The demand for greater performance, a reduction in cost, and more adherence to environmental regulations is driving the creation of new brake formulations.(1,2)
.jpg)
Image Credit: MikiBiz / Shutterstock.com
Importance of Brake Material
A brake material must ultimately meet the requirements of the vehicle for which it is made. It frequently contains upwards of 20 alternate ingredients and requires several processing steps.
It is difficult to simulate on-vehicle braking performance features in an inertia brake dynamometer test, but it has been considered in the past to be even more difficult to do so in a small-scale bench test.
Bruker’s Brake Material Screening Module
The friction behavior of brake material formulations can now be pre-screened before submission to full-scale inertia dynamometer testing, thanks to Bruker’s brake material screening module for the UMT TriboLab platform (Figure 1).
.jpg)
Figure 1. UMT TriboLab benchtop materials screening module with particle collection
The brake material screening module is supplied with a template that translates the majority of the brake-specific conditions from the most commonly used OEM dynamometer tests (such as the AK-Master test or the SAE J2522) to be replicated on the TriboLab system.
The coefficient of friction (COF) is attained for various conditions such as recovery, fade, cold, motorway, speed or pressure sensitivity, burnish, and green. Development time is made much more efficient by these screening tests.
Friction material developers can analyze the impact of several variables, including humidity, temperature, speed, and contact pressure in a highly controlled environment with a high-resolution observation of the data details.
Along with the COF behavior of the latest brake material formulations, recent interest in the development of brake material is also focused on understanding and evaluating the generation of particles (such as the wear debris).
This contemporary aspect of research can additionally be explored with Bruker’s brake particle collection chamber on the TriboLab tester. The particle collection system provides several collection techniques, according to the requirements of the user.
Particles can be acquired on adhesive-backed collection strips (Figure 2), which can be masked at various testing stages, or gathered from the easy-to-clean-and remove bottom tray and chamber, or by using an in-line filter and vacuum pump system for particle separation by size (Figure 3).
.jpg)
Figure 2. Removable chamber with adhesive strips for particle collection during different stages of testing.
.jpg)
Figure 3. Example of particles collected on different size filters from in-line collection set-up.
Particles can be gathered from the chamber when the test has been completed for additional analysis and characterization, or from pre-determined stages during a simulation of a specific dynamometer sequence, for example, the SAE J2522 or AK-Master test.
Researchers can also obtain particles under any self-defined and tailored research test conditions, for example, at particular pressures, temperatures, or speeds.
Figure 4 presents histograms of particle sizes collected after using TriboLab to test low steel (LS) brake material and a non-asbestos organic (NAO) brake material.
.jpg)
.jpg)
Figure 4. Histograms of particle sizes generated from testing two different brake materials.
An example of the various compositions of particles obtained from alternate types of brake pad is displayed in the EDS spectra in Figure 5, gathered from the same LS and NAO brake materials.
.jpg)
Figure 5. Energy Dispersive Spectra of particles collected after testing of NAO-1 (left) and LS-1 (right). Note presence of Si, Zr and Ti in NA-1 spectra compared with L-1, where iron is dominant.
Advantages
The data acquired from the TriboLab benchtop brake screening test module and particle collection setup enables friction material developers and brake manufacturers to reduce overall costs and development time.
They will also enhance efficiency by allowing the user to only choose the materials that offer the greatest performance in the benchtop studies from a range of trial compositions.
Full-scale dynamometer or vehicle stopping tests are reserved for only the most promising compositions as a result of this.
Further advantages are the potential of important studies regarding particle generation and the possible changes of composition that happen throughout braking, using controlled and well-characterized test conditions.
References and Further Reading
- California SB 346, Kehoe. Hazardous materials: motor vehicle brake friction materials, Sept. 27, 2010.
- Washington SB 6557. BRAKE FRICTION MATERIAL-- RESTRICTIONS ON USE, June 10, 2019.
Acknowledgments
Produced from materials originally authored by Steve Shaffer from Bruker.
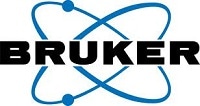
This information has been sourced, reviewed and adapted from materials provided by Bruker Nano Surfaces.
For more information on this source, please visit Bruker Nano Surfaces.