Fiber-reinforced polymers (FRP) are frequently characterized as thermoset goods, meaning that they have been manufactured utilizing a thermoset resin. Contrary to thermoplastics, a thermoset resin does not have a determined melting point after its first heat treatment phase.
This means that, after cooling, shapes cannot be reformed. There are multiple advantages to this, although they vary greatly according to the underlying features of the resin used to produce FRP.
This article outlines the features and advantages of thermoset resins in greater detail.
.jpg)
Types of Thermoset Resins Available
Different customized and standard thermoset resin systems are available for FRP manufacturing. Each solution offers unique thermochemical properties and pricing to suit the exact needs of different customers. A selection of these include:
- Phenolic
- Methyl Methacrylate (MMA)
- Epoxy
- Polyurethane
- Polyester
Outlining Polyester Thermoset Resins
For FRP manufacturing, polyester is a beneficial, general purpose thermoset resin. It is commonly available as isophthalic polyester (premium polyester) or orthophthalic (general purpose).
GP polyester resins provide average water resistance and a selection of common chemicals. PP thermosets are preferred for applications where the corrosives are more aggressive.
All of these resins are used to fabricate structural parts, grating, and panels for different markets. Despite this, they are frequently exceeded by vinyl ester thermoset resins when structural integrity over a long period is a requirement.
Outlining Vinyl Ester Resins
A custom thermoset solution, vinyl ester resin is produced by esterification of an appropriate epoxy with either an acrylic or methacrylic acid (MMA). It provides enhanced long-term mechanical performance compared to polyester thermoset resins and a decreased price point when compared to pure epoxy.
It provides superior resistance to moisture ingress and optimal anti-corrosive features when compared to GP polyesters. Consequently, vinyl ester resins are perfect for use in coastal and marine applications.
Outlining Epoxy Thermoset Resins
Epoxies are one of the most preferred thermoset resins for their superior thermal and mechanical properties in the cured condition.
The thermochemical integrity of standard epoxies is so great that they are frequently utilized for reinforcing and bonding FRP components, along with sealing cut ends of machined parts to mitigate chemical intrusion.
MMA can be used by itself for proprietary applications. However, the resin is most typically employed as a precursor to poly (methyl methacrylate) (PMMA), or as an epoxy-blend in customized thermoset resin mixtures.
Outlining Polyurethane Thermoset Resins
Polyurethanes are also commonly used because of their load-bearing and wear-resistant capabilities. They are frequently utilized for both impregnating resins and thick coating materials for components that need more comprehensive surface veiling, as polyurethane provides a durable surface finish.
Outlining Phenolic Thermoset Resins
Phenolic resins are synthetic polymers collected, in part, from formaldehyde. This justifies their outstanding flame-retardancy and low smoke emission capabilities, giving the best fire-resistant properties of all standard thermoset resins available to FRP manufacturers.
To discover more about phenolic resins in action, read Strongwell’s previous article: Phenolic Resin Products for the Oil and Gas Industry.
Thermoset Resins from Strongwell
Strongwell has recently been delivering its insights into the significance of thermoset resins in FRP with articles such as How and Why are Thermoset Resins used in Pultrusion? and Thermoset vs Thermoplastics: How are They Used in the World Today?.
This series of articles has hopefully answered any questions the customer may have had about producing thermoset FRP. For any additional queries, please contact a member of the team today.
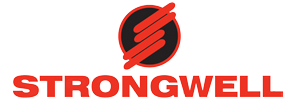
This information has been sourced, reviewed and adapted from materials provided by Strongwell.
For more information on this source, please visit Strongwell.