The function of engineered structures is completed by using composite core materials to make up for performance requirements or a specific type of design. The requirements may be reducing weight, adding stiffness, offering energy absorption, or providing impact resistance.
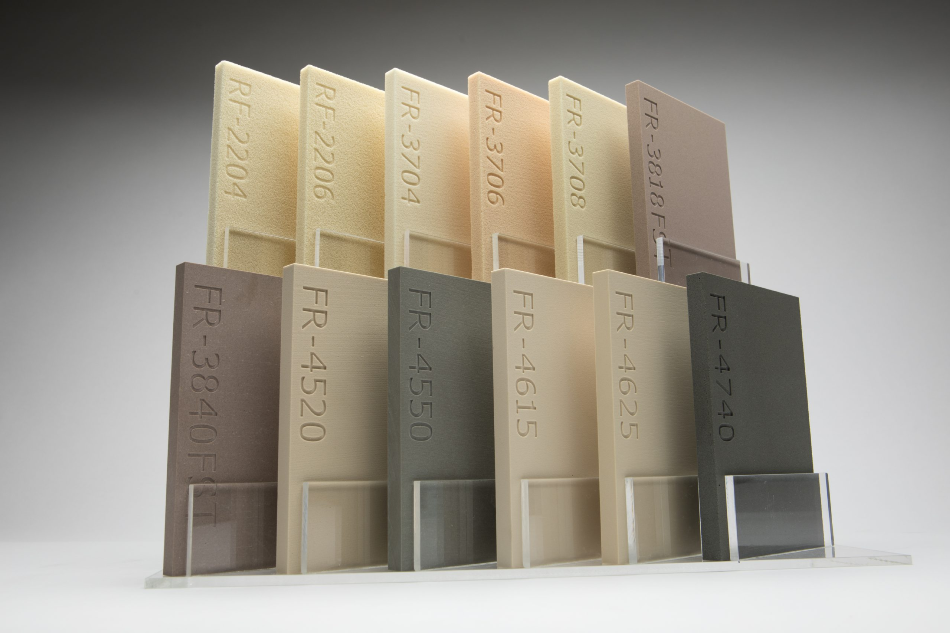
Image Credit: General Plastics Manufacturing
It is important to choose the right kind of composite core material that works as intended and offers the properties specified for users’ applications. However, there are many practical material options available, which make it important to first identify the criteria that have to be met by the material to help narrow down the decision-making process.
In this article, General Plastics covers the various factors that should be taken into consideration when choosing an appropriate composite core material. The company also specifically discusses material compatibility elements, significant processes, and application considerations.
Core Values
The main function of composite core material is to offer stiffness, strength, and continuity across a structure without considerably increasing weight. Whether a core material is over-molded with self-skinning decorative cover/flexible foam or fixed between two composite skins to create a sandwich panel, it acts as the foundation or core member of a structure.
One of the main users of composite materials is the aerospace sector.[i] Composite materials are often used as cargo liners, interior floor and ceiling panels, window surrounds, panels, overhead stowage bins, food and drink trolleys, lavatory modules, galleys, and bulkheads/class dividers.
However, composites are increasingly being used across other different industries such as medical, transportation, marine, etc. In 2019, the U.S. composite end products market was estimated at $26.7 billion and is predicted to increase at a compound annual growth rate (CAGR) of 3.8% in the next five years to reach $33.4 billion by 2025.[ii]
Composite core materials, often recognized for their excellent strength-to-weight ratio, have to be assessed for other properties and qualities like chemicals, moisture, resistance to corrosion, durability, and other environmental exposures. But these qualities rely on the type of material utilized, which makes it exceptionally significant to analyze and select an ideal core material to meet the structural demands. The selection of a core material starts with careful consideration of the manufacturing process, material qualities, and the preferred performance.
Common Composite Core Materials
Balsa
The closed-cell structure of end-grain balsa features elongated, prismatic cells with a length (direction of the grain) measuring around 16 times the diameter. Balsa comes in a scrim-backed block arrangement that conforms to intricate curves, or in sheet form for flat panel construction.
Honeycomb
Honeycomb materials include aluminum, paper, polypropylene, phenolic resin impregnated fiberglass, and aramid fiber phenolic-treated paper. The physical characteristics differ to a large extent with the particular material and density. Extremely lightweight panels can be fabricated using honeycomb cores.
