The gold standard of qualitative compositional analysis is OES spectroscopy. Compared with other analytical techniques, OES analyzers boast the lowest detection levels, as well as the largest element range. When using OES analyzers, ppm levels of boron, phosphorous, sulfur, nitrogen in duplex steels, and carbon can be measured.
.jpg)
However, to have this ultra-sensitivity, the equipment must be of the highest possible standard to give accurate results. Any error within the analyzer, no matter how minute, risks causing a false reading.
Hitachi High-Tech provides the market with leading and highest quality analyzers that are available today. The company’s Global Operations Director, Steffen Zoller, explains below how they guarantee that every OES analyzer it provides is manufactured to the highest possible standard.
Hitachi High-Tech keeps key competencies in-house at its specialist facility. From start to finish, the analyzers are developed, designed and manufactured at the specialist production site in Uedem, Germany (which is located approximately 70 Km north of Düsseldorf). Hitachi believes that to maintain the high quality of their instruments it is crucial to retain control on-site of manufacturing and expert involvement.
For a specialized instrument such as an OES analyzer, maintaining this close relationship between the design and production departments is vital. For instance, if necessary, each process and incoming part can be witnessed and tested by the lead design engineer.
Hitachi also uses six sigma and lean manufacturing methodologies. In addition, they have recently reconstructed their production facility and process to the highest of standards with controlled environments, including clean rooms for calibration and optics.
Quality from the Design Stage
Hitachi understands that its OES analyzers have to be accurate in order to be practical for customers, but they must also be able to endure the harshest and most demanding environments.
The company’s design engineers also develop the equipment to tolerate constant use under harsh conditions, as well as being certified to ISO 9001:2015 to ensure the highest quality. This means that the equipment is ready to work for you as a workhorse, whether in a foundry, a manufacturing plant or scrapyard. Each part of the device endures rigorous and strict testing as part of the quality processes.
Hitachi Uses the Best Components – Testing it all Themselves
Having been in the industry for a long time, Hitachi enjoys long-lasting and close relationships with trustworthy suppliers. Despite this, the company remains vigilant and is careful not to take anything at face value.
Within the production process, each individual component is meticulously tested. This process involves carrying out a visual inspection and Hitachi’s own quality assurance and control testing for vital properties inherent within the equipment, such as optical performance.
Manufacturing Quality Control
An OES analyzer has multiple different components and is a complex piece of equipment: from the spectrometer at the machine’s heart, to the software providing the result for the operator.
The assembled components are verified by a 170-point quality inspection after each manufacturing stage, after which the parts are only released to the next stage if they are successful. This testing provides immediate feedback on the quality of these production procedures, as well as ensuring the quality of the finished analyzer. These checks permit Hitachi to work in an environment of constant improvement.
Calibration Check Before Leaving the Facility
The calibration check is the last stage of production. Each instrument’s calibration is checked with multiple certified reference materials as well as undergoing a functionality test during this calibration inspection.
These stages give precise, accurate results against several known samples and ensure that the analyzer is working flawlessly. The machine must pass this test to leave the facility. Each individual machine is also installed by one of our experts, so we can ensure that it will work successfully after transport and installation.
Hitachi is also an AEO, or authorized economic operator, which is an additional mark of quality when considering customs controls and procedures.
Want to See the Team in Action?
Watch here how Hitachi’s teams guarantee ultimate quality control without making compromises.
These are the stages Hitachi believes are necessary to create OES analyzers that their customers can rely on. They have mobile and stationary OES analyzers in its product range, which customers use for metal production, quality assurance and control, PMI safety inspection and recycling.
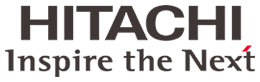
This information has been sourced, reviewed and adapted from materials provided by Hitachi High-Tech Analytical Science.
For more information on this source, please visit Hitachi High-Tech Analytical Science.