To maintain competitiveness, today’s manufacturers work extremely hard to minimize production costs. Their efforts can entail a change of material suppliers or the specification of a different material or type of finish. However, changes are often administered without appropriate examination of how they will affect long-term product performance. There are multiple testing solutions that can be implemented to replicate surface damage. This article considers scratch and mar damage.
Since the findings for each instrument are grounded in that tester’s unique system, it is typically not possible to compare data between different apparatus. In that case, how does one collate and interpret the test outcome to implement worthwhile decisions?
Importance of Repeatable and Reproducible Test Data
Firstly, the test data must be repeatable and reproducible. The primary objective of any test protocol should be the execution of tests in an identical manner, enabling a user to satisfactorily compare the results. ASTM International test methodologies comprise a precision statement that supplies the user with a notion of the results’ repeatability.
However, not all tests are equal, and the selection of the most appropriate methodology for a chosen material must be assessed before its implementation. If there is any hesitation, it is necessary to first contact relevant industry associations. Additional sources of information comprise instrument manufacturers, organizations responsible for test standards development, such as ASTM International and ISO, and companies, such as Taber Industries, which regularly offer expert advice and consultation on how to reproduce physical property damage, such as scratch and mar.
The stylus load, velocity and angle designated in a test methodology can normally undergo systematic alterations, allowing a comprehensive impression of the resistance to scratching to be generated. Following measurements of the width of the scratch, utilizing techniques such as the white light interferometer, it is possible to determine the scratch hardness, enabling the construction of scratch hardness maps. These indicate the plastic and elastic response of the material or coating under particular conditions and loads. As a result, it is possible to compare divergent substrates and coatings, and thus generate quantitative results under a controlled environment.
Scratch and Mar Resistance
Scratch and mar resistance is not an isolated or unique material characteristic; it is connected to several other physical properties. Consequently, companies should assess findings in concurrence with other tests. These tests can include the measurement of material resistance to chemicals, UV, corrosion, abrasion and impact, as well as other variables. For polymers, flow properties, weight advantages (density), dimensional stability and heat resistance (Vicat) should also be considered. It is essential not to disregard costs consequences including the final cost calculations (price, cycle rate, reject rate) along with any processing alterations that are needed.
The principal basis on which companies undertake laboratory testing is to make sure that they are manufacturing a high-quality commodity that will endure throughout its life cycle. For scratch and mar testing, the goal is to ensure that the product maintains a minimum visual appearance over its predicted lifespan.
Effects of Surface Damage
Irrespective of whether the material or coating is for functional performance or cosmetic appeal, surface damage that happens too early on will diminish how a consumer perceives a product’s quality. Among high-gloss finishes, such as piano-black components, because of the way in which light reflects off the smooth, mirror-like surface, any scratch or mar issues will be particularly discernable to the consumer. Consequently, the selection of a tester that can simulate the type of damage that will transpire during routine use is essential.
Test Program for Validating Product Quality
The employment of a worthwhile test program is an important step in the validation of product quality, and can make certain that the specified surface finish satisfies the consumer’s expectations. Although accelerated laboratory tests might not consistently detect potential problems or supply predictive performance results, they can be a cost-effective means of generating advantageous data in a reasonably short time span. Testing also offers a chance to generate value with a specified product, and can be an invaluable means of negating material or coating issues.
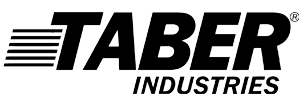
This information has been sourced, reviewed and adapted from materials provided by Taber Industries.
For more information on this source, please visit Taber Industries.