Most ultrasonic flaw detection and thickness gaging are carried out at normal temperatures. However, sometimes a hot material requires testing, for example, in process industries. In these instances, tests need to be carried out on hot metal pipes or tanks without shutting them down for cooling.
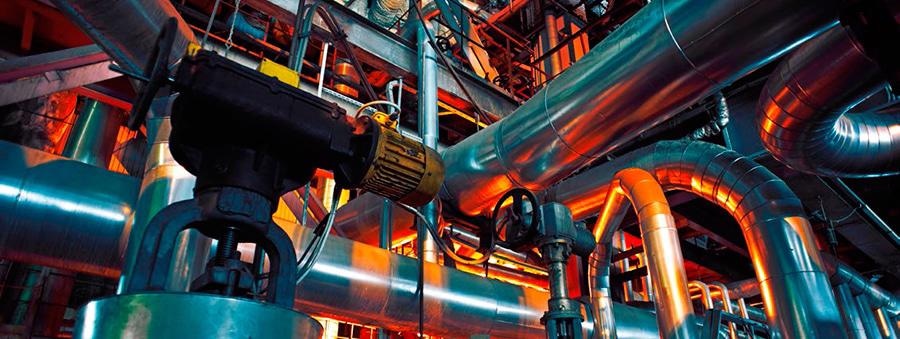
Image Credit: Evident Corporation
Another example is in a manufacturing situation that involves hot materials, such as extruded plastic pipe or thermally molded plastic immediately after fabrication. Conventional ultrasonic transducers can tolerate up to approximately 50 °C (125 °F), but internal disbonding caused by thermal expansion will occur at higher temperatures and can cause permanent damage to the transducers. As such, for materials hotter than 50 °C (125 °F), high-temperature transducers and special test techniques should be utilized.
Below is a brief introduction to available Evident high-temperature transducers and couplants, and important factors regarding their use. Conventional ultrasonic testing of materials at temperatures up to approximately 500 °C (930 °F) is also covered. However, highly specialized waveguide techniques used in research applications fall outside the scope of this article.
Transducers
Evident offers two categories of high-temperature transducers: dual element and delay line. The delay line material (which is internal in the case of duals) in both categories provides thermal insulation between the active transducer element and the hot test surface.
In the standard product line, there are no high-temperature contact or immersion transducers, mainly for design reasons. For both thickness gaging and flaw detection applications, there are high-temperature duals and delay line transducers available. As with all ultrasonic tests, specific test requirements, including the material, thickness range, temperature, and in the case of flaw detection, the type and size of the relevant flaws, determine which transducer is best for a given application.
Thickness Gaging
Corrosion survey work is the most common application for high-temperature thickness gaging. It involves measuring the remaining metal thickness of hot pipes and tanks with instruments such as the 38DL PLUS™ or 45MG thickness gages.
High-temperature use is possible with most of the transducers designed for use with Evident corrosion gages. For example, surfaces as hot as 500 °C (930 °F) can still be tested using D790 series transducers. A complete list of available corrosion gaging duals, including temperature specifications, can be found here.
Any of the standard Microscan™ delay line transducers in the M200 series (including the M202, M206, M207, and M208 gage default transducers) can be equipped with high-temperature delay lines for precision thickness gaging applications using the 38DL PLUS or 45MG thickness gages with single element software.
For surfaces up to 260 °C (500 °F), DLHT-1, -2, and -3 delay lines can be utilized. For surfaces up to 175 °C (350 °F), DLHT-101, -201, and -301 delay lines can be used. The Delay Line Option Chart lists all these delay lines.
When low-frequency transducers are required for increased penetration, the Videoscan™ replaceable face transducers and appropriate high-temperature delay lines can also be used with 38DL PLUS™ and 45MG thickness gages incorporating the HP (high penetration) software option. This will require custom transducer setups.
For surfaces as hot as 480 °C (900 °F), standard delay lines can be used in contact with the surface. Check out Replaceable Face Transducers for a full list of transducers and delay lines.
Flaw Detection
Dual element or delay line transducers are typically used for high-temperature flaw detection just as with high-temperature thickness gaging applications. High-temperature capability is offered by all standard Evident flaw detection duals. In temperatures up to approximately 425 °C (800 °F), fingertip, flush case, and extended range duals, whose frequency is 5 MHz or below, may be used. For temperatures up to approximately 175 °C (350 °F), higher frequency duals (7.5 and 10 MHz) may be used. Read Flaw Detection Duals for a full list of transducers in this category.
In flaw detection applications, the Videoscan replaceable face transducers can all be used with appropriate high-temperature delay lines. For surfaces as hot as 480 °C (900 °F), the available delay lines within this family of transducers can be used in contact with the surface. Check out Replaceable Face Transducers for a full list of transducers and delay lines suitable for various maximum temperatures.
The delay line transducers in the V200 series (most commonly the V202, V206, V207, and V208) are often used for applications involving thin materials. All can be equipped with high-temperature delay lines.
For surfaces up to 260 °C (500 °F), DLHT-1, -2, and -3 delay lines can be used. For surfaces up to 175 °C (350 °F), DLHT-101, -201, and -301 delay lines can be used. The Delay Line Transducer List provides a comprehensive list of these transducers and delay lines.
Special high-temperature wedges for use with angle beam transducers are also available—the ABWHT series for use up to 260 °C (500 °F), and the ABWVHT series for use up to 480 °C (900 °F). Please contact Evident for detailed information on available sizes.
Couplants
If used on surfaces hotter than approximately 100 °C (212 °F), many ultrasonic couplants, such as propylene glycol, glycerin, and ultrasonic gels, will quickly vaporize. As such, specially formulated couplants are required for ultrasonic testing at high temperatures that will remain in a stable liquid or paste form without boiling off, burning, or releasing toxic fumes. It is, therefore, essential that the specified temperature range for their use is strictly adhered to.
