Typically, although laboratory techniques are not able to fully reproduce the mechanics observed in real life, a controlled test permits the researcher to undertake an approximation of field conditions and subsequent evaluation of materials utilizing the same set of criteria. This strategy can yield substantial insight into the multiple variables that influence a material’s performance, starting at its point of manufacture to after it is placed into service. This is particularly relevant when there are so many opportunities for damage to take place.
What is Scratching?
Scratching is the term used to describe the resistance of a solid body to penetration by an edge or protuberance on a second body that is traveling along its surface, and is typically equated with a singular incidence on the specimen surface [1]. Comparatively, marring is defined as relatively fine, shallow surface scratches spread over a larger area, usually resulting in the appearance of the material or coating surface being spoiled.
Scratch and Mar Resistance Tests
During a laboratory scratch test, a stylus with a defined geometry is drawn across a specimen surface with a known force and at a known speed. Mar tests may use a counter-faced material, such as steel wool, which generates damage over a greater area. The goals of most scratch and mar resistance lab evaluations comprise the determination of the behavior of the material under particular test conditions; the establishment of a relative ranking of related materials; and/or the determination of the failure limit of the material or surface coating. The overarching objective is to reproduce the damage that may transpire during everyday use and handling, shipping or assembly processes.
Any attempt to simulate scratch damage in a laboratory environment entails the determination of a complex set of interrelated properties. The objective of the test is to supply predictive performance under a particular group of criteria. However, the task of developing a test methodology is both difficult and multifaceted, a fact which becomes apparent during any evaluation of the conditions a product encounters during its life. Indeed, a sequence of tests might be necessary to pinpoint key variables.
Scratch Damage
The amount of scratch damage on a material surface can be affected by the test variables and demands a suitable methodology to ensure these influences are minimized. To many, it should be clear that different scratch traces can be produced in relation to the individual composition and geometry of the scratching instrument. By way of example, utilizing any of the following scratch indenter geometries can cause divergent mechanical deformations: conical diamond; cube corner; 1mm spherical ball (hardened stainless or tungsten steel); cylinder sectioned at 45° to the axis; pyramidal; 0.8 mm diameter helix; the radius edge of a paperclip.
Differences may also be instigated in accordance with the load that is applied to the stylus, or the speed at which the stylus is drawn across the specimen surface. Material properties, including hardness, surface roughness, texture, modulus of elasticity, gloss level, grain and coating thickness, might also impact the intensity of scratch damage.
Limitations of Scratch Testing Materials
After a test procedure is determined, the process of producing a scratch is reasonably straightforward. Nevertheless, evaluating and describing the outcome is not always simple. A number of contemporary plastics embody visco-elastic characteristics, meaning that the stresses in the plastic can relax during loading. Moreover, plastics might display an elastic recovery after applied stresses are withdrawn, which means that groove depth, displaced material, scratch width and severity of the damage might alter over time. Additional issues that influence the visual perception of scratches comprise the amount of strain whitening; scratch direction; the color of the sample; the time an observer is permitted to view the sample; and lighting and viewing conditions.
To maximize the utility of a laboratory test, the observations and conclusions should be sufficiently correlative with the product’s actual usage. The optimal solution would be to examine the product in actual usage under the proposed usage conditions. However, practical data typically requires several years to become available. Moreover, the costs of undertaking a field test can be restrictive, while the complexity of identifying the influences can also pose difficulties. When no other data exists, how can the results be correlated? How can the conditions to which a product might be exposed be determined?
The recommended starting point is to examine existing knowledge. If a new material is being considered, it is necessary to assess all available information on comparable field applications. If no data is readily available, it is important to acknowledge this as a limiting factor and an educated guess should be anticipated. Although the new material or coating option might behave differently than preceding selections, the data will be of greater value in conjunction with a baseline with which to compare the findings of the new material.
Conclusion
An understanding of the inter-relationship for different physical property tests also enhances the awareness of a particular coating’s performance. This information is key to establishing a predictive model for component life estimation and anticipated failure modes. However, caution is recommended, as no model is universally acceptable. Moreover, accelerated testing might not consistently detect possible problems or yield predictive performance results. To assist whichever model is selected, it is advantageous to obtain data that exhibits a specific relationship between laboratory tests and actual performance in the chosen end-usage.
References and Further Reading
- P.J. Blau, The Lab Handbook of Scratch Testing, Oak Ridge: Blue Rock Technical Publications, p. 1.2 (2002).
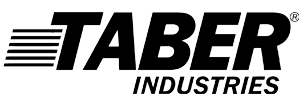
This information has been sourced, reviewed and adapted from materials provided by Taber Industries.
For more information on this source, please visit Taber Industries.