Ceramics are materials which have existed for a long period of time and have since evolved from the materials used to make porcelain. Aside from conventional ceramics seen in art galleries, there are a whole host of technical ceramic materials and piezoceramic materials that are used in sensor applications.
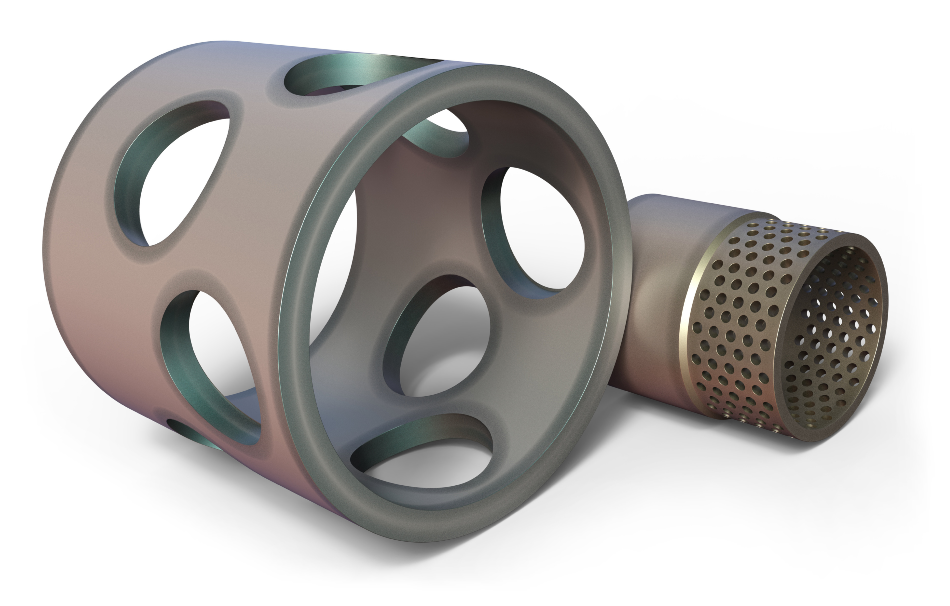
Image Credit: Peter Sobolev/Shutterstock.com
The ceramics used in sensors typically fall into two categories. Those made from conventional (traditional) ceramic materials, typically very tough in nature, and those which are made up of piezoceramic materials which are typically softer, generating an electrical charge when squeezed.
Traditional Ceramics
Traditional ceramics are used in sensors when toughness and durability are required. Given the nature of piezoceramics, traditional ceramic sensors are used when electrical fields are present, due to high electric fields limiting the use of piezoceramics. Traditional ceramics are used in different environments to piezoceramic sensors, often being used in environments where there is more stress and or/heat. This is because sensors made from traditional ceramics tend to have higher resistance to large amounts of stress, are less likely to depolarize under multiple heating cycles, and typically exhibit a lower hysteresis than piezoceramic sensors.
Several ceramic materials can be used in these sensors but require a high temperature tolerance, be robust, have a long usable life, can undergo direct contact with harsh media (especially liquids) and be washable (if they are to be inserted into specific mediums). This has meant that materials such as alumina, zirconia and yttria, as well as toughened/reinforced versions of these materials, have become some of the common materials used as the sensing surface.
They are widely used as temperature and pressure sensors in their application. However, their chemical inertness and ability to be used in a wide range media means they are also used for sensing gases (such as oxygen) and corrosion in different environments, as well as being used in proximity sensing, capacitive sensing, oil level sensors, measuring the flow of harsh chemicals, and monitoring ingredient flows in the food and beverage industry.
Piezoceramics
Due to piezoceramic sensors exhibiting a very useful phenomenon known as the piezoelectric effect, they have become a widespread class of sensors. The piezoelectric effect comes to fruition when a piezoelectric material is subjected to a physical force, as the force causes the charges in the atomic lattice to move to a point where all like charges accumulate at one end of the material, and the opposite like charges accumulate at the opposite end of the material. The result is the generation of an electrical charge across the material that can be detected.
Due to this, there are many piezoelectric and piezoresistive sensors which are made of ceramic materials. One of the main application areas for piezoceramic sensors is physical sensors, such as strain gauges/stress-strain sensors, as the application of a physical force on the ceramic material generates an electrical current which can be detected. However, there are number of physical forces that can generate these currents—such as compression and elongation—meaning that several environments subjected to physical deformations can utilize piezoceramic sensors.
However, it is not just the piezoceramic sensors ability to generate a detectable charge as to why they are a popular ceramic sensor choice. Piezoceramics tend to have greater electromechanical coupling factors, piezoelectric constants, permittivities, and dielectric constants than traditional ceramic sensors, but are not as mechanically robust. In recent years, the evolution of nanomaterials has broadened the scope of piezoceramic sensors. Many inorganic ceramic nanomaterials also exhibit the piezoelectric effect and can be made smaller and thinner than other piezoceramic materials, opening up piezoceramic sensors to new areas of application.
The two ways in which piezoceramics are classified are; active and passive piezoceramic sensors. Active piezoceramic sensors are used to measure the time-of-flight between a transmitter and a receiver. In these cases, the ceramic will be at its resonant frequency, acting as a transmitter, and in an anti-resonant state if acting as a receiver. Specific examples of active piezoceramic sensors include strain gauges on buildings (during construction and after completion), in level sensors, medical ultrasound devices, and flow sensors.
In passive piezoceramic sensors, the ceramics operate below their resonance frequency level, meaning they can be applied across a wide frequency range and for a broader band response. This means passive piezoceramic sensors are well-suited for accelerometer, hydrophone, microphone and musical pick-up applications.
References and Further Reading
CeramTec: https://www.ceramtec.com/applications/piezo-applications/sensor-technology/
CoorsTek: https://www.coorstek.com/english/industries/electronics/sensors/
Servoflo: http://blog.servoflo.com/applications-for-ceramic-pressure-sensors
American Piezo: https://www.americanpiezo.com/apc-materials/apc-materials-for-sensing-applications.html
Disclaimer: The views expressed here are those of the author expressed in their private capacity and do not necessarily represent the views of AZoM.com Limited T/A AZoNetwork the owner and operator of this website. This disclaimer forms part of the Terms and conditions of use of this website.