Using high-temperature couplants beyond their intended range may result in poor acoustic performance and/or safety hazards.
Even specialized high-temperature couplants must be used quickly at very high temperatures, or they will dry out or solidify and no longer transmit ultrasonic energy. The test surface and the transducer must be clear of any dried couplant residue before the next measurement.
It is typically not possible for normal incidence shear wave coupling at elevated temperatures as commercial shear wave couplants will liquefy and lose the very high viscosity that is necessary for the transmission of shear waves.
Due to the slight possibility of vapor auto-ignition, medium- and high-temperature couplants should not be used in unventilated areas. Please consult for further details.
Evident’ application note on Ultrasonic Couplants provides a comprehensive list of available couplants along with information on each.
Test Techniques
With any high-temperature application, the following factors should always be taken into account when establishing a test procedure:
Duty Cycle
All standard high-temperature transducers are designed with a duty cycle in mind. Lengthy contact with very hot surfaces will cause significant heat buildup regardless of the transducer’s interior delay line insulation. Permanent damage to the transducer will eventually occur if the interior temperature becomes hot enough.
The recommended duty cycle for surface temperatures between approximately 90 °C and 425 °C (200 °F to 800 °F) is no more than ten seconds of contact with the hot surface (five seconds is recommended) for the majority of dual element and delay line transducers. This should be followed by a minimum of one minute of air cooling.
Please note that this is only a guideline; at the upper end of a given transducer’s specified temperature range, the ratio of contact time to cooling time becomes even more critical. Generally, the transducer’s interior temperature can be considered to be reaching a potentially damaging temperature if the transducer’s outer case becomes too hot to comfortably hold with bare fingers. If this happens, the transducer should be allowed to cool down before doing any further testing.
Some inspectors use water to accelerate the cooling process. However, there are no official guidelines published for water cooling by Evident, so it is up to the individual user to determine whether this is appropriate.
Evident EPOCH™ series flaw detectors and all Evident thickness gages can freeze the displayed waveform and reading using the freeze functions. The operator can capture a reading and quickly remove the transducer from the hot surface, making the freeze function very useful for high-temperature measurements. Users can then make internal gain or blanking adjustments on the frozen waveform if required. To help minimize contact time with gages, the fast screen update mode should be used.
Coupling Technique
Operators are required to work quickly due to the combination of transducer duty cycle requirements and the tendency of couplants to solidify or boil off at the upper end of their usable thickness range.
Many users have found that the best technique is to apply a drop of couplant to the face of the transducer before pressing it firmly to the test surface, avoiding any twisting or grinding (which can cause transducer wear). The transducer tip should be clear of any dried couplant residue before carrying out the next set of measurements.
Gain Boost
As with all EPOCH™ series flaw detectors, there are user-adjustable gain boost functions available on the 38DL PLUS™ and 45MG gages. It is often useful to increase gain before making measurements due to the higher attenuation levels associated with high-temperature measurements.
Velocity Variation
Temperature changes the sound velocity in all materials—it slows down as the material heats up. Velocity recalibration is always required for accurate thickness gaging of hot materials.
This velocity change is approximately 1% per 55 °C (100 °F) change in temperature for steel. This will vary depending on the alloy. This change is much greater in plastics and other polymers and can approach 50% per 55 °C (100 °F) change in temperature up to the melting point.
A velocity calibration should be performed on a sample of the test material at the actual test temperature if a temperature/velocity plot is not available for the material. Velocity for known elevated temperatures can be automatically adjusted based on a programmed temperature/velocity constant using the temperature compensation software function in the 38DL PLUS™ gage.
Zero Recalibration
When performing thickness gaging with dual element transducers, the zero offset value for a given transducer will change as it heats up due to changes in transit time through the delay line. As such, it is necessary to carry out periodic re-zeroing to maintain measurement accuracy. This can be done quickly and easily with Evident corrosion gages using their auto-zero function, also referred to as Do-ZERO.
Increased Attenuation
Increasing temperature increases sound attenuation in all materials. This effect is much more pronounced in plastics than in metals or ceramics.
Attenuation of 5 MHz at room temperature is approximately 2 dB per 100 mm one-way sound path (equivalent to a round trip path of 50 mm each way) in typical fine-grained carbon steel alloys.
Attenuation increases to approximately 15 dB per 100 mm of sound path at 500 °C (930 °F). The use of significantly increased instrument gain may be required due to this effect when testing over long sound paths at high temperatures. Adjustment to distance/amplitude correction (DAC) curves or time varied gain (TVG) programs established at room temperature may also be required.
The type of material is very influential on the temperature/attenuation effects in polymers. For steel, it will typically be several times greater than the numbers above. A significant source of total attenuation in a test may be represented with long high-temperature delay lines that have heated up.
Angular Variation in Wedges
Sound velocity in the wedge material will decrease as it heats up with any high-temperature wedge. The refracted angle in metals will increase as the wedge heats up. For any given test, if this is a concern, then the refracted angle should be verified at the actual operating temperature. Practically, thermal variations during testing will often make a precise determination of the actual refracted angle difficult.
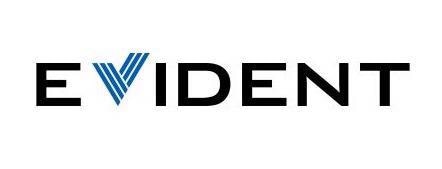
This information has been sourced, reviewed and adapted from materials provided by Evident Corporation.
For more information on this source, please visit https://www.evidentscientific.com/en/