Plasma processing is one of the most frequently used processing methods in the manufacturing of electronic systems, especially for the production of microelectronics such as integrated circuits (ICs).
Large-scale ICs can consist of up to 400 different layers. The creation of these complicated structures uses repeated steps of plasma etching and epitaxial growth. To ensure that the IC functions correctly it is important that, during etching, material from the new layer being etched is fully removed without the layer below it being damaged. In addition, to further complicate things, etching must take place at vacuum conditions to stop contaminants from forming deposits.
During the ionizations that occur during processing large volumes of energy are transferred to the material being ionized, and this results in the material emitting bright light. This light can be used to monitor the process.
.jpg)
Exploiting Changes in Energy State
The emission of light during ionization occurs due to the excitation of atoms to a higher electronic state, these atoms then spontaneously relax to their ground state and emit a photon during the process. The total energy of this process is conserved meaning that the photons emitted have an energy that is equal to the difference between the atom’s ground and electronic states. This discrete energy is unique to each atom, meaning its measurement can be used to determine which elements are present in a sample.
Measurement of the photons emitted by a sample in this way is called optical emission spectroscopy (OES), and this technique allows process engineers to determine the endpoint of a plasma etching step, i.e. when a layer has been fully removed.
By incorporating the monitoring ability that OES provides into their manufacturing processes producers of ICs can fully automate their etching steps without having to worry about over- or under-etching.
An example of this process, where OES of the 431 nm CH line, using an Avantes spectrometer via a fiber optic cable, was used to monitor etching is shown in Figure 1 – courtesy of Professor Richard van de Sanden’s Plasma and Materials Process (PMP) group at the Eindhoven University of Technology. OES automatically tells the user when a lower layer has been reached by the sudden appearance of new spectral lines that correspond to the material below.
.jpg)
Figure 1. Etching Depth and 431nm spectral peak intensity for monitoring CH content.
Working in Vacuum Environments
If possible, it is best to monitor the process using a collection lens (also known as a collimating lens) that collects light through an observation window and passes it through a fiber optic cable. However, this is often not possible when using industrial scale plasma etchers and epitaxial growth reactors and instead vacuum sealed fiber optic cables should be used to collect light from the wafer.
Whilst vacuum sealed fiber optic technology is inherently complicated, it is well developed and available commercially.
The fiberoptic feedthroughs produced by Avantes use an M12 housing, 2 SMA fiber-optic interconnects, produced to work with fiberoptics in vacuum chambers of pressures around 10 – 7 mbar and wall thickness between 5 – 40 mm, and a Viton® O-ring.
In Optical Emission Spectroscopy, Resolution is Key
Like other analytical techniques involving atomic spectroscopy OES tends to need a high spectral resolution in order to correctly identify different atomic species. The high resolution of Avantes’ miniature spectrometers makes them perfect for OES.
Avantes’ AvaSpec-ULS4096CL-EVO uses a 3600-grove density grating to provide a fine resolution of 0.05 nm for emissions between 200 and 400 nm. In addition, the spectrometer uses a sensor consisting of a CMOS detector array, which provides improved dynamic range and linearity, perfect for high light level applications such as plasma etching OES.
AvaSpec spectrometers, when used alongside Avantes’ novel rapid electronic triggers, analog and digital I/O functionalities and fast data transfer, can be easily incorporated into high-speed wafer plasma systems.
.jpg)
AvaSpec-ULS4096CL-EVO
Spectral Range v. Resolution
There are some OES instruments that have been designed to be application specific, which use a limited spectral range for the identification of specific elements, however the majority of OES applications require a wide range of elements to be identified. Multi-purpose instruments, for use in any OES application, require a larger spectral range; meaning they can be impacted by the fundamental limitations of fixed grating spectrometers, i.e. that a greater spectral range results in a lower resolution.
OES spectrometers produced by Avantes use an optical design that provides an enhanced response, meaning a fine resolution of 0.5 nm can be achieved over a wide spectral range of 200 – 1100 nm. In addition, the spectrometers can be concatenated together to give multiplex systems that allow multichannel operation.
This configuration means each spectrometer in the system can be used to collect spectral information over a smaller spectral range, e.g. 200 – 300 nm and at a much higher resolution (< 0.1 nm).
Multiplexed spectrometer systems allow the OES signal to be divided evenly between each spectrometer via a multichannel fiber optic bundle. Multiplexed system are faster and more stable than large scanning spectrometers, whilst also being less expensive.
Depending on the needs of the user, multiplexed spectrometer configurations can be provided as a custom, integrated turn-key system (Figure 3).
.jpg)
AvaSpec Multi-channel Fiber-optic Spectrometers
More Applications for Optical Emission Spectroscopy
The determination of when a stage of plasma etching has been completed is currently the most common application of OES, however there are many other applications of the technology. A full exploration of the other applications of OES goes beyond the scope of this article, though some are briefly mentioned below.
OES can be used as a cheaper alternative to mass spectrometry (MS), for quality control applications, especially when inductively coupled plasma OES (ICP-OES) is used. ICP-MS is frequently employed for elemental verifications in the aerospace, automotive and recycling industries, where the use of ICP-MS would be superfluous.
OES is also used for the monitoring of metal purity, e.g. of aluminum, steel or copper, by measuring their mutant emissions. In addition, OES is also employed during the 3D printing of metals where it is used to monitor the laser ablation spectrum.
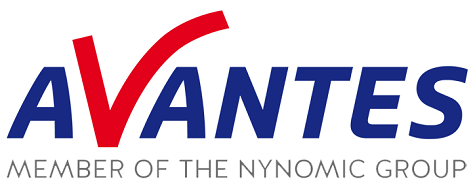
This information has been sourced, reviewed and adapted from materials provided by Avantes BV.
For more information on this source, please visit Avantes BV.