Traditional fuels are still powering cars today, but the car of tomorrow will be electric. In 2018, 2 million electric vehicles (EVs) were sold worldwide according to Forbes; a 400% increase in 2015. It has been a gradual process, but personal transportation is becoming more reliant on electricity. It is also not just the locomotion that is reliant on electricity; the diverse and growing array of infotainment and navigation electronics offered in modern vehicles means that today’s vehicles require more electricity than ever before.
To meet these needs, the batteries in EVs have to provide more power, more cycles, and a longer lifetime, all crucial factors if they are ever to truly flourish. The go-to technology for the EV industry is the Lithium-ion (Li-ion) battery pack due to its impressive power density and charging efficiency. However, these batteries have relatively short operating lifetimes and quickly deteriorate with age, problems that are only made worse by challenging automotive environments.
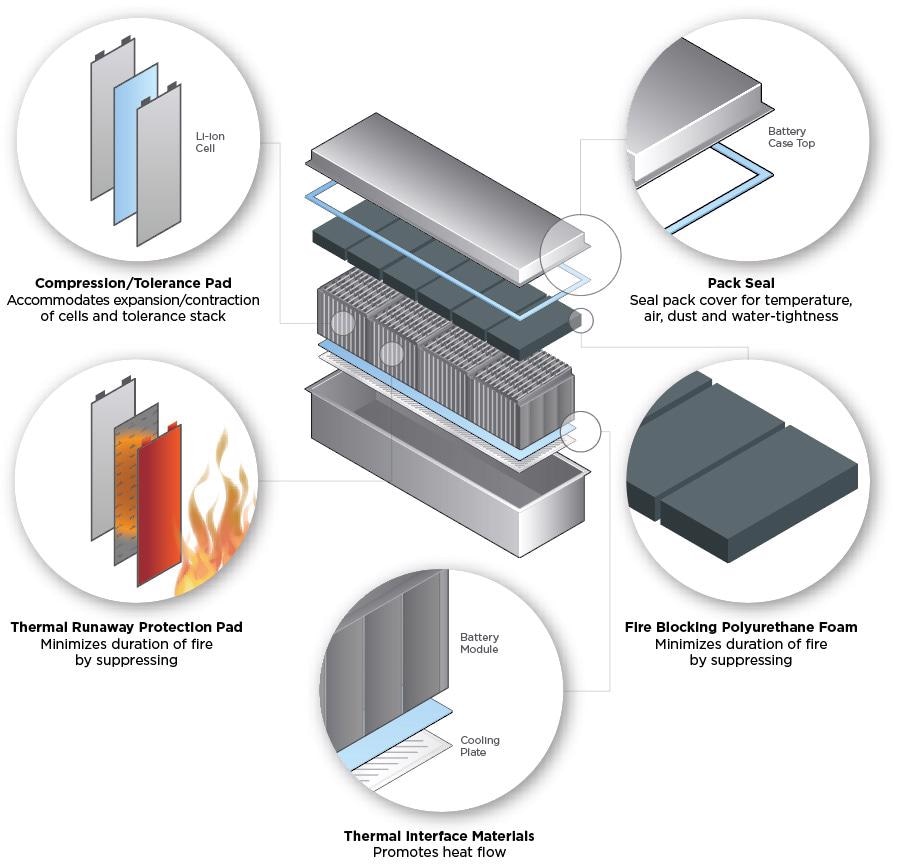
Drawbacks of Li-Ion Technology-Powered Electric Vehicles
EVs powered by Li-ion technologies are still not quite there when it comes to reaching traditional vehicles in terms of range or power density. This results in an EV needing to be recharged more frequently than a gasoline vehicle needs to be refueled. With each recharge cycle, the overall capacitance in the battery is slightly reduced, over time this shortens the battery lifespan.
On top of this, recharging alters the internal chemistry of the battery that causes a slight expansion in the physical dimensions of the battery cells. This can result in delamination of the internal battery cells and components or even battery pack deformation. This inhibits the effective thermal management of the battery, further degrading the lifespan, and in worse case scenarios leading to thermal runaway.
Ways to Improve Battery Lifespan
Research into this phenomenon indicates that optimal battery lifespan is achieved when a moderate amount of pressure is applied to the battery while it ‘breathes’ during its discharge and recharge cycles. The pressure ensures that electrical and thermal connections remain in contact during this time. This breathing can be considerable in large battery packs with many cells. However, there are some innovative material technologies that prevent delamination and deformation in pouch-type, actively-cooled, Li-ion battery packs, helping to keep more EVs and hybrids on the road every day.