PVC Foam
Polyvinyl chloride, or PVC, foam cores are produced by integrating a polyvinyl copolymer with plasticizers, stabilizers, blowing agents, and cross-linking compounds. PVC foams provide an excellent combination of weight and strength with densities spanning from 4 to 30 lbs/ft3.
Polyurethane Foam
Polyurethane (PU) foams are available in sheets, blocks, or other shapes. At times, PU foams are separately molded into discrete part-shapes. Based on formulation, the foams can be useful for temperatures ranging between 275 °F and 350 °F, and they still retain a significant amount of their toughness and strength. This feature enables them to be utilized in panel applications together with high-temperature curing prepregs, cured in autoclaves or ovens.
Factors to Consider
Generally, design engineers focus on the core material’s end cost, performance or design requirements, and property requirements needed to accommodate those demands. For example, honeycomb is commonly used in composite core panel applications, has an excellent strength to weight ratio, but can be susceptible to moisture and is also on the expensive end of the spectrum
The first important step is to narrow down the properties that are particularly required for the application and assess the cost involved.
Standard types of composite core applications can be divided into two main groups — sandwich panels and shaped cores.
Sandwich Panels
Sandwich panels are utilized in many different applications in a variety of markets, including automotive and aerospace markets. A standard sandwich panel contains lower and upper skins that have a relatively thicker core in the center. The key purpose of the core in the middle of the sandwich panel is to provide as much spacing as possible between the two skins to produce the panel stiffness, introducing as little weight as possible, while simultaneously resisting the forces generated upon loading the structure.[iii]
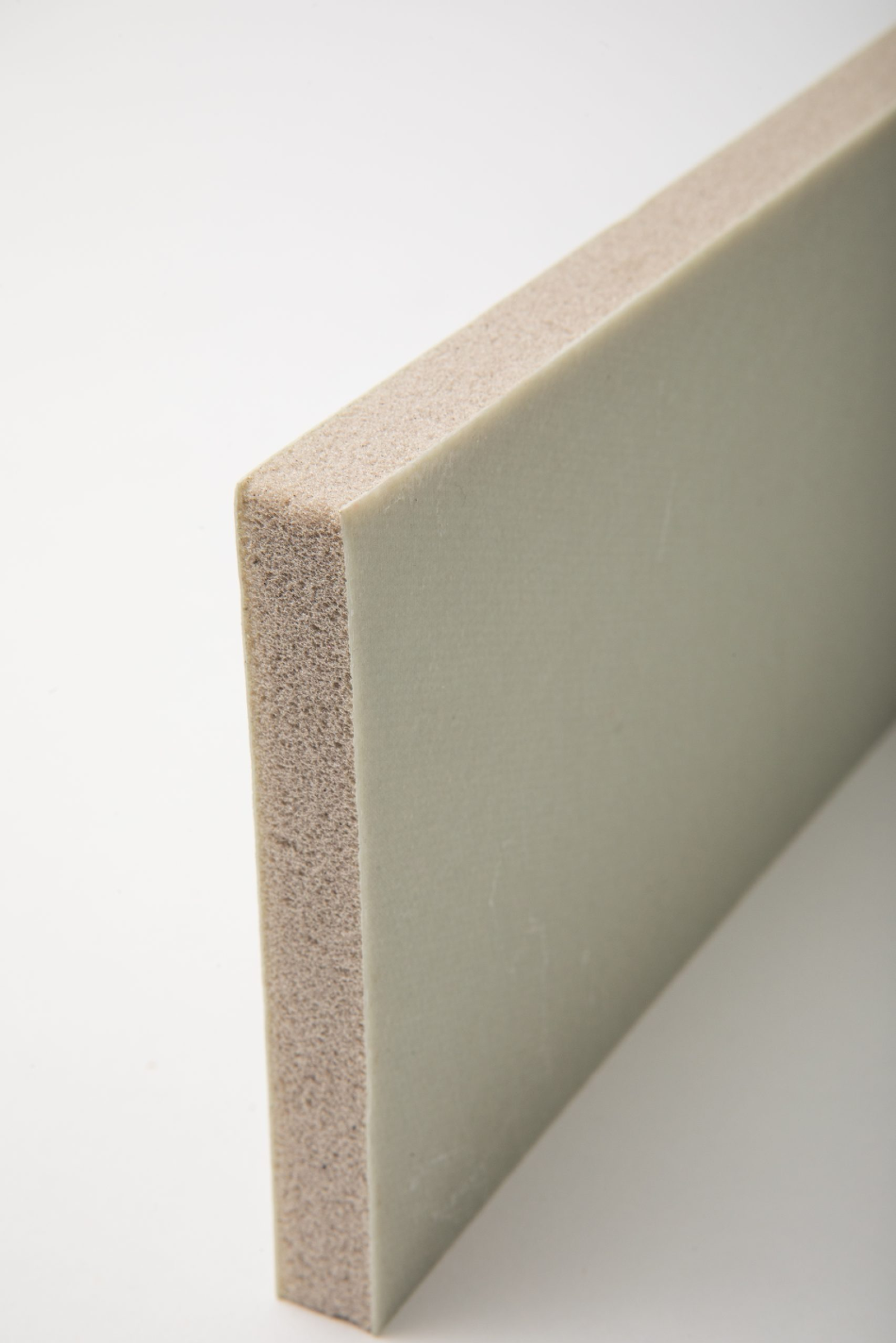
Image Credit: General Plastics Manufacturing
Important Core Material Properties to Consider
Compressive Strength
The compressive strength of a material describes the extent of force that is sustained by a material before it succumbs to the force and breaks or deforms. Certain materials break down at their compressive strength limit, while others deform irreversibly. Therefore, a specified amount of deformation could be regarded as the limit for a compressive load.
Flexural Strength
Flexural strength is the stress sustained by a material just before it yields in a flexure test. Also called bend strength, flexural strength helps to quantify the level of a material’s rigidity
Flexural Modulus
Flexural modulus is the ratio of stress to strain in flexural deformation, or the tendency of a material to resist bending. It is a crucial calculation since it corresponds to a panel’s resistance to deflect when utilized as a structural member.
