The pressure to complete a large amount of testing in the crucial downtime window will have been experienced by the majority of third-party testing companies that provide on-site testing of plant equipment.
.jpg)
It takes time to achieve reliable, accurate results, but extending the downtime is costly. So how is the perfect balance of fast testing times and 100% accuracy achieved for on-site PMI (positive material identification) testing?
On-site PMI Testing of Plant Equipment
Corrosion resistance and weldability are the two biggest challenges with refinery and other industrial plant equipment, both of which can be significantly improved by using the right grade of stainless steel.
Testing companies are regularly required to provide on-site checks for large quantities of steel piping to verify the composition. These checks have to be done without removing sections of installed pipework for lab-based testing. It would cost too much for the plant to remain down for the time taken to carry this out.
Any sub-standard grade of steel must be replaced with a new, correct part, which will also require checking to verify the composition. Carrying out comprehensive testing with high accuracy while limiting the downtime window of the plant is a challenge faced by most companies.
What Are You Testing for?
Ordinarily, the steel parts performance is dependent on whether a single element is present in the alloy. The relatively standard 304 grade of stainless steel will provide sufficient corrosion resistance in most cases. However, grade 316, which has higher nickel content and contains over 2% of molybdenum, is essential for some highly corrosive environments.
The alloy’s carbon content is key when it comes to weldability. The steel is weldable if the carbon content is below a certain limit and the weldability decreases with increasing carbon content. The hardness, strength and ductility are also affected by carbon. Accurate carbon content figures are, therefore, crucial for understanding the performance of specific alloys.
The Right Tool for the Job
A short downtime window may only allow time for one test. As such, a tool is required that will provide all the necessary information. The only technique to provide the required level of accuracy across the whole range of elements is OES (optical emission spectroscopy). There are other analytical techniques, such as XRF (X-ray fluorescence). However, OES is the only option for measuring carbon content for weldability.
Hitachi High-Tech’s PMI-MASTER Smart enables precise PMI measurement of safety-critical plant equipment. It can be used in hard-to-access places, as at only 15 kg it is portable and lightweight. In contrast to other portable OES analyzers on the market, it does not rely on a heating system and as such has an extremely fast start-up time.
With PMI-MASTER Smart, reliable measurements of all the crucial elements, including carbon, can be taken in minutes, meaning that it is possible to work through a large amount of testing in the few hours of downtime.
PMI-MASTER Smart is a portable device, providing fast, reliable and accurate results. Get in touch and speak with one of our experts if you would like more information.
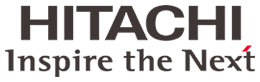
This information has been sourced, reviewed and adapted from materials provided by Hitachi High-Tech Analytical Science.
For more information on this source, please visit Hitachi High-Tech Analytical Science.