Dielectric foams can facilitate the changes in dimensions of the battery cells, but deliver enough pressure to the cell package to inhibit misshaping and disconnections. The foam has a spring-like characteristic but is far superior to a spring. A spring delivers a potential return energy with increased deflection. But foams can be engineered to deliver a constant return energy for a wide range of compression amounts, a property known as compression force deflection (CFD). Springs are typically made of metal which is thermally and electrically conductive and can create hard spots in the battery.
Foam cushioning in the battery also has an impressive compression set, or how well the material can resist permanent deformation under compressive loads. The performance of specially engineered polyurethane- and silicone-based foams will still be steady beyond the lifespan of the battery, which cannot be said for other potential materials solutions such as other elastomers. The foam also has a key advantage in its remarkable operational temperature range, significantly larger than most other rubbers.
Foam materials will perform as intended even under the harsh stress of the automotive environment. As well as possessing excellent high and low temperature resistance, they are also thermally insulative, encouraging heat to be exhausted to the heat sink and rather than being transferred to neighboring battery cells. This insulative property is not impaired with increasing compression, a crucial property as excess heat is the greatest threat to batteries and electronics. A final point is that the dielectric nature of the foam averts arcing between cells.
Protecting the battery components is a supreme concern and foam materials offer important provisions.
Foam compression pads protect the battery components from vibration and shock, which is important for any sensitive system in automotive applications. Cushioning also reduces the potential sources of rattle in the battery, providing a quieter ride for vehicle occupants. Sealing the gaps between cells and other components with specially-engineered foam prevents the ingress of contaminants such as moisture and debris. Another issue can be that overheating Li-ion batteries can descend into thermal runaway, a rare but serious event where the batteries combust. This makes fire resistance a vital trait for compressive battery pads, another issue covered by the specially engineered silicone foams.
Saint-Gobain Polyurethane Compression Pads
The complicated requirements of compression pads leave these specially engineered microcellular polyurethane and silicone as the ideal choice for materials. High-performance polyurethane foams are effective across the temperature range -35 °C - 70°C and are easily cut to size. Saint-Gobain Tape Solutions has specially-engineered polyurethane compression pads available through the enhanced Norseal® PF20 Series and PF47. If the application will be operating over a larger temperature range, high-performance silicone foams should be preferred, with an increased operational temperature range of -51 °C – 204 °C. These Silicone foams also have low smoke generation and low flame spread qualities with a UL94 rating of V-0, to help mitigate the threats of thermal runaway. For these needs, Saint-Gobain supplies Norseal F12 and Norseal F20.
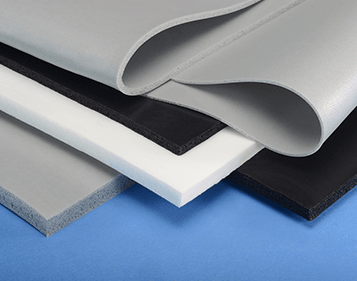
All of the Norseal products deliver consistent, reliable pressure (CFD) to the battery components over a wide range of compressive forces. Saint-Gobain has various products available with different CFD values, making compressive pads suitable for diverse applications, and all compressive pad materials can be supplied with or without an adhesive layer.
Summary
Li-ion batteries will remain the first choice for power in EVs for the foreseeable future. To expedite EV growth with current technologies, every area where these batteries can improve in efficiency should be explored and rectified. Manufacturers are looking to outside innovations with how to achieve longer battery lives and the long expertise and engineering knowledge of Saint-Gobain will be key in these innovations. Saint-Gobain is working today on the next generation of compression pad materials for tomorrow’s EV batteries.
Inside the Materials Driving E-Mobility: Tape Solutions for EV Battery Pack ProtectionPlay
The highest quality and longest-lasting batteries for EV applications are just a call or click away. Contact them for details.
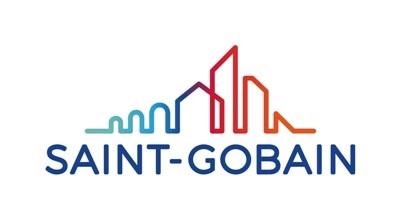
This information has been sourced, reviewed and adapted from materials provided by Saint-Gobain Tape Solutions.
For more information on this source, please visit Saint-Gobain Tape Solutions.