The main advantages of on-site oil analysis are productivity increases and maintenance cost savings from growing the uptime of running machines. If the correct oils are utilized and they are dry, clean and fit for use then machines will run longer.
One of the most common lubrication problems leading to machine failure is oil mix up. A simple task which can enhance machine reliability is using the correct lubricating oil in a machine. Monitoring the viscosity, grade and brand of incoming oil and checking for contamination of alien fluids helps to decrease the possibility of oil mix up and keep the machines running at maximum efficiency.
Seals and filtration systems must work correctly, and oils should be checked regularly to keep the oil clean, dry, and free of contaminants. Dirt and sand in oil lead to the generation of abrasive wear. Corrosion is caused by moisture in oil. Coolant or fuel in engine oil alters viscosity and leads to the generation of adhesive wear. Keeping the lubricating oil clean and dry at all times is vital.
Oil conditions must be frequently monitored to ensure the oil is utilized within its performance specification to keep it fit for use. A well balanced oil analysis program would monitor oil contamination, machine wear condition, and oil degradation.
Key parameters are regularly measured and their trends are closely monitored. If any surpass the parameters, the alarm limits, or an alteration in the trending rate is identified, reliability engineers are alerted and maintenance actions may be required to resolve possible problems.
The cost savings from a well-executed oil analysis program derive from decreasing production loss from unplanned downtime because of catastrophic failure, plus lowering repair costs and stopping unnecessary oil changes. In a paper mill or power plant, the majority of cost savings come from decreased machine down time and repairs.
In the instance of a mining site possessing hundreds of hauling trucks, the majority of cost savings come from preventing engine failures. However, for a municipal transportation fleet, the cost savings from oil analysis are a result of less material, recycling and labor by increasing the oil drain intervals.
On-Site or Outsource
Within the reliability professional community, the awareness of oil analysis has increased over the years. Every year, multiple case studies are published which show how oil analysis and lubrication management practices enhance machine reliability whilst saving money.
Organizations or companies which possess large fleets of high value assets have established processes and policies employing oil analysis in their predictive maintenance practices.
It is common to outsource oil analysis to an offsite oil laboratory. Hundreds of millions of oil samples every year are analyzed by laboratories around the globe. Outsourcing oil analysis involves gathering oil samples from an asset and shipping them to a lab.
Lab technicians then carry out the requested oil analysis tests by asset type. Next, an analyst reviews the data and supplies recommendations which are included in a final report. The report is then returned to the user for review and, if required, maintenance actions are carried out based on the recommendations and maintenance schedule.
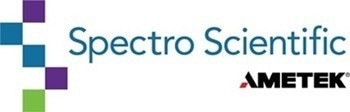
This information has been sourced, reviewed and adapted from materials provided by AMETEK Spectro Scientific.
For more information on this source, please visit AMETEK Spectro Scientific.