When General Plastics works with design engineers, they quickly look into the technical requirements of the planned application and the available polyurethane materials.
.png)
Both General Plastics and their customer come together to detail compressive and shear strengths, maximum temperature, density, and other application needs. Once an ideal polyurethane foam formulation has been chosen for the application, the next question is where to find services that will turn the raw material into a final product.
Saving Time and Money with Production Services
General Plastics not only manufactures premier polyurethane foams, but also assembles, machines, and fabricates finished components. As the original manufacturer, General Plastics will have the most knowledge on how to process its own materials. Additionally, utilizing a one-stop shop makes several steps in the supply chain more efficient. For example, there are fewer vendors to manage, decreased shipping costs, a reduced margin of error, and an increase in time saved overall.
A brilliant example is a manufacturer of garage doors who approached General Plastics for the supply of materials. Due to the machining and sanding services offered, General Plastics was equipped to provide not only the raw material but also the completed parts in the required quantities. This enabled the garage door manufacturer to remove many in-house finishing procedures and save capital in the total cost of goods sold.
Another customer, that manufactures underwater floatation devices with General Plastics, chose to use the fabrication services also. Once General Plastics was machining, painting, and finishing the floatation planks for the client, their supply base was merged from three vendors to only one. This change successfully halved the lead times and decreased costs by 33%.
.png)
The Specialty Skills of a One-Stop Shop
Changing to a single-supplier solution requires the chosen vendor, like General Plastics, to have a varied range of specialized skills.
For example, General Plastics offers various in-house production services (such as molding, machining, and tooling), but also has the experience and knowledge to locate, bond, and assemble materials and components that may be difficult to integrate well. Along with this, General Plastics can produce customized shapes, formulations, and details to adhere to stringent specifications.
A medical components company also decided to work with General Plastics to manufacture one of its products due to its unique capabilities. They had experienced issues with their previous supplier’s performance and hoped to source a new vendor with an excellent reputation. In talks with their customer, General Plastics discussed their material requirements, gave support and feedback, finalized the components entirely in-house, and met delivery goals. The customer was so pleased with the outcome that they asked General Plastics to take over the production of further products to streamline their supply chain even more.
With over 80 years of experience in manufacturing, General Plastics has invested heavily in fabrication services to better serve their diverse customer base.
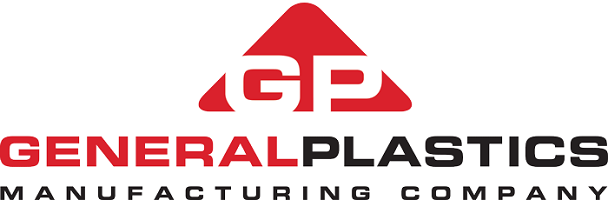
This information has been sourced, reviewed and adapted from materials provided by General Plastics Manufacturing.
For more information on this source, please visit General Plastics Manufacturing.