Shear Strength
Shear strength quantifies the highest amount of stress that can be tolerated by a material before it breaks or tears following the shifting and sliding of layers.
Shear Modulus
Shear modulus is the ratio of shear stress to the shear strain. This feature informs in advance of the level of resistance shown by a material to shearing deformation. If a material is highly resistant to attempted shearing, then it will spread the shear energy very rapidly.[iv]
Peel Strength
Peel strength is utilized to quantify the adhesive strength of two or more materials that have been adhered together, like the core material and two-face sheets inside a sandwich panel.
Application Environment Considerations
Will the panel come in contact with moisture? What kind of environment will it be subjected to? While mechanical properties are crucial, there are important environmental design parameters that can create a problem with the life expectancy of a core material, if not dealt with.
Moisture Resistance
Any panel subjected to high amounts of humidity/condensation and outdoor elements requires a water-resistant core material to prevent rot, saturation, swelling, softening, or bowing of the core. For example, balsa and other kinds of wood core materials may ultimately degrade, swell, or rot with prolonged exposure. It is equally significant to choose a core material that does not support the growth of fungi.
Thermal Conductivity
Thermal conductivity quantifies how a material resists or conducts heat transfer, which is crucial to assess whether the panel has to provide insulating properties or a thermal break.
Chemical and Corrosion Resistance
A material may be exposed to industrial chemicals, solvents, or cleaners, and hence, it is better to look for a material that is resistant to predicted conditions. It should not attract insects and rodents or support fungus.
Flammability
Sandwich panels are often utilized for aircraft interiors, and thus fulfilling the rigorous standards of aerospace for heat release and flame, smoke, and toxicity (FST) is crucial. If a panel is likely to be exposed to fire, it is required to fulfill several requirements to ensure that it will not spread a fire upon potential exposure to a flame.
Is the material self-extinguishing and flame-retardant? Does it have the ability to intumesce to produce a protective carbonaceous char layer that insulates, assists self-extinguishment, and safeguards the material from constant burning?
Weight
In the automotive and aerospace markets, the concept of lightweight has become more and more significant to Tier 1 suppliers, Tier 2 suppliers, and OEMs. Manufacturers are forced to develop new products that fulfill the growing requirements of these industries as well as new government standards. It is important to know the right kind of lightweight core material that also does not compromise the other required performance properties.
