Using the Polytec PSV-3D Scanning Laser Vibrometer, Scientists at NASA’s Jet Propulsion Laboratory (JPL) have validated the dynamic response of spectrometer inlet funnels on the Mars Science Laboratory rover.
In November 2011, NASA JPL’s most recent mission to Mars sent the Mars Science Laboratory rover known as ‘Curiosity’ to determine whether Mars ever had, or still has, an environment that can support life. On the surface of the red planet, Curiosity will act as a robot geologist to gather information regarding the atmosphere, environmental conditions, geology, and potential biosignatures on Mars.
.jpg)
Figure 1: Inlet for soil samples.
Curiosity will gather environmental samples and soil while on Mars’ surface, and use spectrometers, radiation detectors, cameras, atmospheric sensors and environmental sensors to examine the samples on location. The resulting data will be sent to NASA scientists for analysis and interpretation.
To ensure that Curiosity’s data collection and analysis gives accurate results, preventing contamination of the rover is vital. Hence, flight models and engineering models are assessed separately to validate design requirements of the numerous systems aboard the rover.
.jpg)
Figure 2: Engineering model of the sample funnel.
.jpg)
Figure 3: Vibration analysis of the engineering model.
.jpg)
Figure 4: Frequency response of the model in X, Y, and Z directions.
The inlets (fig. 1) for the Chemistry and Mineralogy X-Ray Diffraction/X-Ray Fluorescence Instrument (CheMin) and Scientists at NASA’s Jet Propulsion Laboratory (JPL) have validated the dynamic response of spectrometer inlet funnels on the Mars Science Laboratory rover using the Polytec PSV-3D Scanning Laser Vibrometer.
To sift and shake soil from Mars’ surface into the spectrometers for analysis Science Lab on Mars Space System Component Design Validation using Scanning Laser Vibrometry Sample Analysis on Mars Instrument Suite (SAM) use piezo-driven actuators at the base of the funnels.
Due to the mass loading effects of attaching the transducers to the test article, limiting the amount of measurement locations possible, the models previously tested using accelerometers generated inaccurate data. Scientists at JPL have created a technique of non-contact dynamic performance testing in order to measure the vibration levels of the spectrometer inlet funnels for design validation.
Experimental Setup
Dynamically characterizing the engineering models (fig. 2) that have proven to effectively move soil through the funnel was the initial step in the validation process.
This data can be compared to the predicted results from the Finite Element Model (FEM) by characterizing vibration levels at numerous places on the inlet funnel, and so supplies a benchmark to be compared with measurements on the flight model later, which cannot be tested with soil.
The engineering model testing was carried out (fig. 3) with excitation to the actuators, utilizing a 10.5 kHz – 12.5 kHz sweep across 5 seconds for the CheMin and a 100 Hz – 500 Hz sweep across 15 seconds for the SAM. The procedure involved testing each one of the three actuators separately, then together in groups of two actuators exciting and all three actuators exciting.
The Polytec PSV-3D was employed to measure vibrations on the engineering model in 3D. The engineering model was placed in multiple positions to permit line of sight access from the Polytec sensor heads to the CheMin inlet (inside and outside), the CheMin collection screen, the CheMin funnel, and the SAM inlets.
The measurement positions were made up of around 20 to 30 measurement points on the inlets in addition to some locations on the collection screen and funnel. Time history data of the response to the sweep input was gathered in X, Y and Z directions at every measurement position (fig. 4).
The flight hardware had to be compared to the engineering models which were tested in order to confirm its functionality. The flight hardware is the SAM and CheMin instruments which are installed on the rover that is being sent to Mars. The rover is built in the Spacecraft Assembly Facility (SAF), a clean room.
Access was restricted to one meter away from the rover to stop any damage to the rover and its components. The Polytec PSV-3D was cleaned thoroughly and transported into the SAF to a location of one and a half meters away in front of the rover with a direct line of sight to the SAM and CheMin inlets (fig. 5).
Just the inlets of the SAM and CheMin could be seen above the rover’s top surface. Measurements were gathered using the same acquisition and excitation settings from the engineering model tests on the inside and outside rim of the SAM and CheMin inlets.
.jpg)
Figure 5: Vibration measurement on the inlets installed on the rover.
Results and Conclusion
The data was analyzed via JPL, low pass filtering the time history data and computing the RMS velocity over one chirp for each of the measurement positions. The resulting data was then compared to the engineering models and the flight hardware.
The results of this testing established that the dynamic behavior of the flight model equaled that of the engineering model, meaning that JPL scientists could depend on the functional performance characteristics of the inlet actuation system.
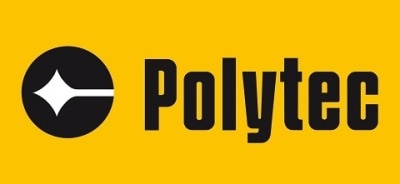
This information has been sourced, reviewed and adapted from materials provided by Polytec.
For more information on this source, please visit Polytec.