In this interview, Peter Faulkner from Olympus talks about the common challenges associated with stockpile identification in the cement industry and how XRF can help overcome them.
Why are stockpiles so important in the cement industry?
Stockpiles of raw materials are an essential component in the cement process. They create a storage buffer between the mine or quarry and the processing plant. When quarry operations or shipments are stopped or delayed, it is critical to stockpile enough raw materials to ensure continuous cement production.
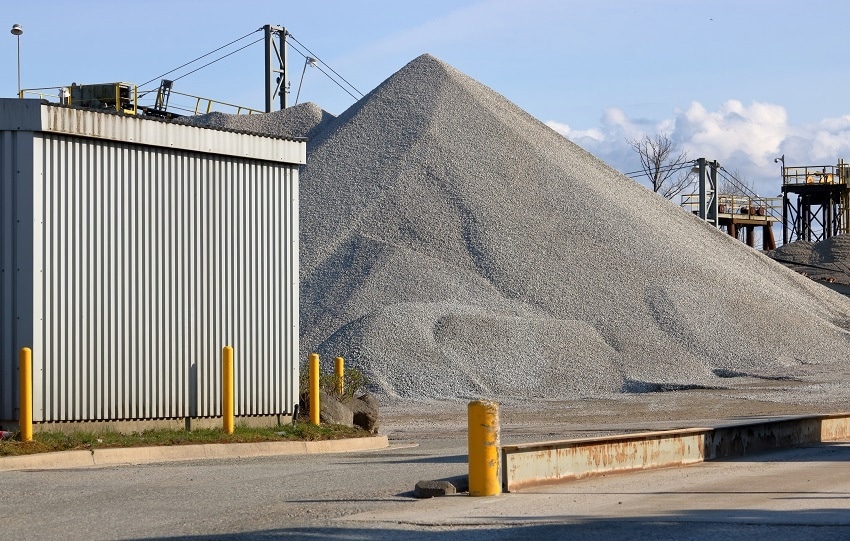
Image Credit: Shutterstock/EricBuemeyer
Why is the ability to identify and separate stockpiles based on their composition so important to the cement manufacturing process?
The cement manufacturing process includes several steps: crushing, blending, calcining, and grinding. The various cement types produced through this process consist of different compounds, requiring careful control of raw materials. For example, white portland cement requires very low levels of manganese (Mn), iron (Fe), and chromium (Cr) to achieve a brilliant whiteness.
What are the common challenges associated with stockpile identification in the cement industry?
Materials from quarries and mines naturally vary in composition and may contain unwanted raw materials or elements in undesirable concentrations. With a knowledge of the chemical composition of raw materials, chemists and engineers can make more informed decisions with regard to diverting material to specific stockpiles or blending material.
In addition, cement manufacturers across the world often use by-products from other industries, such as fly ash from power plants or slag from ironmaking and steelmaking. While by-products help manufacturers produce cement efficiently and economically, they often come from multiple sources, and, consequently, have compositional variation.
How do XRF analyzers rapidly characterize raw materials?
XRF analyzers can be calibrated to accurately measure all raw materials. For instance, production and quality personnel can use Olympus’ handheld XRF analyzer to easily measure material in the stockpile or as materials arrive or are delivered. While on-site, personnel can analyze raw materials with minimal or no sample preparation. This helps them assess the composition of a larger number of samples than is permitted using conventional laboratory methods. Further, these measurements only take seconds to perform. Raw materials may be measured at several places and the results averaged to compensate for any variation within a single load.
Which features of the Vanta™ handheld XRF analyzer can help to improve cement production processes?
Olympus’ Vanta analyzer is our most advanced handheld XRF device with the most modern electronic components. Most importantly, the detector and processor combined with ultra-low noise electronics produce faster, more accurate results. In addition, the rugged and durable design helps our customers stay productive in dusty, hot, and wet environments and other challenging working conditions.