Shaped Core
Shaped core — the second group of core applications — utilizes a core material as the base structure that is further covered or over-molded with a performance-enhancing material or cosmetic. Usually, the core material is machined or molded into the required geometry or shape needed by the application. Some examples of shaped core applications are automobile bumpers, winglets, car dashboards, crash pads, glare shields, automotive seatbacks, and headliners.
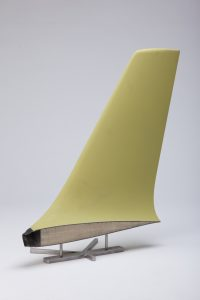
Image Credit: General Plastics Manufacturing
All the factors listed for sandwich panels should be taken into consideration for the shaped core. But there are more energy absorption and impact mitigation-related queries that need to be examined:
- Is the core material load-bearing?
If the shaped core happens to be the load-bearing portion of a structure, then it has to be a very sturdy material that displays high-performance load-bearing behaviors.
- Is the load dynamic or static, will it see impact or movement or should both be taken into consideration?
The speed at which the force is applied, whether it is a rapid force (high strain rate) or build-up of energy (low strain rate), should be assessed.
- Is it meant to absorb energy in a head strike application? Will a semi-rigid or rigid core, over-molded with a decorative cover or softer self-skinning foam fulfill the Head Impact Criterion (HIC) requirements? For example, if crash impact or turbulence occurs aboard an aircraft and makes the pilots fall forward and hit their head on the glare shield pad, the built-in core material should act as a de-lethalization pad and actually crush and absorb the energy, analogous to a bicycle helmet.
Process
Strengthening a bulletproof design and choosing the perfect materials are important to a project’s success. But choosing the right processing technique for certain materials can impact costs, time-to-market, overall product quality, and users’ bottom line.
Standard manufacturing techniques that are used when producing shaped core parts or sandwich panels include:
- Machining/Shaping — In this process, numerous machining methods like CNC machining, cutting, sawing, turning, routing, carving, filing, sanding, etc. are performed. Computer software is used by CNC machining to manage machine tools that cut intricate two-dimensional (2D) and three-dimensional (3D) shapes out of blocks of material. Generally, a CAD drawing or other digital representation of the required part is developed, and the drawing is subsequently translated into instructions (for example, coordination, locations, and speeds) for the CNC machine.
- Bonding — During this procedure, the following features should be taken into consideration: temperature resistance, open cell content, contact surface area, and resin compatibility. Also, materials not designed to operate at high temperatures for long durations may still be capable of withstanding the heat from resin exotherm or short term high-temperature exposure, so don’t mistakenly eliminate materials because of this.
- Resin-Infusion — Resin-infusion is a process in which the layers in an evacuated stack-up of porous materials are infused with a liquid resin. As the resin solidifies, the solid resin matrix attaches the material assembly into a unified stiff composite. This process is very useful to reinforce the core of a sandwich panel. Furthermore, selecting the right kind of resin could considerably enhance the fire resistance of the panel.
- Crush Core — Crush core is a rapid and low-cost process performed at high pressure and temperature, where a cored laminate is positioned in a large press and crushed down to a predefined thickness. Such a process is often used to produce the preferred contour and thickness in a panel.
- Vacuum Bagging — Vacuum bagging is a clamping technique that holds the resin- or adhesive-coated components of a lamination in place using atmospheric pressure. The components are held in place until the adhesive cures. Another method is to add skins or layers to a core material.
- Over molding — In the over molding method, a molded or pre-machined core is placed inside a mold, forming or molding an extra covering around the core to finish the completed part. Shaped core parts that are created in this way can be selectively strengthened where required with hard mounting points, fasteners, backing plates, etc.
Cost
Once users have decided the manufacturing process and core material, they should verify that it is the most economical option for their budget. Several core materials are available that provide a product, and this product may be regarded as over-designed for the application.
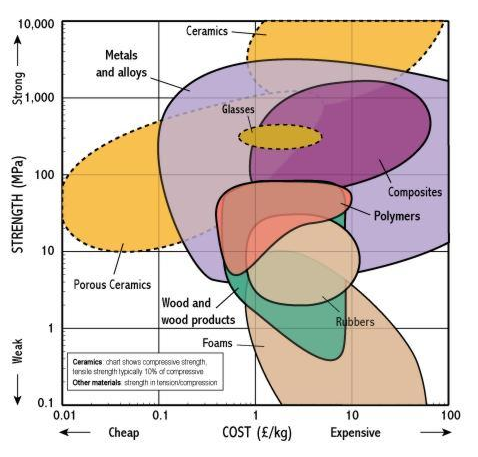
Image Credit: General Plastics Manufacturing
Rather than paying a premium for capabilities that are not required, users should focus on a material that offers the capabilities and properties that meet the required function of their projects.
