During the ANSYS Conference & 28th CADFEM User’s Meeting held 2010 in Aachen, Germany, a new approach was presented, which facilitates the integration of experimental modal analysis test into the CAE data chain.
This approach merges the properties of the PSV-3D Scanning Vibrometer with robotics and makes it viable to utilize CAE data for defining the test. The main advantage for the model updating process is the potential to work with imported FE geometries and coordinate systems and to automatically gather data at all nodal points.
Optical vs. Conventional Testing Approach
A case study compared conventional modal testing with accelerometers to the automated optical approach (Fig. 1). A cast alloy motorcycle gearbox cover was probed using both techniques. The focus was more on the benefits for the FE (finite elements) model update rather than comparing the efficiency of the techniques. The FE model was a tetrahedral mesh type with 19994 nodes and 69019 elements.
.jpg)
Figure 1: Comparison of two approaches to the FE model updating process. Center: FE model generation; left: accelerometer modal test; right: RoboVib® modal test.
.jpg)
Figure 2: CAD model with measurement locations. Wire frame model resulting from measurement points.
.jpg)
Figure 3: Measurement of the gearbox cover with RoboVib®.
.jpg)
Figure 4: Comparison of mode shapes from FE analysis (left) with RoboVib® (center) and conventional measurements (right).
.jpg)
Figure 5: MAC comparing FE simulation and tri-axial accelerometer measurements.
.jpg)
Figure 6: MAC comparing FE simulation and RoboVib ® measurements.
Accelerometer Test
An impulse hammer was utilized to excite the gearbox cover when testing with accelerometers. Measurements were gathered at 14 measurement points, as can be seen in Fig. 2. The locations were manually defined from the FE modal analysis results.
Test with RoboVib®
Optical techniques can use measurement grids that come from existing FE models of an object under test. Two major shortfalls of conventional testing techniques are overcome by being free of the restrictions of physically mounted and cabled sensors: the limited spatial density of measurement nodes and mass loading.
The Modal Assurance Criterion (MAC) values between measurement and simulation are improved considerably by overcoming these constraints, which enables a much better FE validation quality. The imported grid was coarsened by a factor of roughly 10, which still produces 100x more data points than the accelerometer test.
The robot was taught positions so that every side of the cover could be measured to scan the cover completely optically. Once the measurement was prepared during the daytime, the measurement was left to run overnight, as seen in Fig. 3. Data from 1630 nodes were gathered automatically and results from every robot position were stitched together automatically into a single seamless file for analysis.
Post-processing was carried out using the VMAP Modal Analysis package. Fig. 4 shows the results of the first two modes for the different measurement methods, in addition to the first two modes from FEA as a reference.
MAC Analysis
One of the key benefits of RoboVib® is the ability to compare and update finite element models (FEM). In this instance, the VMAP modal analysis program from TechPassion was employed to extract the modal parameters. This provides a native import of Polytec’s binary file format.
The mode shapes and Eigen frequencies may be compared to the values which are calculated from the simulation, and the modal damping added to the FEM. The FEM may now be tuned to the real structure and an enhanced model can be created by utilizing the VMAP FE model updating tools.
Accelerometer Test
The modal analysis from the conventional accelerometer test was restricted to the first two modes, at 592 Hz and 933 Hz. The MAC values between the same modes from measurement and simulation are displayed in Fig. 5 and are 0.67 and 0.59. These values demonstrate that some parameters of the test, e. g. the location and orientation of the sensors and accelerometer masses, decrease the measurement quality.
RoboVib® Test
Higher modes of the gearbox cover can be extracted using a 100x higher point resolution. The MAC values between the same modes from measurement and simulation are close to 1, showing a closer match than when compared to the accelerometer test. The MAC matrix for the first five modes is shown in Fig. 6, the diagonal values are near to 1 and the off-diagonal values are near to zero. This enables precise matching of the measured modes with the simulated modes.
.jpg)
Figure 7: CAE-Test Workflow.
Improving the Incompleteness Ratio
To ideally represent the later prototype, an FE mesh is generated. For a defined operating condition, the FE model should be able to predict the durability and dynamic parameters of these components. The results of the modal analysis, Eigen frequencies, and Eigen modes are then proven by the resulting damping values and mode shapes from the experimental modal test, as seen in Fig. 7.
Typically, FE models contain a few thousand nodes at least. In practice, a measurement for validating the FE model only has a subset of the FE nodes. The measurement is incomplete. This incompleteness is illustrated by the term “incompleteness ratio”:
.jpg)
Where n is the number of measured nodes and N is the number of nodes in the FE model. Some other authors have demonstrated that the quality of an FE model update is strongly dependent on the incompleteness ratio.
Grafe states: “The real challenge of updating large FE models is not so much the size of the models, as these can be solved by ever more powerful computers, but rather small incompleteness ratios” (Model Updating of Large Structural Dynamics Models Using Measured Response Functions, Doctoral thesis, University of London, 1998).
The number of measurement nodes must be high enough to establish a correct update of the FE model. Thus, the significant decrease of the incompleteness using the automatic approach with RoboVib® paves the way for an optimized model updating.
RoboVib® Structural Test Station Automated, Full-Field 3D Vibration Measurement
RoboVib® is a 3D vibration measurement station that is auto-configurable for whole-body vibration mapping of complex-shaped objects. By circumventing labor-intensive contact transducers, throughput, accuracy, and productivity are all enhanced.
For example, the measurement time required to distinguish the optically accessible regions of an entire car body is reduced from a few days to a few hours. Furthermore, the RoboVib® system can run unattended, enabling measurements to be scheduled night or day. Test fields and prototypes are utilized more efficiently, and the results are available quicker, because of the increased productivity.
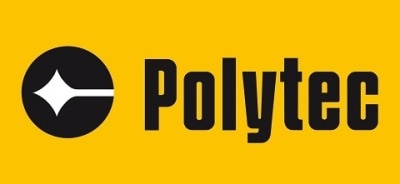
This information has been sourced, reviewed and adapted from materials provided by Polytec.
For more information on this source, please visit Polytec.