The EA8000 X-Ray Particle Contaminant Analyzer is created to assist lithium ion battery (LiB) manufacturers to enhance the performance, yield, and safety of their product.
.jpg)
The analyzer is designed to quickly identify and analyze undesired metal particles inside of the battery. These particles can create instant and catastrophic battery failure, which is frequently accompanied by explosion or fire.
The EA8000 utilizes two X-ray methods for efficient and rigorous analysis:
- X-ray transmission imaging to efficiently discover any metal particles and distinctly present their shape and size.
- X-ray fluorescence spectroscopy (XRF) to establish which metal elements are evident in the contaminated sites.
Metal contaminants can be introduced into the battery using the raw materials, or from the actual processing, for example, metal particles from machinery. The EA8000 is flexible enough to identify these in various stages throughout production, including as a last check prior to shipping.
How to Use the EA8000 in LiB Production
The following sections will describe how the EA8000 analyzer is employed inside of a LiB production facility.
Incoming Material Testing
The majority of the components utilized in production can be investigated in the EA8000, such as carbon-based powders employed in anodes and for improving conductivity, the cell separator, cathode materials, and the outer casing of the cell.
Slurries and powders can be spread out inside of a clear plastic container for the measurement, whereas solid components can be laid in a flat manner on the stage.
The analyzer can identify and analyze metal particles as small as 20 µm and the efficient measurement means that analyzing big cathode plates for A4 size LiB’s is practical within the production environment.
The X-ray transmission scan creates an image of the material where the shape and size of any metal particles can be distinctly observed.
This provides critical data on the density and size of the contaminants, and the part can be rejected if it is outside of specifications.
XRF analysis of the contaminants describes which elements are included, which gives the user a full understanding of the contaminants present. This can then be matched to the actual performance of the battery.
Process Control
Having verified that the raw materials are in line with specifications for contamination by metal particles, the production process itself may be the next potential route for contaminants to enter.
One way this can occur is from the dust created by the machinery within production. An easy way to verify if equipment and machinery is adding to the issue of contamination is to put a piece of sticky film close to the machine.
The film can be frequently scanned in the EA8000 for amounts of metal particles normally contained in the dust.
Along with discovering the contamination source within the cell of the battery, this method is beneficial to check for possible issues in the machinery itself.
A variation in the type or extent of dust produced could indicate that a part needs to be replaced, or that a service is required.
Failure Analysis
The EA8000 finally provides a solution to assist in discovering the primary cause of battery failure throughout the last testing phase of manufacturing.
It is now possible to analyze products that have failed to understand if any metal particles are evident on the cell separator, or to see if electrodes are present that could have resulted in a short circuit inside of the cell.
XRF compositional analysis will demonstrate precisely which metals are evident, which ultimately allows the user to find out where the contaminants originated from.
The EA8000 can identify metal contaminants early in the process of manufacturing, which helps to increase yield because components which are outside of specifications are excluded before they are employed.
As the tool provides thorough information on the number and size of the metal particles present, specific patterns can be correlated to performance, where only parts that truly increase quality and performance issues are rejected.
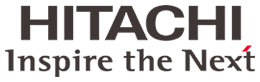
This information has been sourced, reviewed and adapted from materials provided by Hitachi High-Tech Analytical Science.
For more information on this source, please visit Hitachi High-Tech Analytical Science.