with and without inhibitor, in red and in blue respectively, are shown in Figure 8. The anodic part of the polarization curve without inhibitor is usual for active metal dissolution.
.jpg)
Figure 8 – Linear polarization measurement in the absence (blue) and presence (red) of a corrosion inhibitor.
The data suggests that there is a shift of the corrosion potential in the anodic direction and a reduction in the anodic current when an anodic inhibitor is added to the solution. The corrosion inhibitor also leads to the formation of the passive film evidenced by the appearance of the passivation plateau.
Resources
ASTM International – Standards Worldwide
www.astm.org/Standard/standards-and-publications.html
NACE International Standards
nace.org/resources
Introduction to Corrosion Science
Author: E. McCafferty Springer 2010
The Fundamentals of Corrosion
Author: JC Scully Pergamon 3e 1990
Principles and Prevention of Corrosion
Author: Denny A Jones Pearson 2e 2013
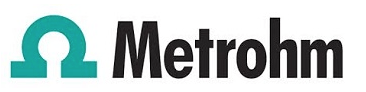
This information has been sourced, reviewed and adapted from materials provided by Metrohm AG.
For more information on this source, please visit Metrohm AG.