Polymers have been used in many consumer and industrial areas for many years. They have several advantage compared to metals such as low density, chemical resistance and easy production. However, polymers have generally lower wear and scratch resistance than other materials and therefore these properties must be carefully controlled.
Scratch testing is one of the methods that allow well defined characterization of scratch resistance of polymeric materials, both bulk and coatings such as paints. The scratch technique has therefore found many applications in polymer development, car paints, coatings, etc.
Introduction
Since the beginning of the 20th century polymers found their place in many applications in daily life and industry. Their production is relatively simple and they can be formed into many different shapes. The market of polymers is developing fast and new polymers appear very frequently. Polymers are also coated to improve their surface properties; at the same time, polymers are applied in form of coatings or paint to protect the base (metallic) material or simply to give it the desired color and gloss.
However, polymers are much softer than most metals and ceramics and although they are resistant to many chemicals, they generally do not withstand high temperatures. In addition, being relatively soft, wear and scratch resistance of polymers is lower than that of metals or ceramics. Since many parts and components from polymers are subject to sliding contact with more or less sharp objects, the scratch resistance has to be determined. A typical example of scratching in real life is floor lining or car paint: both these applications require polymeric coating with high resistance to scratching. In the past, many methods (pencil test,
Tabor test, car wash, etc.) have been used for characterization of scratch resistance of polymers. With some exceptions, these methods are usually not well defined, the results are difficult to evaluate and they are often user subjective. The scratch test method on the other hand provides precisely defined conditions of a scratch that can be applied to different materials.
The main results obtained from a scratch test are penetration depth, residual depth, friction force and acoustic emission. The most important information obtained from the scratch test however remains the optical analysis of the scratch: during observation in optical microscope (attached to the scratch tester, with several objectives) the user defines critical loads (loads where different types of failure occur). The critical loads serve for comparison of the adhesion (or cohesion) of the coating or bulk material. In addition, a Panorama image of the entire scratch track can be automatically recorded and saved together with other scratch signals.
Since polymers are often used in bulk form or as paints (thickness >~40 μm) usually scratch resistance and the ability to recover due to viscoelasticity are measured. In case of coated polymers also adhesion of the surface treatment via critical load is determined.
This application report summarizes several applications of scratch testing on polymers and shows the advantages of the scratch tests. Examples of scratch test on car paints, floor lining and heat activated recovery are presented.
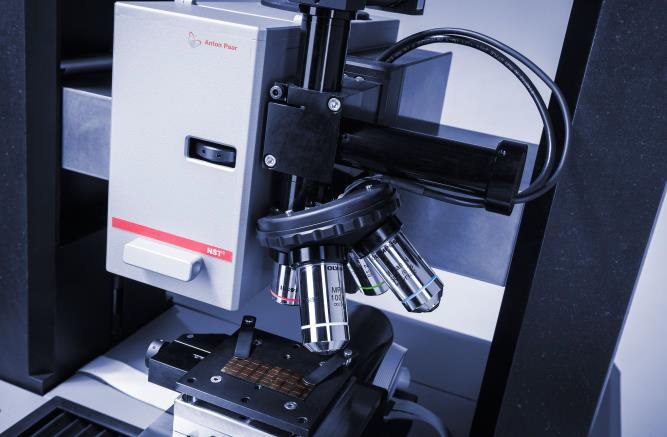
Figure 1. The Nano Scratch Tester for testing of polymers, paints and thin films.
Want to know more? Click here to read the full article.
.jpg)
This information has been sourced, reviewed and adapted from materials provided by Anton Paar GmbH.
For more information on this source, please visit Anton Paar GmbH.