For example, honeycomb is often utilized in aerospace applications because it is one of the lightest core options available and possesses exceptional fire-resistant properties. But the exposed cutouts and edges of a honeycomb panel are sensitive to moisture ingress if they are not sealed with labor-intensive potting compounds or rigid foam-edge closeouts. Moreover, mounting and fastener sites across the surface of the panel require a substrate that has appropriate fastener pullout strength characteristics.
PU foam is a more cost-effective material to be considered, specifically when the cost of materials is factored in. PU foam has excellent thermal properties and is usually provided in an array of densities.
While certain PVC and PMI foams may also be taken into consideration, they display some changes in shape upon exposure to humidity over time. The core material switch may eventually reduce the materials and processing costs of a company.
Company and Products
General Plastics Manufacturing Company has been producing aircraft assemblies, rigid and flexible rigid polyurethane materials, molded parts, and other specialty foam products for more than seven decades. The company’s LAST-A-FOAM® closed- and open-cell polyurethane foam products offer versatile solutions in the defense, aerospace, marine, construction, nuclear, tooling and molds industries, resulting from chemistry-based solutions and a dedication to quality and excellence.
Core material and finished panels are offered by General Plastics to fulfill the particular requirements of each customer. The company’s composite core products offer long-lasting uniformity and performance over time, are flame-retardant, and provide an excellent alternative to honeycomb, wood, and other core materials.
General Plastics’ product range comprises of core material that meets heat release standards and passes smoke, fire, and toxicity needs for interior aerospace applications.
The LAST-A-FOAM® products offered by General Plastics are non-decaying PU composite cores that support fiberglass laminating. They are strong, durable, lightweight, flame-retardant, very cost-effective, and resistant to chemicals.
The LAST-A-FOAM® composite core materials have been utilized for decades in the automotive and aerospace sectors instead of aluminum, and also used for insulated doors and windows and sports equipment. In the marine sector, composite core foams from General Plastics offer a non-decaying option to wood that supports processes involving fiberglass laminating production.
The LAST-A-FOAM® from General Plastics provides high-strength, low-weight solutions for various manufacturing processes, ranging from the durability of a wing tip to impact resistance needed for a hockey stick blade. Whether users require machined parts or board stock, General Plastics can meet the customers’ exact specifications.
Source: General Plastics Manufacturing
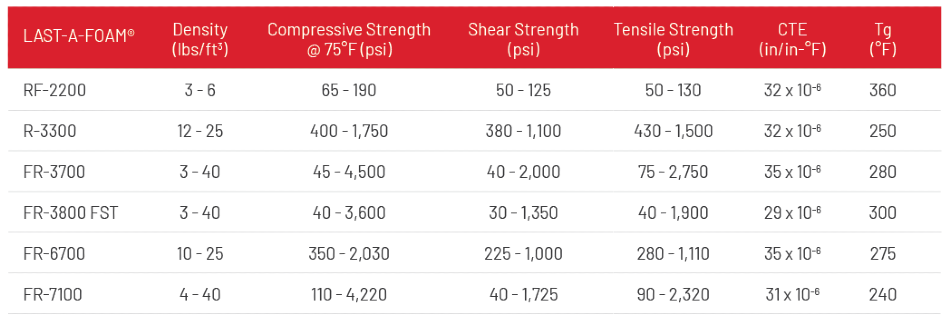
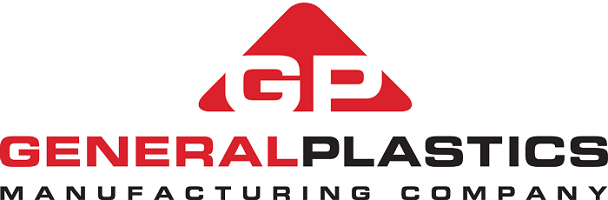
This information has been sourced, reviewed and adapted from materials provided by General Plastics Manufacturing.
For more information on this source, please visit General Plastics Manufacturing.