There has never been a more challenging time for stakeholders in the metals industry. Steel plants and foundries are under more and more pressure to utilize scrap materials in the melt.
.png)
Supply chains are becoming more complicated and potentially less reliable. The legislation for trace elements is becoming increasingly strict.
The consequence is that foundries and metals processing companies must analyze and control the materials that enter and exit the facilities to consistently create a high-quality, profitable product that adheres to all specifications and legislation. This can be challenging.
Every element must be tested to meet a materials specification. Contemporary specifications exceed what the majority of mid-range OES analyzers can offer.
High-end OES analyzers are not viable for the majority of users and are not always sufficient for an environment involving high-throughput production. This is where the new OE750 from Hitachi High-Tech offers a competitive edge.
OE750: Designed for Next Level OES Analysis
The OE750 is a pioneering piece of equipment. It is an OES analyzer that functions like any high-end instrument and yet is inexpensive to purchase and run. It is the sole analyzer in its class at the moment that can attain next-level OES analysis, for example:
- The capability to analyze all tramp, residual, treatment, trace, and alloying elements for steel and iron alloys. The OE750 has significantly lower detection limits and can identify Te, Se, Bi, Zn, N, Pb, B, and Sb to less than 10 ppm.
- Adhering to the standards of the updated ASTM E415 test technique for low-alloy and carbon steel and ASTM E1086 standard test technique for the evaluation of stainless steel. Nitrogen levels of less than 10 ppm can be easily detected by the analyzer.
- Enabling aluminum die casters to manage levels of antimony, bismuth, and phosphorus to very low parameters in near eutectic and hypereutectic Al-Si alloys.
The ability to manage these, and alternative trace and tramp elements, enables Al processing facilities to have a greater degree of control when optimizing the melt structure.
- Identify the trace elements present in scrap metal, such as zinc as low as 1 ppm. This is critical when sorting incoming scrap material or recycling automotive parts.
- The evaluation of gases such as oxygen, hydrogen, and nitrogen allows greater control over titanium production.
- The potential to investigate copper anodes in gunmetals, bronzes, plus brass, refineries and alternative copper alloys in foundries.
- Thorough trace elements analysis to enable the PMI testing of incoming materials for high-end metals in forming and machining facilities.
These functions mean that, for the first time, metals processing facilities and foundries do not have to sacrifice performance for the sake of cost.
The OE750 offers advanced OES analysis at a price point that is affordable for scrap metal facilities, metals manufacturers, steel mills, and foundries.
Ultimate Quality Control. No Compromise
The OE750 has the greatest optical resolution in its class and identifies the full range of elements in metal with some of the lowest possible detection limits.
This has been attained through the production of an exclusive optical concept and alternative innovations in technology, for example, an electrical spark discharge source and a new sealed spark stand.
Further advantages, for example, the efficient start-up time and decreased maintenance intervals make sure that the analyzer assists in 100% PMI quality assurance programs and high throughput production.
Find Out More
To discover more about how the OE750 analyzer can take metals testing applications to a new level, get in touch to schedule a demo.
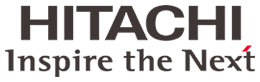
This information has been sourced, reviewed and adapted from materials provided by Hitachi High-Tech Analytical Science.
For more information on this source, please visit Hitachi High-Tech Analytical Science.