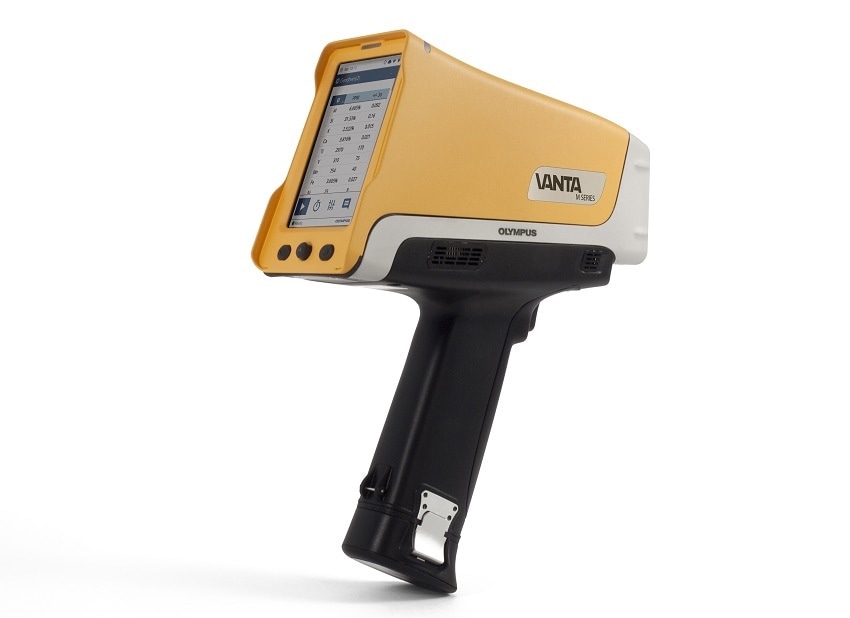
What types of elements can Vanta handheld XRF analyzers ID?
The Vanta analyzer’s silicon drift detector measures the most important elements for cement production, particularly the light elements magnesium (Mg), aluminum (Al), and silicon (Si). It also measures critical elements such as calcium (Ca), potassium (K), iron (Fe), and chromium (Cr), which we typically report as oxides such as MgO, Al2O3, SiO2, and CaO.
Coal is used as fuel during cement manufacturing, and the sulfur (S) produced is environmentally important. Thus, coal blending is important and can be controlled with S measurements from the Vanta analyzer.
How does the analyzer’s Axon Technology™ help provide accurate results?
Each Vanta analyzer features Axon Technology, which offers enhanced XRF signal processing. This revolutionary technology provides accurate, repeatable measurements for greater productivity and a fast return on investment. As the latest silicon drift detector can now detect 100,000 X-ray counts per second, Axon Technology’s primary function is to rapidly process the higher X-ray count rate for fast, accurate, and repeatable results with improved limits of detection.
Axon Technology also uses ultra-low-noise electronics coupled with a new processor. These components make Vanta analyzers remarkably responsive, pushing performance limits so you get the best results in the least amount of time. Axon Technology provides remarkable test-to-test and instrument-to-instrument repeatability, so your first test is the same as your last test no matter what instrument you may use.
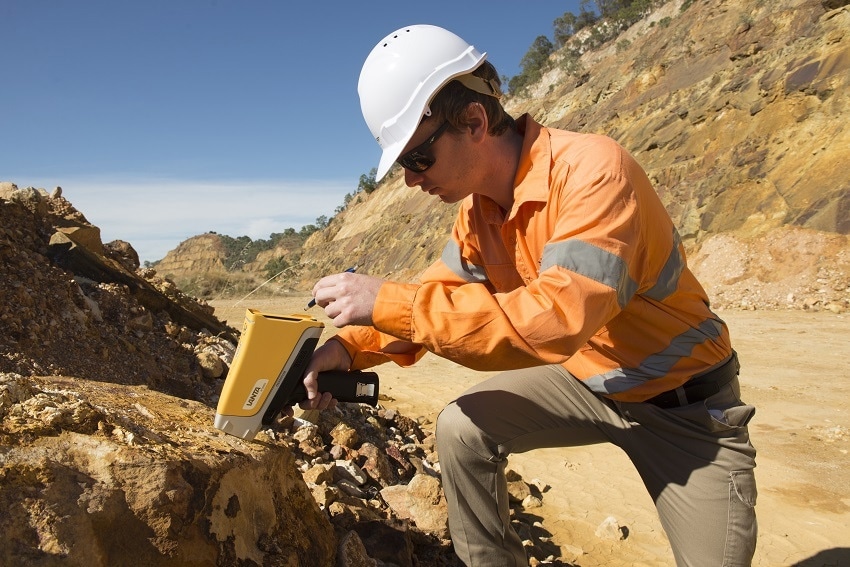
What are the benefits of mapping materials with the analyzer’s GPS?
Knowing each stockpile’s exact location and chemistry at the quarry or cement plant can help ensure operators of material handling equipment and blending equipment achieve the desired clinker analysis with confidence.
How is data saved and shared in Vanta analyzers?
The Vanta analyzer is versatile, so you can use several methods to transfer stored data from the analyzer for quality and production control purposes. First, the analyzer seamlessly integrates with other control systems. It also incorporates 4 GB embedded storage with microSD™ expandable memory. Data transfer is simple with wireless, Bluetooth®, and USB flash drive options.
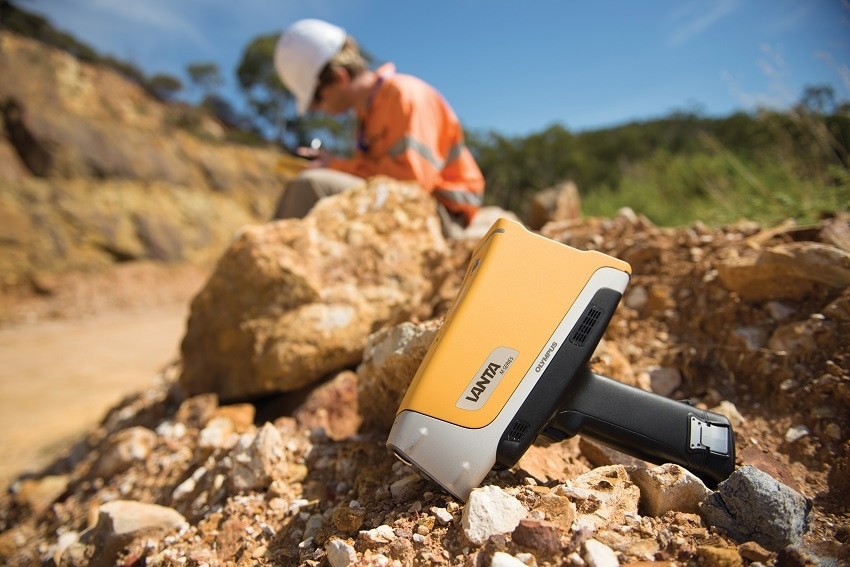
How do you think handheld XRF analyzers will transform the cement industry as we know it?
Handheld XRF analyzers provide process decision-makers in production and QC with immediate analysis, helping them make real-time process optimization decisions. As a result, cement plants can reduce or eliminate out-of-specification clinker production, saving materials, time, and ultimately money. If process and laboratory analyzers go offline or shut down, handheld XRF analyzers can help to keep the plant operational. Finally, this technology can reduce the need for urgent material analyses in the laboratory and be used as a screening tool to ensure that only correct samples are sent to the laboratory. Ultimately, the Vanta analyzer can replace the need for lab analyses in many stages of the production process, as well as optimize the selection of samples sent to the laboratory.
Olympus is a registered trademark, and Vanta and Axon Technology are trademarks of Olympus Corporation.
microSD is a trademark of SD-3C, LLC.
The Bluetooth® word mark and logos are registered trademarks owned by Bluetooth SIG, Inc. and any use of such marks by Olympus Corporation is under license.
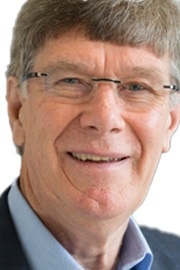
About Peter Faulkner
Peter has held sales and marketing positions within the analytical instrument field for over twenty years. He received his BSc in metallurgy from the University of Sheffield, UK and has many years’ experience within the metals and mining industries, including steel manufacturing, mining equipment, molten metal control sensors, and industrial gases prior to his work within the analytical instrument market. Peter has worked in these industries in South Africa, the UK, and the US. He is married to Gill and they have two daughters; all are “mad scientists.”
Disclaimer: The views expressed here are those of the interviewee and do not necessarily represent the views of AZoM.com Limited (T/A) AZoNetwork, the owner and operator of this website. This disclaimer forms part of the Terms and Conditions of use of this website.